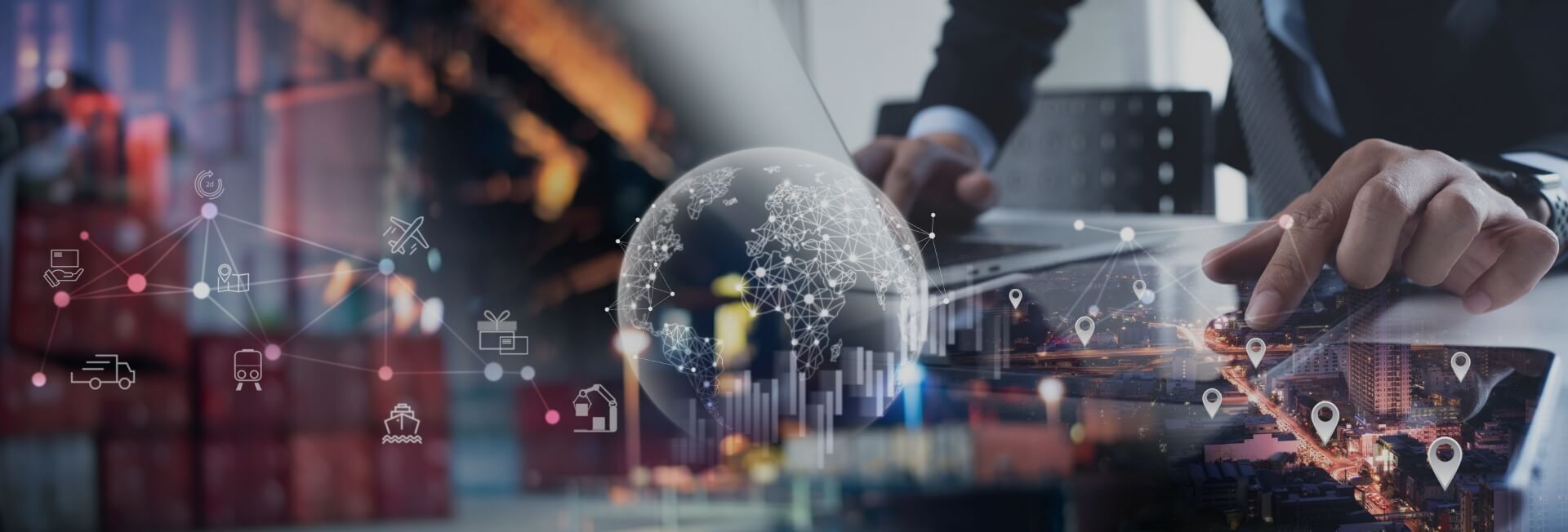
The role of performance measurement in logistics operations
- Home
- Resources
- Transportation Operations
- The role of performance measurement in logistics operations
The Role of Performance Measurement in Logistics Operations
Logistics management is a complex process that involves the planning, implementation, and control of the efficient and effective flow of goods, services, and information from the point of origin to the point of consumption. In today's competitive business landscape, it is essential for companies to constantly evaluate and improve their logistics operations in order to stay ahead of the competition.
The Importance of Logistics Optimization
Logistics optimization is the process of improving the efficiency and effectiveness of logistics operations. It involves analyzing and redesigning the logistics network, streamlining processes, and implementing technological solutions to achieve better results. One of the key factors in logistics optimization is performance measurement. Performance measurement allows companies to evaluate the performance of their logistics operations and identify areas for improvement.
Benefits of Performance Measurement in Logistics
Performance measurement in logistics operations provides several benefits to companies:
1. Supply Chain Optimization: Performance measurement helps companies identify bottlenecks and inefficiencies in their supply chain. By measuring key performance indicators (KPIs) such as on-time delivery, order accuracy, and inventory turnover, companies can identify areas for improvement and take corrective actions to optimize their supply chain.
2. Enhanced Efficiency: Performance measurement allows companies to identify and eliminate wasteful activities in their logistics operations. By measuring KPIs such as transportation costs, warehouse utilization, and order cycle time, companies can identify opportunities for process improvement and cost reduction.
3. Improved Customer Service: Performance measurement helps companies monitor their customer service levels and identify areas for improvement. By measuring KPIs such as order fill rate, order cycle time, and customer complaints, companies can identify gaps in their customer service and take corrective actions to improve customer satisfaction.
4. Better Decision Making: Performance measurement provides companies with the data and insights they need to make informed decisions. By measuring KPIs such as cost per unit, revenue per mile, and return on investment, companies can make data-driven decisions that lead to improved performance and profitability.
Key Performance Indicators in Logistics
There are several key performance indicators that companies can use to measure the performance of their logistics operations:
1. On-Time Delivery: This KPI measures the percentage of orders that are delivered on time. It is a critical indicator of customer service performance and can help companies identify areas for improvement in their transportation and delivery processes.
2. Order Accuracy: This KPI measures the percentage of orders that are delivered without errors. It is an important indicator of order fulfillment accuracy and can help companies identify areas for improvement in their order processing and picking processes.
3. Inventory Turnover: This KPI measures the number of times inventory is sold or used in a given period. It is a key indicator of inventory management efficiency and can help companies identify opportunities to reduce carrying costs and improve cash flow.
4. Transportation Costs: This KPI measures the cost of transporting goods from the point of origin to the point of consumption. It is a critical indicator of transportation efficiency and can help companies identify opportunities to reduce costs and improve profitability.
Implementing Performance Measurement in Logistics
Implementing performance measurement in logistics operations requires a systematic approach:
1. Define Key Performance Indicators (KPIs): The first step is to identify the KPIs that are most relevant to your logistics operations. These KPIs should be aligned with your overall business objectives and should provide insights into the performance of your logistics operations.
2. Collect Data: Once you have defined your KPIs, you need to collect the data required to measure them. This may involve implementing systems and processes to capture relevant data, such as using TMS software for transportation-related KPIs.
3. Analyze and Interpret Data: The next step is to analyze the data and interpret the results. This involves comparing the actual performance against the target performance, identifying trends and patterns, and understanding the root causes of performance issues.
4. Take Corrective Actions: Based on the analysis and interpretation of the data, you need to take corrective actions to address performance issues and improve the performance of your logistics operations. This may involve making changes to your processes, investing in technology, or developing new strategies.
The Role of TMS Software in Performance Measurement
TMS software plays a crucial role in performance measurement in logistics operations. TMS stands for Transportation Management System, and it is a software solution that helps companies manage their transportation operations more effectively.
TMS software provides companies with the tools and capabilities to measure and track key performance indicators related to transportation, such as on-time delivery, carrier performance, and transportation costs. By integrating with other systems and data sources, TMS software can provide real-time visibility into the performance of transportation operations and help companies make data-driven decisions.
Some of the key features of TMS software that support performance measurement include:
1. Carrier Relationship Management: TMS software allows companies to manage their relationships with carriers more effectively. It provides tools for tracking carrier performance, managing contracts and rates, and monitoring carrier compliance. By measuring carrier performance, companies can identify underperforming carriers and take corrective actions.
2. Transportation Optimization: TMS software helps companies optimize their transportation operations by providing tools for route planning, load optimization, and mode selection. By measuring transportation costs and efficiency, companies can identify opportunities for cost reduction and process improvement.
3. TMS Integration: TMS software can integrate with other systems and data sources, such as ERP systems, warehouse management systems, and IoT devices. This integration allows companies to capture and analyze data from multiple sources and gain a holistic view of their logistics operations.
4. Automation: TMS software automates several manual tasks and processes, such as carrier selection, load tendering, and freight audit and payment. This automation improves efficiency, reduces errors, and provides real-time visibility into the performance of transportation operations.
Conclusion
Performance measurement plays a crucial role in optimizing logistics operations and improving efficiency in the supply chain. By measuring key performance indicators such as on-time delivery, order accuracy, and transportation costs, companies can identify areas for improvement and take corrective actions to optimize their logistics operations.
TMS software provides companies with the tools and capabilities to measure and track key performance indicators related to transportation. By integrating with other systems and data sources, TMS software can provide real-time visibility into the performance of transportation operations and help companies make data-driven decisions.
In today's competitive business landscape, companies that effectively measure and optimize their logistics operations will gain a competitive edge and achieve higher levels of customer satisfaction and profitability.