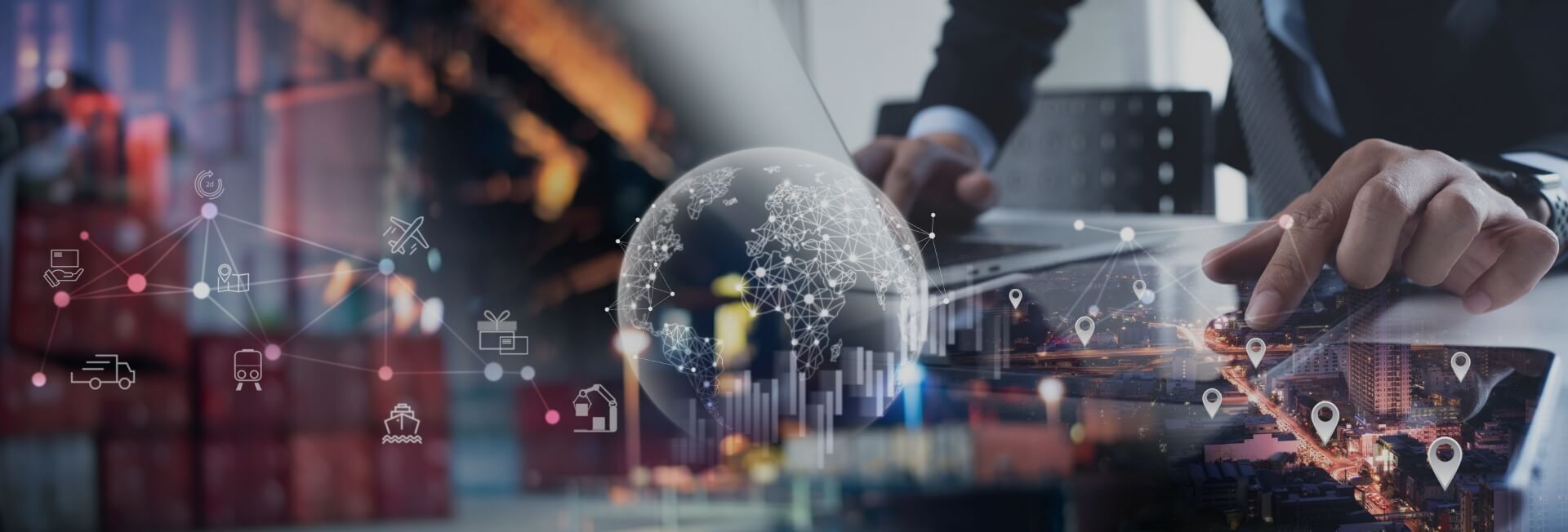
The importance of quality management in logistics operations
- Home
- Resources
- Transportation Operations
- The importance of quality management in logistics operations
The Importance of Quality Management in Logistics Operations
In today's fast-paced and competitive business environment, efficient logistics operations are crucial for success. The ability to deliver products and services to customers in a timely manner can make or break a company's reputation. One way to ensure smooth and efficient logistics operations is through effective quality management. By implementing quality management practices, businesses can optimize their supply chain, enhance customer satisfaction, and gain a competitive edge in the market.
Logistics Management and Quality Management
Logistics management involves the planning, implementing, and controlling of the flow and storage of goods, services, and information from the point of origin to the point of consumption. It encompasses activities such as transportation, warehousing, inventory management, packaging, and order fulfillment. Quality management, on the other hand, focuses on ensuring that products and services consistently meet or exceed customer expectations.
Integrating quality management principles into logistics operations can help businesses identify and eliminate inefficiencies, reduce costs, and improve overall performance. It involves implementing quality control measures at every stage of the supply chain, from sourcing raw materials to delivering the final product to the customer.
Benefits of Quality Management in Logistics Operations
Implementing quality management practices in logistics operations offers a range of benefits for businesses:
1. Improved Efficiency and Productivity
Quality management helps identify bottlenecks and streamline processes, resulting in improved efficiency and productivity. By analyzing data and identifying areas for improvement, businesses can eliminate waste, reduce lead times, and optimize their supply chain.
2. Enhanced Customer Satisfaction
Quality management ensures that products and services meet or exceed customer expectations. By consistently delivering high-quality products on time, businesses can enhance customer satisfaction and loyalty. Satisfied customers are more likely to become repeat customers and recommend the company to others.
3. Cost Reduction
Implementing quality management practices can lead to cost reduction in logistics operations. By identifying and eliminating inefficiencies, businesses can reduce waste, minimize rework, and optimize their use of resources. This can result in significant cost savings and improved profitability.
4. Competitive Advantage
Quality management can give businesses a competitive advantage in the market. By consistently delivering high-quality products and services, businesses can differentiate themselves from competitors and attract more customers. A strong reputation for quality can also help businesses win new contracts and partnerships.
Implementing Quality Management in Logistics Operations
Implementing quality management in logistics operations requires a systematic and structured approach. Here are some key steps to consider:
1. Set Quality Objectives
Define clear quality objectives for your logistics operations. These objectives should be specific, measurable, achievable, relevant, and time-bound (SMART). They should align with your overall business goals and customer expectations.
2. Establish Quality Control Measures
Implement quality control measures at every stage of the supply chain to ensure that products and services meet the required quality standards. This may involve conducting regular inspections, performing quality tests, and monitoring key performance indicators (KPIs).
3. Monitor and Analyze Performance
Regularly monitor and analyze performance data to identify areas for improvement. Use data analytics tools to gain insights into your logistics operations and make data-driven decisions. Continuously track key metrics such as on-time delivery, order accuracy, and customer satisfaction.
4. Implement Continuous Improvement Initiatives
Encourage a culture of continuous improvement within your organization. Empower employees to identify and suggest improvements in logistics operations. Implement lean methodologies and tools such as Six Sigma to eliminate waste and reduce variation.
5. Foster Collaboration with Suppliers and Partners
Collaborate closely with your suppliers and partners to ensure quality throughout the supply chain. Establish clear quality requirements and standards, and regularly communicate and monitor performance. Build strong relationships based on trust and mutual understanding.
Conclusion
Quality management plays a vital role in optimizing logistics operations. By implementing effective quality management practices, businesses can enhance efficiency, improve customer satisfaction, reduce costs, and gain a competitive advantage. It requires a systematic and structured approach, with a focus on setting clear objectives, implementing quality control measures, monitoring performance, and fostering collaboration with suppliers and partners. By prioritizing quality management, businesses can ensure smooth and efficient logistics operations, ultimately leading to business success.