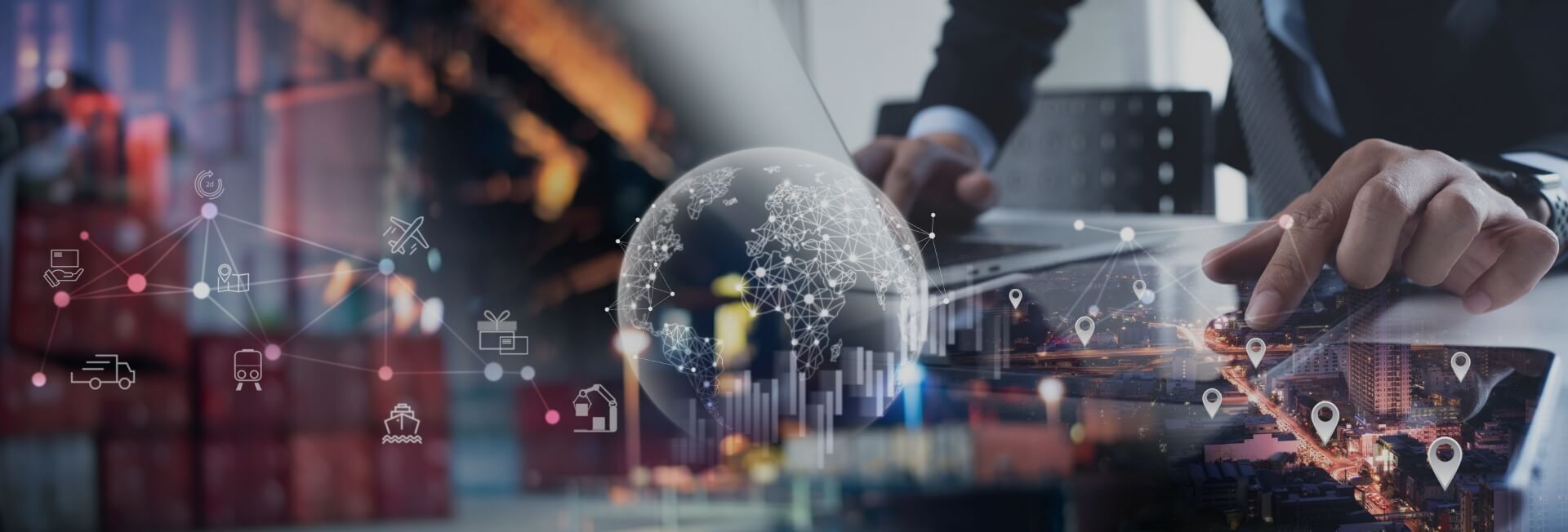
The importance of continuous improvement in supply chain optimization
- Home
- Resources
- Transportation Operations
- The importance of continuous improvement in supply chain optimization
Introduction
In today's highly competitive business landscape, supply chain optimization has become a critical factor for success. Companies are constantly seeking ways to improve their supply chain operations to reduce costs, enhance efficiency, and deliver better customer experiences. One of the key strategies that companies can employ to achieve these goals is continuous improvement.
What is Continuous Improvement?
Continuous improvement, also known as continuous process improvement or continuous quality improvement, is an ongoing effort to enhance products, services, or processes. It is a systematic approach that involves identifying areas for improvement, implementing changes, and evaluating the results. Continuous improvement is not a one-time project but a mindset that encourages organizations to constantly strive for excellence.
The Role of Continuous Improvement in Supply Chain Optimization
Supply chain optimization is the process of improving the efficiency and effectiveness of a company's supply chain operations. It involves streamlining processes, reducing costs, and enhancing customer satisfaction. Continuous improvement plays a crucial role in supply chain optimization by providing a structured framework for identifying and addressing inefficiencies and bottlenecks.
Benefits of Continuous Improvement in Supply Chain Optimization
Implementing continuous improvement practices in supply chain optimization can yield numerous benefits for businesses. Here are some of the key advantages:
1. Increased Efficiency
Continuous improvement helps identify and eliminate inefficiencies in supply chain processes. By analyzing the entire supply chain and identifying areas for improvement, companies can streamline their operations, reduce waste, and enhance overall efficiency. This leads to faster order fulfillment, improved on-time delivery, and reduced lead times, resulting in a more efficient and responsive supply chain.
2. Cost Reduction
Continuous improvement allows companies to identify cost-saving opportunities in their supply chain. By optimizing processes, reducing waste, and eliminating non-value-added activities, companies can significantly reduce their operating costs. This can be achieved through automation, improved inventory management, better transportation routing, and other efficiency-enhancing measures. As a result, companies can achieve cost savings and improve their bottom line.
3. Enhanced Customer Satisfaction
Customer satisfaction is a key driver of business success. Continuous improvement helps companies deliver better customer experiences by reducing lead times, improving order accuracy, and enhancing overall service quality. By optimizing the supply chain, companies can ensure timely delivery, minimize stock-outs, and provide superior customer service. This leads to increased customer satisfaction, loyalty, and repeat business.
4. Competitive Advantage
In today's hyper-competitive business environment, companies need to constantly innovate and improve to stay ahead of the competition. Continuous improvement in supply chain optimization can provide a significant competitive advantage by enabling companies to deliver products faster, at lower costs, and with higher quality. It allows companies to respond quickly to changing customer demands, market trends, and industry disruptions, giving them a competitive edge.
Implementing Continuous Improvement in Supply Chain Optimization
Implementing continuous improvement practices in supply chain optimization requires a systematic approach. Here are some steps that companies can follow:
1. Analyze the Current State
The first step in implementing continuous improvement is to analyze the current state of the supply chain. This involves mapping out the entire supply chain process, identifying key bottlenecks and inefficiencies, and collecting relevant data. By understanding the current state, companies can identify areas for improvement and set specific improvement goals.
2. Set Improvement Goals
Once the current state analysis is complete, companies need to set clear improvement goals. These goals should be specific, measurable, achievable, relevant, and time-bound (SMART). For example, a goal could be to reduce order lead time by 20% within six months. Setting clear goals helps focus the improvement efforts and provides a benchmark for evaluating the effectiveness of the improvements.
3. Identify Improvement Opportunities
After setting improvement goals, companies need to identify specific improvement opportunities. This can be done through various techniques such as value stream mapping, process mapping, and root cause analysis. By involving cross-functional teams and gathering input from employees at all levels, companies can identify potential areas for improvement and generate innovative ideas.
4. Implement Changes
Once improvement opportunities are identified, companies can start implementing changes. This may involve implementing new technologies, automating manual processes, redesigning workflows, or reorganizing the supply chain network. The key is to implement changes in a systematic and controlled manner, ensuring that the improvements are sustainable and aligned with the overall business strategy.
5. Monitor and Evaluate
Continuous improvement is an ongoing process that requires regular monitoring and evaluation. Companies should establish key performance indicators (KPIs) to track the progress of the improvements. This may include metrics such as on-time delivery, order accuracy, inventory turnover, and customer satisfaction. By monitoring the KPIs, companies can assess the effectiveness of the improvements and make necessary adjustments.
Conclusion
Continuous improvement is a powerful strategy for supply chain optimization. By embracing a culture of continuous improvement, companies can achieve increased efficiency, cost reduction, enhanced customer satisfaction, and a competitive advantage. Implementing continuous improvement practices requires a systematic approach and a commitment to ongoing evaluation and adjustment. Companies that prioritize continuous improvement in their supply chain operations are well-positioned to succeed in today's dynamic business environment.