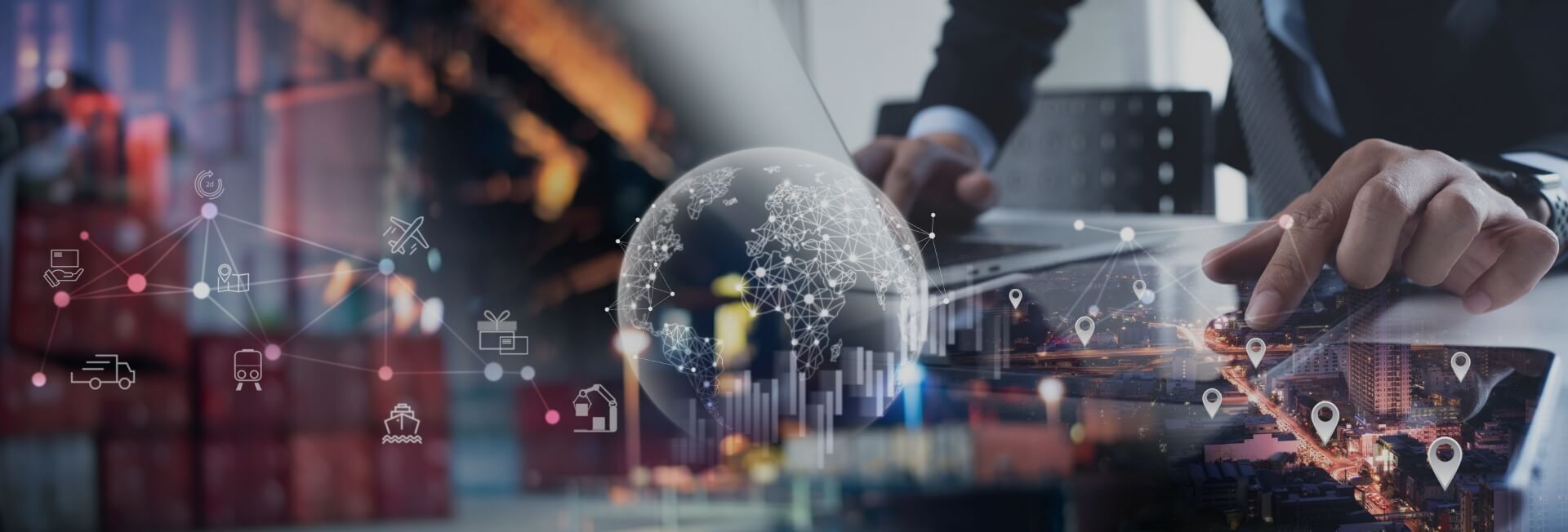
The impact of automated supply chain on reducing order fulfillment time and improving customer experience
- Home
- Resources
- Transportation Operations
- The impact of automated supply chain on reducing order fulfillment time and improving customer experience
Introduction
In today's fast-paced and highly competitive business environment, efficient supply chain management is crucial for the success of any company. The ability to deliver goods quickly and accurately to customers is no longer a luxury but a necessity. With the advent of technology, automated supply chain systems have emerged as a game-changer in the logistics industry, drastically reducing order fulfillment time and improving the overall customer experience.
The Need for Automated Supply Chain
Traditional supply chain management processes involved multiple manual steps, which were both time-consuming and prone to errors. From order placement to inventory management, every task required human intervention, leading to delays and inefficiencies. Moreover, the lack of real-time visibility into the supply chain made it difficult for companies to respond quickly to customer demands and market changes.
Enter automated supply chain management. By integrating technology into every aspect of the supply chain, companies can streamline operations, reduce costs, and enhance customer satisfaction. From automated order processing to real-time tracking, these systems offer a wide range of benefits that can revolutionize the logistics industry.
Reducing Order Fulfillment Time
One of the primary advantages of automated supply chain management is the significant reduction in order fulfillment time. With manual processes, it can take days or even weeks to process an order, leading to delays in delivery and dissatisfied customers. However, with automated systems, orders can be processed in a matter of minutes, ensuring quick dispatch and timely delivery.
Automated systems can also optimize the picking, packing, and shipping processes, reducing the time required to fulfill an order. By using advanced algorithms and real-time data, these systems can identify the most efficient routes, allocate the right resources, and minimize downtime, resulting in faster order fulfillment and improved customer satisfaction.
Improving Customer Experience
With the rise of e-commerce, customer expectations have skyrocketed. Customers now demand fast, accurate, and transparent delivery of their orders. Automated supply chain management plays a crucial role in meeting these expectations by providing real-time visibility into the entire order fulfillment process.
Automated systems offer features such as order tracking, automated notifications, and personalized delivery options, allowing customers to stay informed about the status of their orders. This transparency not only enhances the overall customer experience but also builds trust and loyalty.
Streamlining Logistics Operations
Automated supply chain systems can streamline logistics operations by eliminating manual tasks and optimizing processes. For example, TMS (Transportation Management System) software can automate the entire transportation planning and execution process, from carrier selection to route optimization.
By integrating TMS software into the supply chain, companies can reduce transportation costs, improve delivery efficiency, and enhance carrier relationship management. These systems use advanced algorithms to analyze various factors such as carrier performance, transit times, and cost structures to make data-driven decisions and optimize the transportation process.
Supply Chain Optimization
Automated supply chain systems enable companies to optimize their supply chain by analyzing vast amounts of data and making informed decisions. These systems can collect data from various sources such as inventory levels, demand forecasts, and production schedules, and use advanced analytics to identify bottlenecks, anticipate demand fluctuations, and optimize inventory levels.
By optimizing the supply chain, companies can reduce costs, improve operational efficiency, and enhance customer satisfaction. For example, by using demand forecasting algorithms, companies can ensure that the right products are available at the right time, reducing stockouts and lost sales opportunities.
TMS Integration for Carrier Management
Transportation Management System (TMS) software plays a crucial role in carrier management by automating processes such as carrier selection, contract management, and performance tracking. By integrating TMS software into the supply chain, companies can effectively manage their carrier relationships and ensure optimal performance.
TMS software enables companies to track carrier performance metrics such as on-time delivery, transit times, and claims ratio. By analyzing this data, companies can identify underperforming carriers and take corrective actions. Moreover, TMS software can also automate the settlement process, ensuring accurate and timely payments to carriers.
TMS Cost Reduction and Savings
Automated supply chain systems, particularly TMS software, can significantly reduce transportation costs and generate cost savings for companies. By optimizing routes, consolidating shipments, and reducing empty miles, TMS software can minimize fuel consumption and improve resource utilization.
TMS software can also help companies negotiate better rates with carriers by providing accurate data on shipping volumes, transit times, and historical performance. By leveraging this data during contract negotiations, companies can secure favorable rates and reduce transportation costs.
Conclusion
The revolution of automated supply chain management has transformed the logistics industry, enabling companies to reduce order fulfillment time, improve customer experience, streamline operations, and optimize their supply chain. By embracing technology and integrating automated systems into their supply chain, companies can stay ahead of the competition and meet the ever-increasing customer expectations.