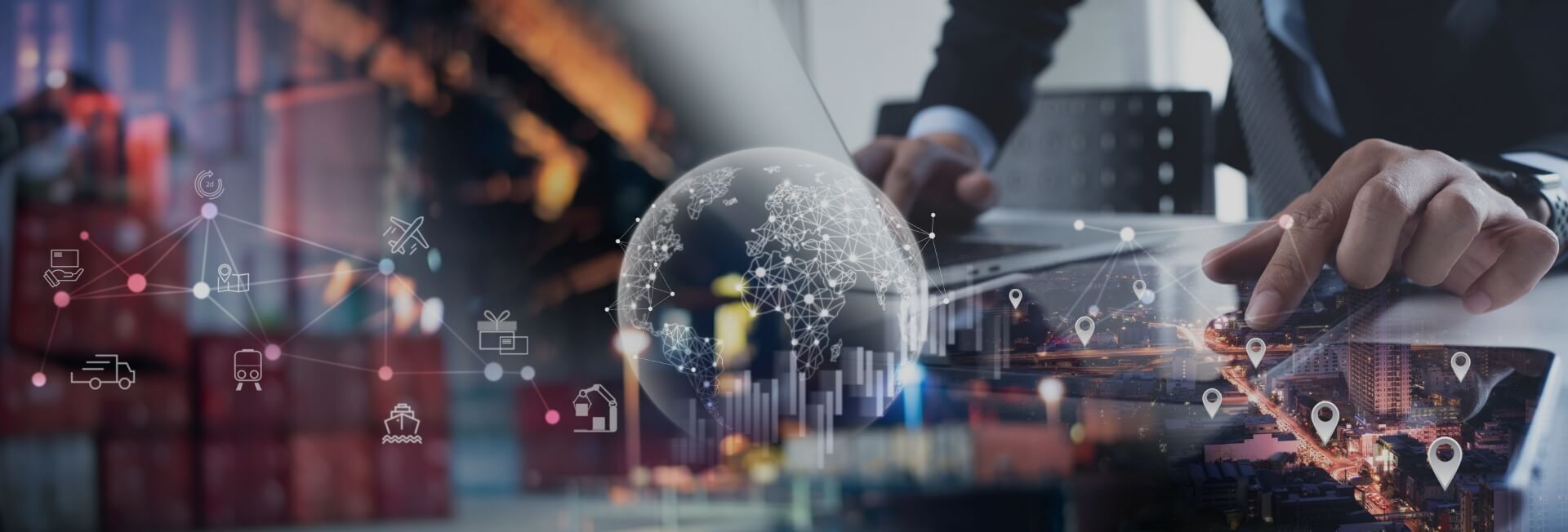
The impact of automated returns processing in reverse logistics
- Home
- Resources
- Transportation Operations
- The impact of automated returns processing in reverse logistics
Introduction
Reverse logistics, the process of managing product returns and the flow of materials back through the supply chain, is an essential aspect of modern business operations. With the rise of e-commerce and online shopping, reverse logistics has become even more critical as businesses need to efficiently handle returns and exchanges to maintain customer satisfaction. In recent years, automated returns processing has emerged as a game-changer in reverse logistics, offering numerous benefits and streamlining operations. This article will explore the impact of automated returns processing in reverse logistics and how it can revolutionize the supply chain industry.
The Challenges of Traditional Returns Processing
Traditionally, returns processing has been a labor-intensive and time-consuming task for businesses. Manual handling of returned products not only leads to increased costs but also introduces the risk of errors and delays. Without automated systems in place, businesses often struggle to keep track of returned items, leading to inventory discrepancies and customer dissatisfaction. Additionally, the lack of visibility into the returns process makes it difficult to identify patterns and trends, hindering the ability to make data-driven decisions to improve the reverse logistics process.
The Benefits of Automated Returns Processing
Automated returns processing offers several advantages over traditional methods, enabling businesses to streamline operations and improve efficiency. Here are some key benefits:
1. Enhanced Visibility and Tracking
With automated returns processing systems, businesses have real-time visibility into the status of returned items. Each returned product is assigned a unique identifier, allowing for seamless tracking throughout the reverse logistics process. This enhanced visibility enables businesses to identify bottlenecks, monitor trends, and make data-driven decisions to optimize the returns process. By leveraging advanced analytics and reporting capabilities, businesses can gain valuable insights into customer behavior and preferences, helping them improve product quality and customer satisfaction.
2. Reduced Processing Time
Automated returns processing significantly reduces the time required to process returned items. Manual handling of returns often involves multiple touchpoints and manual data entry, leading to delays and potential errors. With automation, returned products can be quickly scanned, identified, and sorted, minimizing processing time and improving overall efficiency. This not only speeds up the returns process but also allows businesses to quickly restock returned items or initiate exchanges, enhancing customer satisfaction.
3. Improved Accuracy and Error Reduction
Manual returns processing is prone to errors, such as misidentifying returned products or incorrectly updating inventory records. These errors can have a significant impact on business operations, leading to inventory discrepancies and customer dissatisfaction. Automated returns processing minimizes the risk of errors by eliminating manual data entry and utilizing barcode scanning technology. By accurately identifying returned items and automatically updating inventory records, businesses can ensure inventory accuracy and provide a seamless returns experience for customers.
4. Cost Savings
Implementing automated returns processing systems can result in significant cost savings for businesses. By reducing processing time and improving accuracy, businesses can minimize labor costs associated with manual returns handling. Additionally, the enhanced visibility and tracking capabilities enable businesses to identify inefficiencies and make informed decisions to optimize the reverse logistics process. This optimization can lead to cost reductions in transportation, inventory management, and overall supply chain operations. With automated returns processing, businesses can achieve greater efficiency and cost savings while maintaining customer satisfaction.
Conclusion
Automated returns processing has revolutionized the reverse logistics process, offering businesses enhanced visibility, reduced processing time, improved accuracy, and cost savings. By leveraging advanced technologies such as barcode scanning and data analytics, businesses can streamline operations, optimize the supply chain, and maintain customer satisfaction. As e-commerce continues to grow, the importance of efficient reverse logistics and automated returns processing will only increase. Businesses that embrace automation in their returns processing will gain a competitive edge in the market and be better equipped to meet the evolving demands of customers.