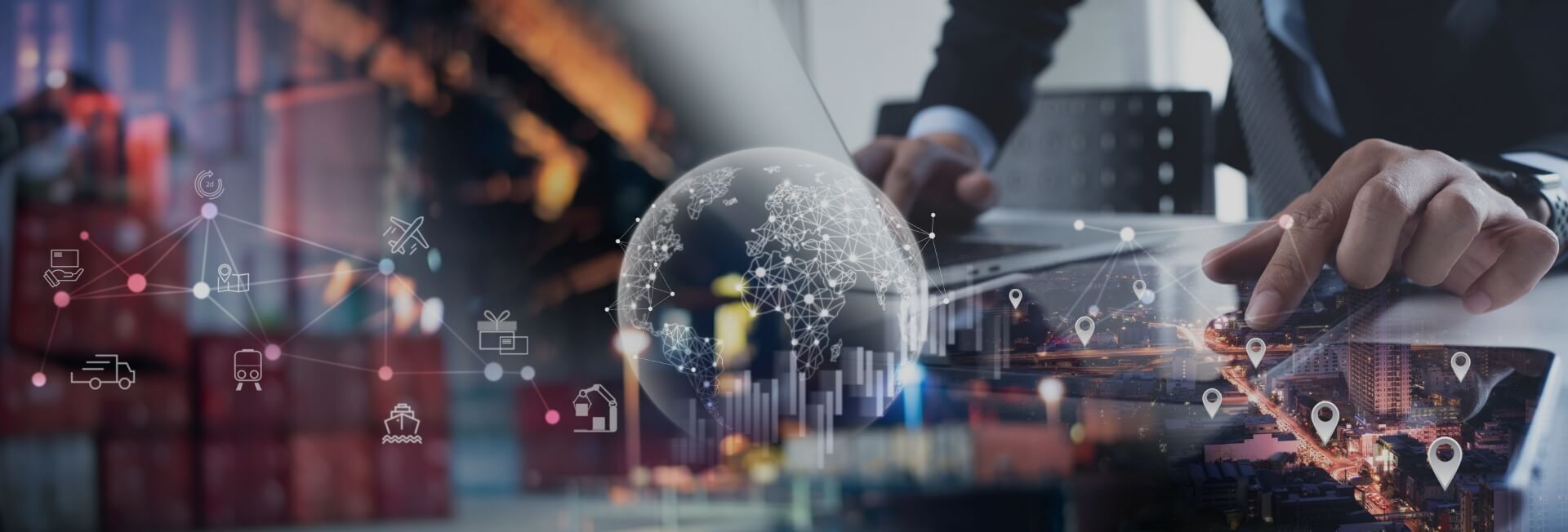
The challenges of reverse logistics and how to streamline the process
- Home
- Resources
- Transportation Operations
- The challenges of reverse logistics and how to streamline the process
The Challenges of Reverse Logistics and How to Streamline the Process
Reverse logistics is the process of managing the return of products from the customer to the manufacturer or retailer. Unlike forward logistics, which deals with the flow of goods from the manufacturer to the customer, reverse logistics involves the flow of goods in the opposite direction. This can include returns, repairs, recalls, and recycling. While reverse logistics is an essential part of the supply chain, it can be a complex and challenging process. In this article, we explore the various challenges faced in reverse logistics and provide tips on how to streamline the process for maximum efficiency.
The Challenges of Reverse Logistics
1. Limited Visibility and Control:
One of the main challenges of reverse logistics is the limited visibility and control over the return process. Unlike forward logistics, where the flow of goods is relatively straightforward, reverse logistics involves multiple touchpoints and stakeholders, making it difficult to track and manage. This lack of visibility and control can result in delays, inefficiencies, and increased costs.
2. Complex Returns Management:
Returns management is a critical component of reverse logistics. However, it can be a complex process due to the varying reasons for returns, such as product defects, customer dissatisfaction, or incorrect orders. Each return requires careful assessment, categorization, and disposition, which can be time-consuming and labor-intensive.
3. Inventory Management:
In reverse logistics, managing inventory can be challenging. Returned products often need to be inspected, repaired, or refurbished before they can be resold or returned to the manufacturer. This requires efficient inventory management to ensure that returned products are properly tracked, stored, and processed.
4. Cost Management:
Reverse logistics can be costly, with expenses arising from transportation, warehousing, inspection, repair, and customer service. Additionally, there may be additional costs associated with product disposal or recycling. Managing and minimizing these costs is essential for efficient reverse logistics operations.
How to Streamline the Reverse Logistics Process
1. Implement a TMS Software:
A Transportation Management System (TMS) software can greatly streamline the reverse logistics process. TMS software provides real-time visibility and control over the return process, allowing for better tracking and management. It also enables automated workflows and notifications, reducing manual intervention and improving efficiency.
2. Optimize Supply Chain:
Supply chain optimization is crucial for efficient reverse logistics. By analyzing and optimizing the supply chain, companies can identify and address bottlenecks, streamline processes, and reduce costs. This can be achieved through the use of advanced analytics, automation, and integration with other systems.
3. Automate Processes:
Automation plays a key role in streamlining reverse logistics. By automating processes such as returns authorization, inspection, and disposition, companies can reduce manual errors, improve efficiency, and speed up the overall return process. Automation can also help in managing inventory, tracking shipments, and generating reports.
4. Improve Carrier Management:
Effective carrier management is essential for efficient reverse logistics. By establishing strong relationships with carriers, companies can ensure timely pickup and delivery of returned goods. Carrier relationship management tools and systems can help in tracking carrier performance, managing contracts, and resolving any issues that may arise.
The Benefits of Streamlining Reverse Logistics
Streamlining the reverse logistics process offers several benefits:
1. Improved Customer Satisfaction:
A streamlined reverse logistics process ensures faster and more efficient returns, leading to improved customer satisfaction. Customers appreciate hassle-free returns and quick resolutions to their concerns.
2. Cost Reduction:
Streamlining reverse logistics helps in reducing costs associated with transportation, warehousing, and processing of returned goods. By optimizing processes and minimizing manual intervention, companies can achieve significant cost savings.
3. Enhanced Sustainability:
Efficient reverse logistics promotes sustainability by enabling proper disposal, recycling, and refurbishment of returned products. This reduces waste and helps in minimizing the environmental impact.
4. Increased Operational Efficiency:
Streamlining reverse logistics improves overall operational efficiency by reducing delays, errors, and inefficiencies. This allows companies to focus on core business activities and allocate resources more effectively.
Conclusion
Reverse logistics can be a complex and challenging process, but with the right strategies and tools, companies can streamline the process for maximum efficiency. Implementing a TMS software, optimizing the supply chain, automating processes, and improving carrier management are key steps towards achieving this goal. By streamlining reverse logistics, companies can improve customer satisfaction, reduce costs, enhance sustainability, and increase operational efficiency. It's time to embrace the challenges of reverse logistics and turn them into opportunities for growth and improvement.