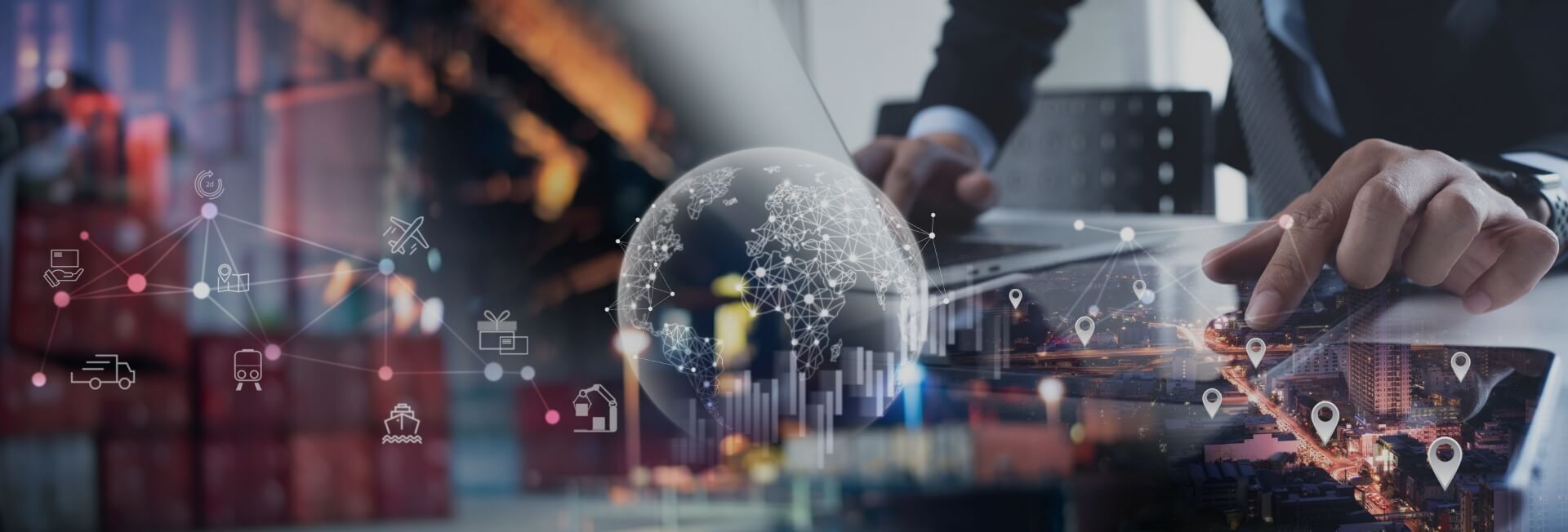
The challenges of managing product recalls in logistics operations
- Home
- Resources
- Transportation Operations
- The challenges of managing product recalls in logistics operations
The Challenges of Managing Product Recalls in Logistics Operations
In today's global marketplace, product recalls have become a common occurrence. Whether it's due to safety concerns, quality issues, or regulatory compliance, companies must be prepared to handle the challenges that come with managing product recalls in their logistics operations. From communication and coordination to inventory management and transportation, there are many moving parts involved in the process. This article will explore the challenges faced in managing product recalls and how transportation management system (TMS) software can help streamline the process.
Communication and Coordination
One of the biggest challenges in managing a product recall is communication and coordination. When a recall is initiated, it is crucial to quickly and efficiently notify all relevant parties, including suppliers, distributors, retailers, and customers. This requires clear and effective communication channels and the ability to track and monitor the progress of the recall. Without proper communication and coordination, delays and errors can occur, leading to increased costs and potential harm to consumers.
Inventory Management
Another challenge in managing a product recall is inventory management. When a recall is initiated, it is important to have an accurate and up-to-date inventory record to identify the affected products and remove them from circulation. This can be a daunting task, especially for companies with large and complex supply chains. Manual inventory management processes can be time-consuming and prone to errors. TMS software can help automate and streamline the inventory management process, making it easier to track and manage recalled products.
Transportation and Logistics
The transportation and logistics aspect of a product recall is often one of the most complex and challenging. Once the recalled products have been identified and removed from inventory, they need to be transported back to the manufacturer or a designated location for proper disposal or remediation. This requires careful planning and coordination to ensure that the products are transported safely and efficiently. TMS software can help optimize transportation routes, schedule pickups and deliveries, and track the progress of the shipments, making the logistics of a product recall more streamlined and efficient.
TMS Software: Streamlining the Product Recall Process
With the challenges involved in managing a product recall, it is essential for companies to leverage technology solutions to streamline the process. Transportation management system (TMS) software offers a range of features and capabilities that can help companies effectively manage product recalls and minimize the impact on their operations.
One of the key benefits of TMS software is its ability to automate and streamline communication and coordination. With TMS software, companies can set up automated alerts and notifications to quickly and efficiently notify all relevant parties about a product recall. This ensures that everyone is on the same page and can take immediate action to address the issue.
TMS software also offers advanced inventory management capabilities. With real-time visibility into inventory levels and locations, companies can easily identify and track recalled products throughout the supply chain. This helps ensure that the affected products are promptly removed from circulation and prevents them from reaching customers.
When it comes to transportation and logistics, TMS software can help optimize routes, consolidate shipments, and track the progress of the shipments in real-time. This not only improves efficiency and reduces costs but also ensures that the recalled products are transported safely and in compliance with regulatory requirements.
Furthermore, TMS software can integrate with other systems and technologies, such as carrier TMS and supply chain optimization solutions, to further streamline the product recall process. By automating and optimizing various aspects of the recall process, companies can minimize disruptions to their operations and mitigate potential risks.
In conclusion, managing product recalls in logistics operations is a complex and challenging task. From communication and coordination to inventory management and transportation, there are many moving parts involved in the process. However, with the right technology solutions, such as transportation management system (TMS) software, companies can streamline the product recall process and minimize the impact on their operations. TMS software offers a range of features and capabilities that help automate and optimize communication, inventory management, and transportation, making the product recall process more efficient and effective.