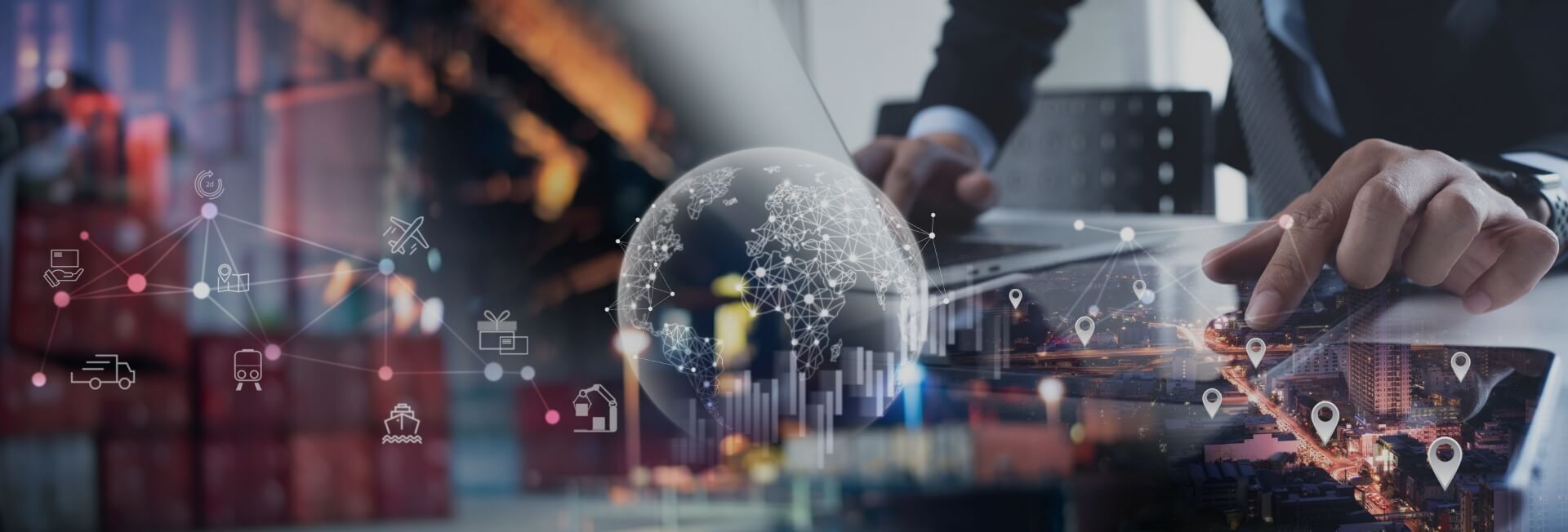
The challenges of implementing TMS software in highly regulated industries
- Home
- Resources
- Transportation Operations
- The challenges of implementing TMS software in highly regulated industries
The Challenges of Implementing TMS Software in Highly Regulated Industries
Logistics management is a complex and vital aspect of any organization involved in the transportation of goods. In highly regulated industries, such as pharmaceuticals, food and beverage, and healthcare, the need for efficient and compliant logistics processes is even more critical. Companies operating in these industries face unique challenges when it comes to implementing Transportation Management System (TMS) software.
Logistics Automation for Supply Chain Optimization
TMS software is designed to streamline logistics operations, optimize transportation routes, and improve overall supply chain efficiency. By automating manual processes and providing real-time visibility into transportation activities, TMS solutions enable companies to make data-driven decisions and enhance customer service.
However, implementing TMS software in highly regulated industries comes with its own set of challenges. These challenges can include compliance with industry-specific regulations, integration with existing systems, and managing carrier relationships. Let's explore each of these challenges in detail.
Compliance with Industry-Specific Regulations
Highly regulated industries are subject to various laws and regulations to ensure the safety, quality, and integrity of their products. This includes regulations related to temperature control, product tracking, and documentation. When implementing TMS software, companies must ensure that the system complies with these regulations and supports the necessary functionalities.
For example, pharmaceutical companies need to comply with Good Distribution Practice (GDP) guidelines, which require strict temperature control during transportation. TMS software should have the capability to monitor and maintain the required temperature throughout the transportation process, and provide documentation to prove compliance.
Similarly, companies in the food and beverage industry need to comply with food safety regulations, such as the Hazard Analysis and Critical Control Points (HACCP) system. TMS software should be able to track and trace products, record critical control points, and generate reports to demonstrate compliance.
Integration with Existing Systems
Many companies in highly regulated industries already have existing systems in place to manage their logistics operations. These systems may include warehouse management systems (WMS), enterprise resource planning (ERP) systems, and electronic data interchange (EDI) systems. When implementing TMS software, integration with these existing systems becomes crucial for seamless data exchange and process automation.
TMS integration allows companies to leverage the data and functionalities of their existing systems while adding the benefits of transportation optimization. For example, integrating TMS with a WMS enables companies to automatically generate shipping orders based on inventory levels and customer orders. This helps in ensuring accurate and timely deliveries while minimizing inventory holding costs.
Furthermore, integration with ERP systems allows for better visibility into the entire supply chain, from procurement to delivery. This enables companies to optimize transportation routes, consolidate shipments, and reduce transportation costs.
Managing Carrier Relationships
In highly regulated industries, maintaining strong relationships with carriers is crucial for ensuring compliance, timely deliveries, and overall supply chain efficiency. However, managing carrier relationships can be challenging, especially when implementing TMS software.
Carrier TMS (CTMS) solutions can help companies streamline carrier management by providing real-time visibility into carrier performance, automating carrier selection and tendering processes, and facilitating communication between shippers and carriers. CTMS also enables companies to track carrier compliance with industry-specific regulations, such as maintaining temperature logs for pharmaceutical shipments or providing documentation for food safety audits.
Implementing CTMS requires effective communication and collaboration with carriers, as well as clear expectations and performance metrics. Companies need to establish strong partnerships with carriers and align their goals and objectives to ensure successful implementation and ongoing collaboration.
Overcoming the Challenges
While implementing TMS software in highly regulated industries may pose challenges, these challenges can be overcome with proper planning, collaboration, and the right technology partner. Here are some strategies to overcome the challenges:
1. Choose a TMS Solution with Industry-Specific Functionality
When selecting a TMS solution, it is important to choose a system that offers industry-specific functionality and complies with the relevant regulations. Look for features such as temperature monitoring, product tracking, and documentation generation to ensure compliance with industry-specific regulations.
Additionally, consider the scalability and flexibility of the TMS solution to accommodate future regulatory changes and evolving business needs.
2. Prioritize Integration with Existing Systems
Prioritize TMS solutions that offer seamless integration with existing systems, such as WMS, ERP, and EDI. This will allow for efficient data exchange, process automation, and improved visibility into the entire supply chain.
Work closely with the TMS provider and existing system vendors to ensure smooth integration and minimize disruptions during the implementation process.
3. Invest in Training and Change Management
Implementing TMS software involves changes in processes, roles, and responsibilities. To ensure successful adoption and minimize resistance to change, invest in comprehensive training programs for employees and carriers.
Communication and change management strategies should be developed to address any concerns or resistance to the new system. Engage employees and carriers throughout the implementation process to foster a sense of ownership and collaboration.
4. Establish Strong Carrier Relationships
Carrier relationship management is key to successful implementation and ongoing collaboration. Establish clear expectations and performance metrics with carriers, and regularly communicate and review performance.
Provide carriers with the necessary tools and resources to comply with industry-specific regulations and ensure timely and accurate deliveries. Foster a culture of collaboration and continuous improvement to drive mutual success.
Conclusion
Implementing TMS software in highly regulated industries can be challenging, but the benefits of logistics automation and supply chain optimization make it worth the effort. By addressing the challenges of compliance, integration, and carrier relationship management, companies can streamline their logistics operations, improve compliance with industry-specific regulations, and enhance overall supply chain efficiency.
Choosing the right TMS solution, prioritizing integration with existing systems, investing in training and change management, and establishing strong carrier relationships are key strategies for overcoming these challenges. With the right approach and the support of a trusted technology partner, companies can successfully implement TMS software and unlock the benefits of transportation efficiency and cost savings.