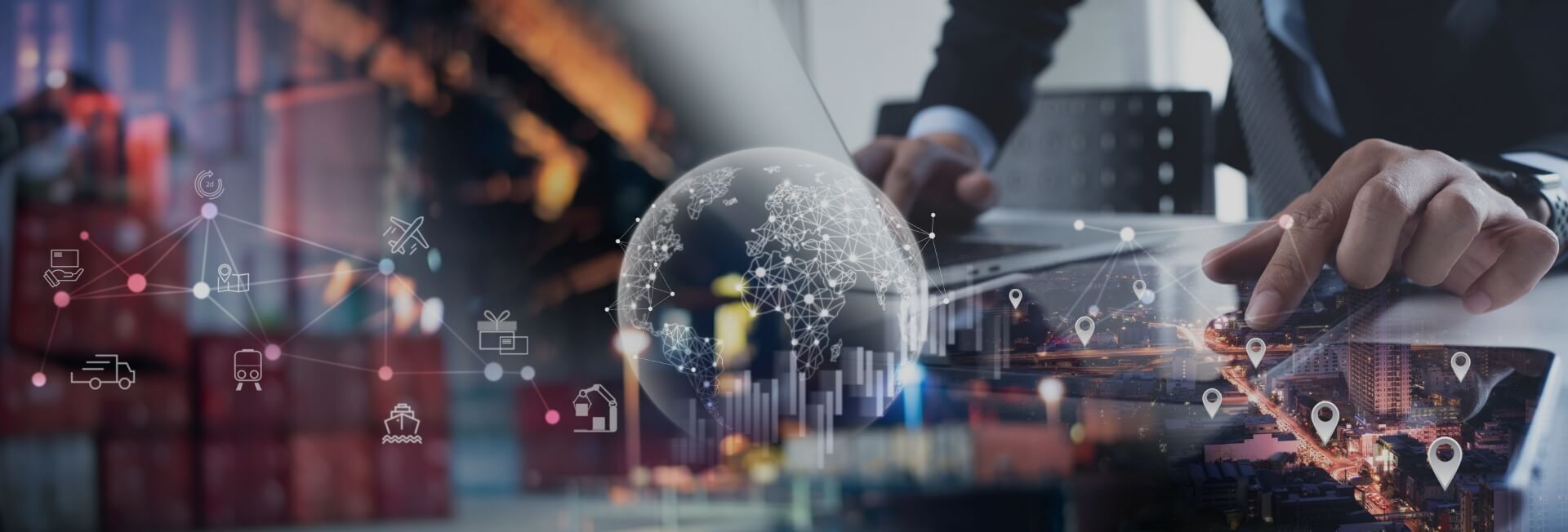
The benefits and challenges of implementing just-in-time (JIT) manufacturing in automated supply chains
- Home
- Resources
- Transportation Operations
- The benefits and challenges of implementing just-in-time (JIT) manufacturing in automated supply chains
The Benefits and Challenges of Implementing Just-in-Time (JIT) Manufacturing in Automated Supply Chains
In today's fast-paced business environment, companies are constantly looking for ways to optimize their supply chains and improve operational efficiency. One approach that has gained popularity in recent years is just-in-time (JIT) manufacturing. JIT manufacturing is a strategy that aims to minimize inventory levels by producing and delivering goods just in time to meet customer demand. When combined with automated supply chains, JIT manufacturing can offer numerous benefits, but it also comes with its own set of challenges. In this article, we will explore the advantages and difficulties of implementing JIT manufacturing in automated supply chains.
Advantages of JIT Manufacturing in Automated Supply Chains
1. Reduced Costs: One of the primary benefits of implementing JIT manufacturing in automated supply chains is the potential for cost savings. By reducing inventory levels and eliminating the need for large warehouses, companies can significantly reduce carrying costs. Additionally, JIT manufacturing allows for better cost control by minimizing waste and reducing the need for excess production.
2. Improved Efficiency: JIT manufacturing promotes a lean and efficient production process. With automated supply chains, companies can streamline their operations by automating tasks such as order processing, inventory management, and production scheduling. This automation eliminates manual errors and reduces lead times, allowing for faster and more efficient production.
3. Increased Flexibility: JIT manufacturing enables companies to quickly adapt to changes in customer demand. With real-time data provided by automated supply chains, companies can adjust production schedules and inventory levels to meet fluctuating demand patterns. This flexibility allows companies to be more responsive to market dynamics and reduce the risk of obsolete inventory.
4. Enhanced Quality Control: With JIT manufacturing, companies can focus on producing high-quality products. By implementing rigorous quality control measures and closely monitoring production processes, companies can ensure that products meet or exceed customer expectations. Automated supply chains further enhance quality control by providing real-time data on production performance, allowing for prompt identification and resolution of any issues.
Challenges of JIT Manufacturing in Automated Supply Chains
1. Dependency on Suppliers: JIT manufacturing relies heavily on suppliers to deliver materials and components on time. Any delay or disruption in the supply chain can have a significant impact on production schedules and customer satisfaction. It is crucial for companies to have strong relationships with reliable suppliers and implement effective supplier management strategies to mitigate this risk.
2. Increased Vulnerability to Disruptions: While JIT manufacturing aims to minimize inventory levels, it also leaves companies more vulnerable to disruptions in the supply chain. Any unexpected event, such as natural disasters or transportation disruptions, can disrupt the flow of materials and components, leading to production delays. To mitigate this risk, companies must have contingency plans in place and maintain close communication with suppliers and transportation providers.
3. Complex Demand Forecasting: JIT manufacturing requires accurate demand forecasting to ensure that production schedules align with customer demand. However, demand forecasting can be challenging, especially in industries with volatile demand patterns. Companies must invest in advanced forecasting tools and analytics capabilities to improve accuracy and minimize the risk of overproduction or stockouts.
4. High Initial Investment: Implementing JIT manufacturing in automated supply chains often requires a significant initial investment. Companies need to invest in advanced technologies such as transportation management system (TMS) software, automation equipment, and real-time data analytics. While these investments can yield long-term cost savings, they may pose financial challenges for some companies.
Logistics Management and TMS Software for JIT Manufacturing
To successfully implement JIT manufacturing in automated supply chains, companies need effective logistics management and transportation management system (TMS) software. Logistics management involves the planning, execution, and control of the flow of goods and information between the point of origin and the point of consumption. TMS software, on the other hand, helps companies optimize their transportation operations by automating processes such as carrier selection, load planning, and route optimization.
By integrating TMS software into their supply chain operations, companies can achieve the following benefits:
1. Supply Chain Optimization: TMS software enables companies to optimize their supply chain by reducing transportation costs, improving delivery performance, and enhancing visibility. With real-time data and analytics capabilities, companies can make informed decisions about carrier selection, route planning, and load consolidation, leading to improved efficiency and cost savings.
2. Streamlined Logistics: TMS software automates manual processes and provides real-time visibility into transportation operations. This streamlines logistics operations and reduces the risk of errors, delays, and miscommunication. With automated workflows and centralized data, companies can ensure that goods are delivered on time and in the most cost-effective manner.
3. Carrier Relationship Management: TMS software facilitates better carrier relationship management by providing tools for tracking carrier performance, managing contracts, and resolving disputes. By monitoring carrier performance and holding carriers accountable for their service levels, companies can improve collaboration, optimize carrier selection, and negotiate better rates.
4. TMS Integration: TMS software can be seamlessly integrated with other supply chain management systems, such as warehouse management systems (WMS) and enterprise resource planning (ERP) systems. This integration allows for better data sharing and coordination between different functions, leading to improved visibility, efficiency, and decision-making.
Conclusion
Implementing just-in-time (JIT) manufacturing in automated supply chains offers numerous benefits, including reduced costs, improved efficiency, increased flexibility, and enhanced quality control. However, it also comes with its own set of challenges, such as dependency on suppliers, increased vulnerability to disruptions, complex demand forecasting, and high initial investment. To overcome these challenges and fully leverage the benefits of JIT manufacturing, companies need to invest in logistics management and transportation management system (TMS) software. By optimizing their supply chain operations and automating transportation processes, companies can achieve greater efficiency, cost savings, and customer satisfaction.