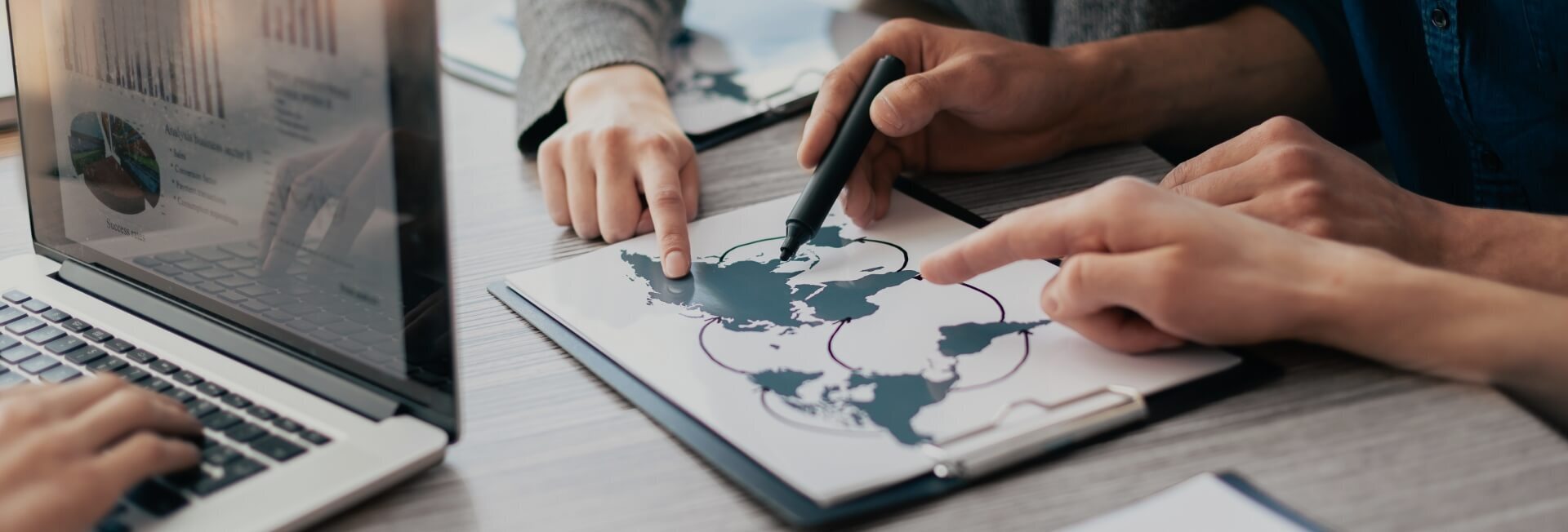
The role of predictive maintenance in reducing downtime and improving logistics equipment reliability
- Home
- Resources
- Freight Logistics and Planning
- The role of predictive maintenance in reducing downtime and improving logistics equipment reliability
The Importance of Predictive Maintenance in Logistics Equipment Reliability
In the fast-paced world of logistics, minimizing downtime and ensuring the reliability of equipment is crucial for smooth operations. Any disruption in logistics equipment can lead to delays in shipments, increased costs, and dissatisfied customers. This is where predictive maintenance comes into play, offering a proactive approach to identify and address potential issues before they cause equipment failure.
What is Predictive Maintenance?
Predictive maintenance is an advanced maintenance strategy that utilizes data analysis and machine learning algorithms to predict equipment failures. By monitoring various parameters and collecting real-time data, predictive maintenance can identify patterns and anomalies that indicate potential issues.
This approach differs from traditional maintenance methods, such as preventive maintenance, which rely on fixed schedules or predetermined thresholds to perform maintenance tasks. With predictive maintenance, logistics companies can move away from reactive approaches and adopt a proactive maintenance strategy that minimizes downtime and maximizes equipment reliability.
The Benefits of Predictive Maintenance in Logistics
Implementing predictive maintenance in logistics offers numerous benefits that directly impact the efficiency and profitability of the business. Here are some key advantages:
1. Reduced Downtime
By using predictive maintenance, logistics companies can detect and address potential equipment failures before they occur. This proactive approach minimizes unexpected breakdowns and reduces downtime, ensuring uninterrupted operations and timely deliveries. With reduced downtime, logistics companies can optimize their resources and improve overall productivity.
2. Cost Savings
Predictive maintenance not only reduces downtime but also helps in optimizing maintenance activities. By identifying specific issues and addressing them promptly, logistics companies can avoid costly repairs and replacements. Additionally, predictive maintenance allows for better planning of maintenance tasks, ensuring that resources are utilized efficiently and unnecessary costs are minimized. Overall, this approach leads to significant cost savings in the long run.
3. Improved Equipment Reliability
Regular maintenance based on predictive analysis ensures that logistics equipment operates at its optimal level. By identifying and addressing potential issues, logistics companies can prevent equipment failures and extend the lifespan of their assets. This leads to improved equipment reliability, reducing the chances of unexpected breakdowns and enhancing overall operational efficiency.
4. Enhanced Safety
Predictive maintenance helps in identifying potential safety hazards and taking proactive measures to mitigate them. By continuously monitoring equipment performance and analyzing data, logistics companies can ensure that their equipment meets safety standards and regulations. This not only protects the workforce but also reduces the risk of accidents and associated liabilities.
Implementing Predictive Maintenance in Logistics
Implementing predictive maintenance in logistics requires a well-designed strategy and the right technological infrastructure. Here are some key steps to consider:
1. Data Collection and Analysis
The first step in implementing predictive maintenance is to collect relevant data from the logistics equipment. This includes parameters such as temperature, vibration, pressure, and performance indicators. This data is then analyzed using machine learning algorithms to identify patterns and anomalies that indicate potential issues.
2. Setting Thresholds and Alerts
Based on the data analysis, logistics companies can set thresholds and alerts to trigger maintenance activities. These thresholds are determined by analyzing historical data and identifying the optimal maintenance points. When the equipment's parameters exceed these thresholds or when anomalies are detected, alerts are generated, and maintenance teams are notified.
3. Integration with Maintenance Management Systems
Predictive maintenance systems can be integrated with existing maintenance management systems to streamline the maintenance workflow. This integration allows for seamless communication between the predictive maintenance system, maintenance teams, and other stakeholders. It enables efficient scheduling of maintenance tasks, allocation of resources, and tracking of maintenance activities.
4. Continuous Improvement and Optimization
Predictive maintenance is an ongoing process that requires continuous improvement and optimization. As more data is collected and analyzed, logistics companies can refine their predictive models and further optimize their maintenance strategies. This iterative approach ensures that the predictive maintenance system becomes more accurate and effective over time.
Conclusion
Predictive maintenance plays a crucial role in reducing downtime and improving the reliability of logistics equipment. By adopting this innovative approach, logistics companies can move away from reactive maintenance methods and proactively address potential issues. With reduced downtime, cost savings, improved equipment reliability, and enhanced safety, predictive maintenance offers significant advantages for logistics operations. By implementing the necessary infrastructure and continuously optimizing their maintenance strategies, logistics companies can harness the power of predictive maintenance to achieve greater efficiency and profitability.
Related Blogs
The impact of real-time temperature monitoring on ensuring product quality in freight transportation
Read More