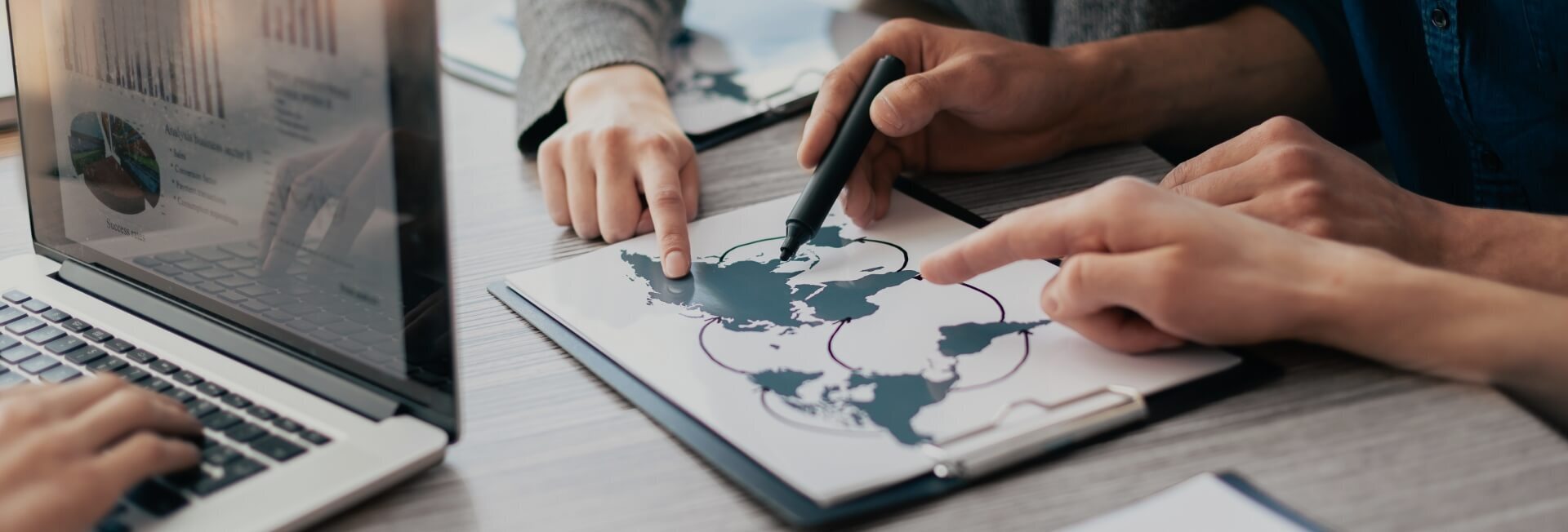
The role of predictive maintenance in minimizing downtime and improving efficiency in freight management
- Home
- Resources
- Freight Logistics and Planning
- The role of predictive maintenance in minimizing downtime and improving efficiency in freight management
The Role of Predictive Maintenance in Minimizing Downtime and Improving Efficiency in Freight Management
Freight management is a complex and dynamic process that requires careful planning, coordination, and execution. With the increasing demands of the global supply chain, companies are constantly looking for innovative solutions to optimize their freight logistics and reduce costs. One such solution that has gained significant traction in recent years is predictive maintenance.
What is Predictive Maintenance?
Predictive maintenance is a proactive approach to maintenance that uses real-time data and advanced analytics to predict equipment failures before they occur. By analyzing historical data, monitoring equipment conditions, and leveraging machine learning algorithms, predictive maintenance can identify potential issues and schedule maintenance activities accordingly. This helps minimize downtime, improve operational efficiency, and reduce overall maintenance costs.
The Benefits of Predictive Maintenance in Freight Management
Predictive maintenance offers several benefits for freight management, including:
1. Minimizing Downtime
Downtime can have a significant impact on freight operations, leading to delays, missed deadlines, and increased costs. By implementing predictive maintenance, companies can identify and address potential equipment failures before they occur, minimizing unplanned downtime and ensuring smooth operations.
2. Improving Efficiency
Predictive maintenance allows for more accurate planning and scheduling of maintenance activities. By identifying the optimal time for maintenance, companies can avoid unnecessary disruptions to their operations and maximize equipment uptime. This leads to improved efficiency and productivity in freight management.
3. Reducing Maintenance Costs
Traditional maintenance practices often rely on scheduled maintenance or reactive repairs, which can be costly and inefficient. Predictive maintenance, on the other hand, focuses on proactive maintenance based on data-driven insights. By addressing potential issues before they become major problems, companies can reduce maintenance costs and extend the lifespan of their equipment.
4. Enhancing Safety
Predictive maintenance helps ensure the safety of both freight operators and the cargo they transport. By identifying and addressing potential equipment failures in advance, companies can prevent accidents, reduce the risk of injuries, and protect their assets.
Implementing Predictive Maintenance in Freight Management
To implement predictive maintenance in freight management, companies need to establish a comprehensive system that combines advanced technologies, data analytics, and industry expertise. Here are some key steps to consider:
1. Data Collection and Analysis
The first step in implementing predictive maintenance is to collect and analyze relevant data. This includes historical maintenance records, equipment sensor data, and other relevant information. By leveraging advanced analytics tools and machine learning algorithms, companies can identify patterns and anomalies that indicate potential equipment failures.
2. Condition Monitoring
Condition monitoring involves the continuous monitoring of equipment conditions in real-time. This can be done through the use of sensors that collect data on temperature, vibration, pressure, and other parameters. By monitoring equipment conditions, companies can detect any deviations from normal operating conditions and take proactive measures to prevent failures.
3. Predictive Analytics
Predictive analytics plays a crucial role in identifying potential equipment failures and predicting their likelihood. By analyzing historical data and combining it with real-time sensor data, companies can develop predictive models that can accurately forecast equipment performance and anticipate maintenance needs.
4. Maintenance Planning and Scheduling
Based on the insights from predictive analytics, companies can develop maintenance plans and schedules that prioritize critical equipment and address potential issues in a timely manner. This involves coordinating maintenance activities with other operational requirements to minimize disruptions and optimize resource allocation.
Conclusion
Predictive maintenance is revolutionizing the freight management industry by minimizing downtime, improving efficiency, and reducing maintenance costs. By leveraging advanced technologies and data analytics, companies can proactively identify potential equipment failures, schedule maintenance activities accordingly, and ensure smooth operations. As the logistics industry continues to embrace technology-driven solutions, predictive maintenance will play a crucial role in driving innovation and optimizing freight logistics.
Related Blogs
The impact of real-time temperature monitoring on ensuring product quality in freight transportation
Read More