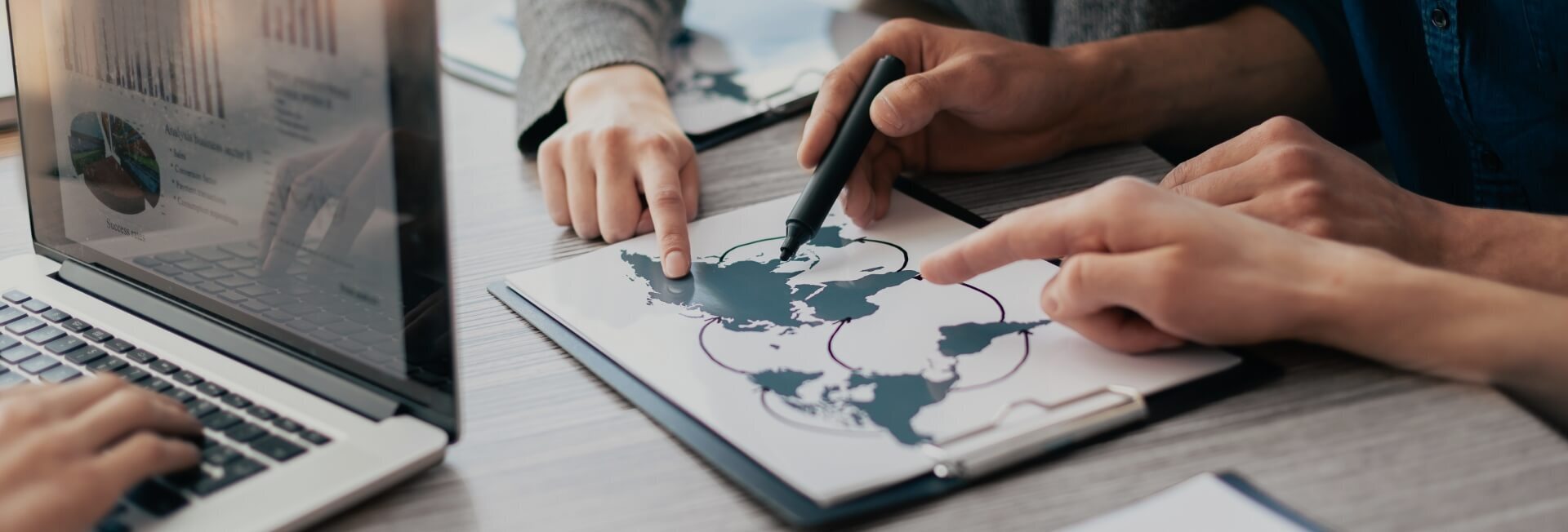
The benefits and challenges of implementing a reverse logistics system for product returns
- Home
- Resources
- Freight Logistics and Planning
- The benefits and challenges of implementing a reverse logistics system for product returns
The Benefits and Challenges of Implementing a Reverse Logistics System for Product Returns
Reverse logistics, the process of managing the return of products from customers to the point of origin, is becoming increasingly important in today's business landscape. As e-commerce continues to grow, so does the volume of product returns. Implementing a reverse logistics system can have significant benefits for businesses, but it also comes with its own set of challenges. In this article, we will explore the advantages and difficulties associated with reverse logistics and how innovative freight solutions and advanced freight systems can optimize the process.
Benefits of Implementing a Reverse Logistics System
1. Improved Customer Satisfaction: A well-executed reverse logistics system can enhance customer satisfaction. By providing a seamless and hassle-free return process, businesses can build trust and loyalty with their customers. This, in turn, can lead to repeat purchases and positive word-of-mouth recommendations.
2. Increased Sales and Revenue: Effective reverse logistics can result in increased sales and revenue. When customers have the option to return products easily, they are more likely to make a purchase in the first place. Additionally, by efficiently managing returns, businesses can identify and recover any salvageable products, reducing loss and generating additional revenue.
3. Enhanced Sustainability: Reverse logistics systems can contribute to a more sustainable business model. By encouraging customers to return unwanted or faulty products, businesses can reduce waste and promote recycling or refurbishing. This not only benefits the environment but also aligns with the growing consumer demand for eco-friendly practices.
4. Valuable Data Insights: The implementation of a reverse logistics system allows businesses to gather valuable data on product returns. By analyzing this data, businesses can identify trends, uncover the root causes of returns, and make informed decisions to improve product quality, packaging, and customer service. This data-driven approach can drive continuous improvement and lead to more satisfied customers.
Challenges of Implementing a Reverse Logistics System
1. Complex Process: Reverse logistics involves multiple stages, including product collection, transportation, sorting, refurbishing, and disposal. Coordinating these activities can be challenging, especially when dealing with a high volume of returns. Implementing a reverse logistics system requires careful planning and efficient execution to ensure smooth operations.
2. Cost Considerations: Reverse logistics can be costly. Businesses need to invest in transportation, storage, refurbishment, and disposal facilities. Additionally, managing returns requires dedicated staff and specialized software solutions. It is essential to carefully analyze the costs and benefits of implementing a reverse logistics system to ensure it is financially viable.
3. Inventory Management: Reverse logistics can complicate inventory management. Returned products need to be accurately recorded, inspected, and either reintroduced into inventory or disposed of properly. Without proper inventory management, businesses may face challenges in meeting customer demands, tracking product status, and optimizing stock levels.
4. Customer Fraud and Abuse: Reverse logistics systems are also vulnerable to customer fraud and abuse. Some customers may take advantage of lenient return policies or engage in activities such as "wardrobing," where they use a product and then return it. Businesses need to implement measures to prevent and detect fraudulent returns, such as strict return policies, product authentication, and customer behavior analysis.
Optimizing Reverse Logistics with Innovative Freight Solutions
To overcome the challenges associated with reverse logistics, businesses can leverage innovative freight solutions and advanced freight systems. These technologies and strategies can streamline the process and maximize efficiency. Here are some key areas where innovative freight solutions can optimize reverse logistics:
1. Freight Tracking and Transportation Software
Implementing freight tracking software can provide real-time visibility into the movement of returned products. This allows businesses to track and manage returns efficiently, ensuring that products are transported to the appropriate location for sorting, refurbishment, or disposal. Transportation software can also optimize routing and reduce transit times, minimizing costs and improving overall logistics operations.
2. Automated Sorting and Refurbishment
Automated sorting systems can streamline the process of categorizing returned products based on their condition and disposition. This saves time and reduces manual labor, enabling faster processing and decision-making. Additionally, advanced refurbishment technologies can restore returned products to their original condition, increasing their value and reducing the need for disposal.
3. Data Analytics and Predictive Modeling
Utilizing freight management software with advanced data analytics capabilities can provide valuable insights into return patterns, product quality issues, and customer behavior. By analyzing this data, businesses can identify areas for improvement, implement preventive measures, and make data-driven decisions to enhance the overall reverse logistics process.
4. Collaboration and Partnerships
Collaborating with third-party logistics providers and establishing partnerships with refurbishment centers, recycling facilities, and charitable organizations can optimize the reverse logistics process. These partnerships can enhance efficiency, reduce costs, and ensure that returned products are handled in an environmentally responsible manner. Working with experienced partners can also provide access to cutting-edge freight technology and expertise.
Conclusion
Implementing a reverse logistics system for product returns can bring numerous benefits to businesses, including improved customer satisfaction, increased sales and revenue, enhanced sustainability, and valuable data insights. However, it is essential to be aware of the challenges associated with reverse logistics, such as the complex process, cost considerations, inventory management, and customer fraud. By leveraging innovative freight solutions and advanced freight systems, businesses can optimize the reverse logistics process and overcome these challenges. Embracing technology-driven logistics and automation can lead to a more efficient and effective reverse logistics system, ultimately benefiting both businesses and customers.
Related Blogs
The impact of real-time temperature monitoring on ensuring product quality in freight transportation
Read More