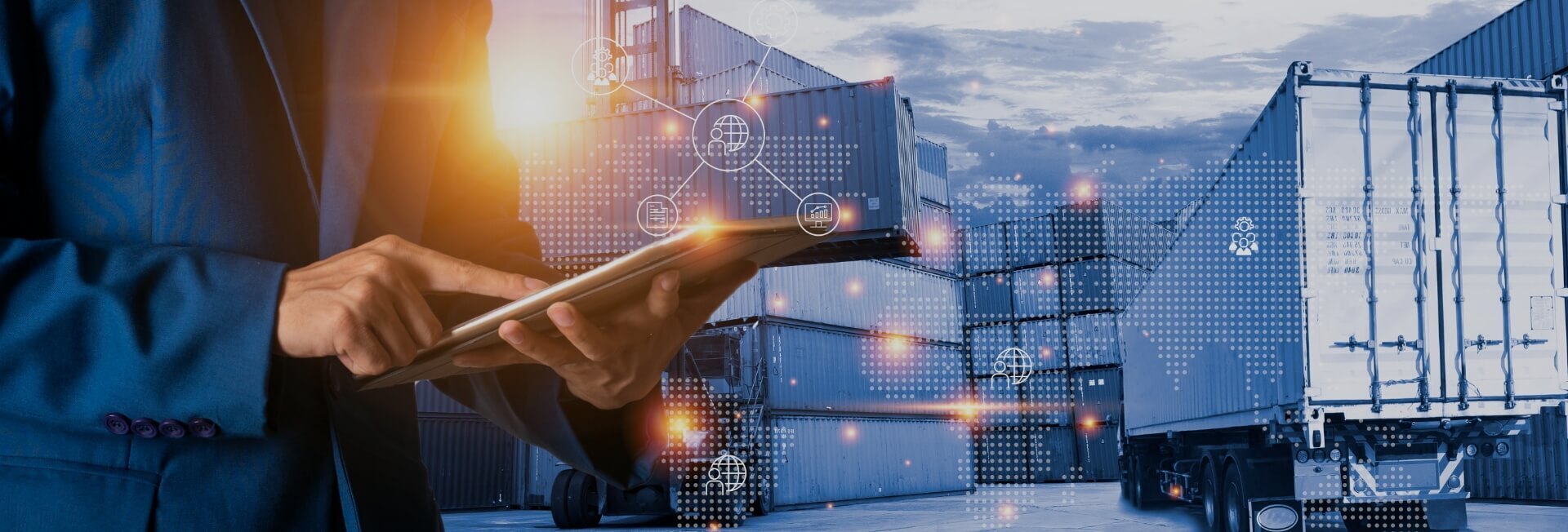
The role of preventive maintenance in reducing equipment failures in the food processing industry
- Home
- Resources
- Fleet Operations and Optimization
- The role of preventive maintenance in reducing equipment failures in the food processing industry
The Importance of Preventive Maintenance in Reducing Equipment Failures in the Food Processing Industry
In the fast-paced and demanding world of the food processing industry, equipment failures can have significant consequences. Not only can they lead to costly downtime and delays in production, but they can also compromise food safety and quality. To mitigate these risks and ensure smooth operations, preventive maintenance plays a crucial role. By implementing a proactive maintenance approach, food processing companies can minimize equipment failures and optimize their operations.
The Benefits of Preventive Maintenance
Preventive maintenance involves regularly inspecting, servicing, and repairing equipment to prevent failures before they occur. This proactive approach offers several benefits to the food processing industry, including:
1. Increased Equipment Reliability: By conducting routine maintenance checks and addressing any issues promptly, the reliability of the equipment is significantly improved. This reduces the likelihood of unexpected breakdowns and ensures uninterrupted production.
2. Extended Equipment Lifespan: Regular maintenance helps extend the lifespan of the equipment. By identifying and addressing minor issues early on, companies can prevent them from escalating into major problems that could lead to premature equipment failure.
3. Enhanced Food Safety: Preventive maintenance involves inspecting the equipment for any potential contamination risks, ensuring that it meets hygiene standards, and replacing worn-out parts. This helps maintain a high level of food safety and prevents product recalls or contamination incidents.
4. Improved Efficiency and Productivity: Well-maintained equipment operates more efficiently, resulting in increased productivity and reduced downtime. By avoiding unexpected breakdowns, companies can optimize their production schedules and meet customer demands more effectively.
Implementing an Effective Preventive Maintenance Program
To reap the benefits of preventive maintenance, food processing companies must develop and implement an effective program. Here are some key steps to consider:
1. Create a Maintenance Schedule: Develop a comprehensive maintenance schedule that outlines the frequency and type of maintenance tasks required for each piece of equipment. This schedule should be based on manufacturer recommendations, industry best practices, and the specific needs of the food processing facility.
2. Use Data-Driven Decision-Making: Collect and analyze data from equipment sensors, maintenance logs, and historical records to identify patterns and trends. This data can provide insights into equipment performance, maintenance needs, and potential failure risks, enabling companies to make informed decisions.
3. Conduct Regular Inspections: Schedule regular inspections to assess the condition of equipment and identify any signs of wear or potential issues. These inspections should include checking for leaks, loose connections, abnormal noises, and any other indicators of equipment malfunction.
4. Train and Empower Maintenance Staff: Provide comprehensive training to maintenance staff on equipment maintenance techniques, safety protocols, and troubleshooting procedures. Empower them to report any issues promptly and encourage a culture of proactive maintenance.
The Role of Technology in Preventive Maintenance
Technology plays a vital role in optimizing preventive maintenance efforts in the food processing industry. Here are some ways technology can enhance maintenance practices:
1. Fleet Tracking and Supply Chain Visibility: Implementing fleet tracking systems allows companies to monitor the movement of vehicles and equipment in real-time. This enables better supply chain visibility, streamlines logistics, and facilitates maintenance scheduling.
2. Data-Driven Insights: Leveraging data analytics and machine learning algorithms can provide actionable insights into equipment performance, maintenance needs, and potential failure risks. This allows for more efficient maintenance scheduling and resource allocation.
3. Maintenance Automation: Automation technologies, such as computerized maintenance management systems (CMMS), can streamline maintenance processes by automating tasks such as work order generation, inventory management, and equipment condition monitoring.
4. Predictive Maintenance: Predictive maintenance uses real-time data and predictive analytics to anticipate equipment failures before they occur. By detecting early warning signs, companies can schedule maintenance activities proactively, minimizing downtime and reducing costs.
Conclusion
Preventive maintenance is a critical aspect of ensuring smooth operations in the food processing industry. By implementing a proactive maintenance approach and leveraging technology, companies can reduce equipment failures, improve efficiency, and enhance food safety. Investing in comprehensive preventive maintenance programs and embracing technological advancements is essential for staying competitive and meeting the demands of a rapidly evolving industry.
Related Blogs
The benefits of implementing a preventive maintenance schedule for facility management
Read More