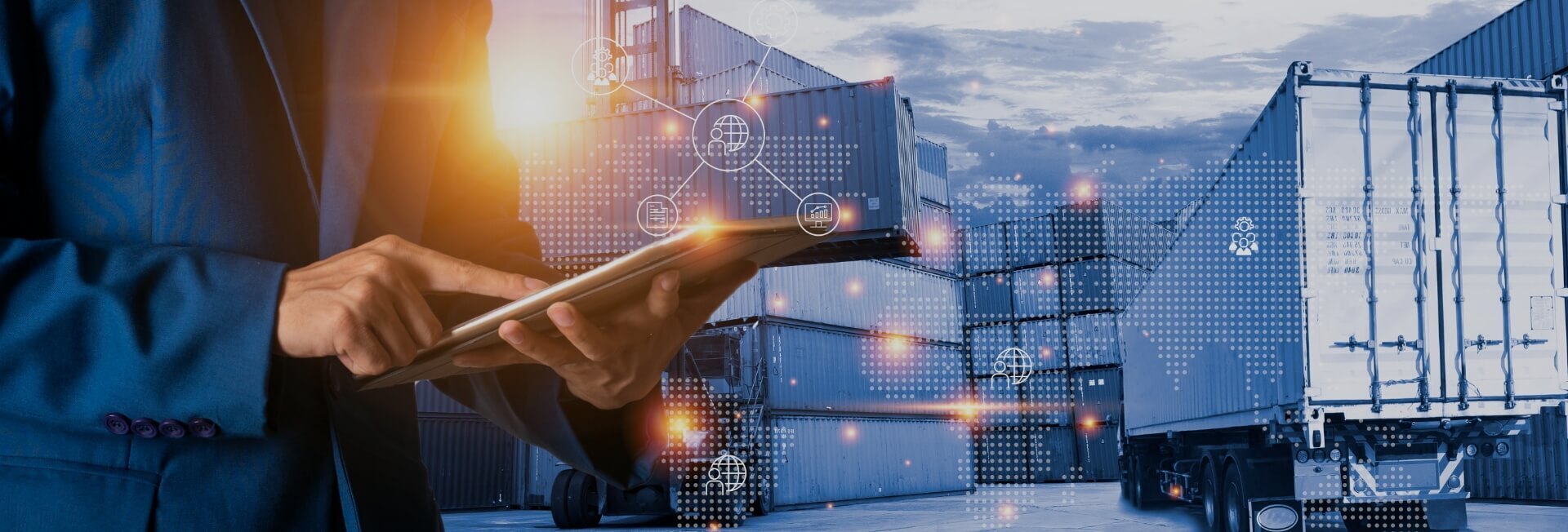
The role of preventive maintenance in reducing equipment failures in the chemical industry
- Home
- Resources
- Fleet Operations and Optimization
- The role of preventive maintenance in reducing equipment failures in the chemical industry
Preventive maintenance plays a crucial role in reducing equipment failures in the chemical industry. By implementing regular maintenance schedules, conducting inspections, and addressing potential issues before they become major problems, companies can significantly improve the reliability and lifespan of their equipment. In this article, we will explore the importance of preventive maintenance in the chemical industry and discuss how it can help streamline logistics, optimize supply chains, and ensure efficient operations.
Preventive Maintenance for Fleet Optimization
Fleet maintenance is a critical aspect of the chemical industry, as companies rely heavily on transportation to move raw materials and finished products. By implementing preventive maintenance practices, such as regular inspections and proactive repairs, companies can ensure that their fleet remains in optimal condition, reducing the risk of breakdowns and delays.
One key aspect of fleet maintenance is fleet tracking, which provides real-time fleet data and enables companies to make data-driven decisions. With comprehensive fleet management solutions, companies can track their vehicles' performance, monitor fuel consumption, and identify potential maintenance issues before they lead to equipment failures. This visibility allows for efficient maintenance scheduling, ensuring that vehicles are serviced at the appropriate intervals without disrupting operations.
Streamlining Logistics with Preventive Maintenance
Efficient logistics is crucial in the chemical industry, as timely deliveries and optimal supply chain management are essential for meeting customer demands. Preventive maintenance plays a vital role in streamlining logistics by minimizing the risk of equipment failures and unexpected breakdowns.
By implementing preventive maintenance practices, companies can reduce the need for unscheduled vehicle repairs, which can result in costly delays and disruptions. Regular inspections and maintenance help identify potential issues early on, allowing for timely repairs and minimizing the risk of breakdowns during transportation. This proactive approach enables companies to maintain a reliable fleet, ensuring that deliveries are made on time and without interruptions.
Optimizing Supply Chain Visibility
Supply chain visibility is crucial for efficient operations in the chemical industry. By implementing preventive maintenance practices and utilizing fleet tracking technologies, companies can gain real-time insights into their supply chain and make data-driven decisions.
With comprehensive fleet management solutions, companies can monitor the performance of their vehicles, track their location, and optimize routes to minimize fuel consumption and reduce transportation costs. This level of visibility allows for efficient supply chain management, enabling companies to make informed decisions and optimize their operations for maximum efficiency and productivity.
Actionable Insights for Efficient Operations
Preventive maintenance not only helps reduce equipment failures but also provides actionable insights that can further improve operational efficiency. By analyzing maintenance data and identifying trends, companies can identify areas for improvement and implement preventive measures to address potential issues.
For example, if a certain type of equipment consistently requires frequent repairs, companies can explore alternative options or adjust maintenance schedules to minimize downtime and improve overall efficiency. By leveraging data-driven insights, companies can continuously optimize their maintenance processes and ensure that their equipment remains in optimal condition, reducing the risk of failures and maximizing productivity.
In conclusion, preventive maintenance plays a crucial role in reducing equipment failures in the chemical industry. By implementing regular maintenance schedules, conducting inspections, and addressing potential issues proactively, companies can minimize the risk of breakdowns, streamline logistics, optimize supply chain visibility, and improve overall efficiency and productivity. With comprehensive fleet management solutions and data-driven decision-making, companies can ensure that their equipment remains in optimal condition, reducing downtime, and maximizing the lifespan of their assets.
Related Blogs
The benefits of implementing a preventive maintenance schedule for facility management
Read More