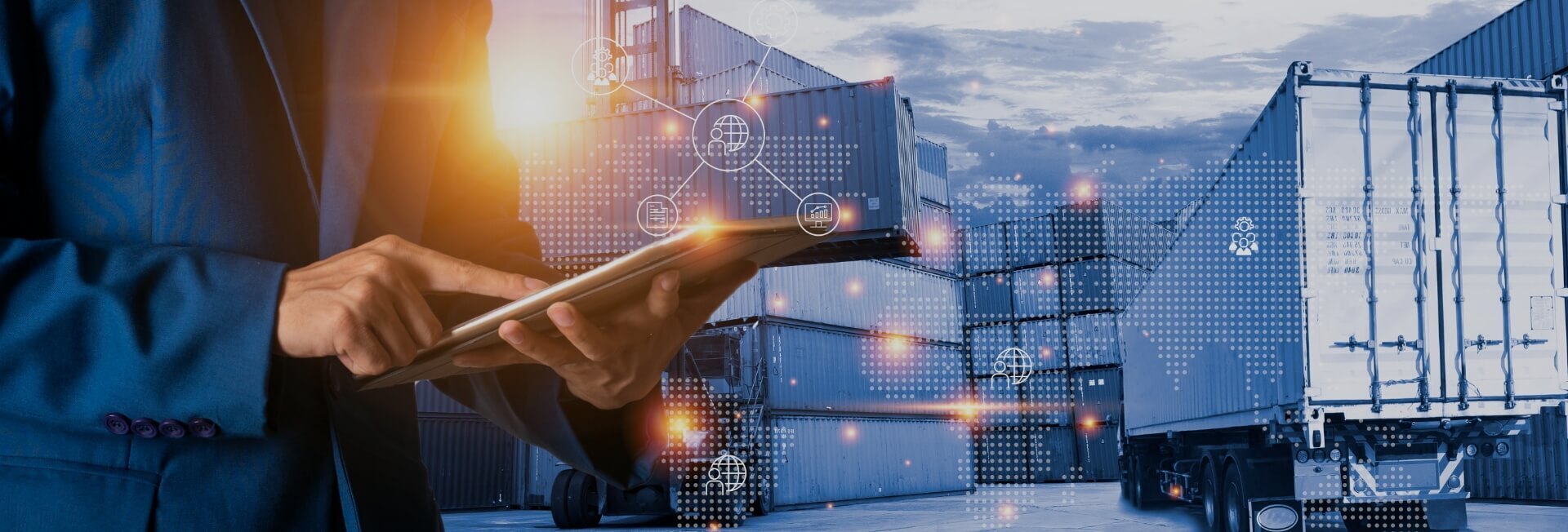
The role of predictive maintenance in reducing fleet downtime
- Home
- Resources
- Fleet Operations and Optimization
- The role of predictive maintenance in reducing fleet downtime
In today's fast-paced business environment, fleet management plays a critical role in ensuring the smooth operation of supply chains. Effective fleet maintenance and management are crucial for organizations to achieve optimal logistics efficiency and minimize downtime. One of the key strategies that can significantly enhance fleet maintenance and reduce downtime is predictive maintenance.
What is Predictive Maintenance?
Predictive maintenance is a proactive approach to maintenance that uses data and analytics to predict when a vehicle or equipment is likely to fail. By monitoring various parameters and performance indicators, predictive maintenance can identify potential issues before they escalate into major problems. This allows fleet managers to schedule maintenance and repairs in a planned and efficient manner, minimizing unplanned downtime.
The Benefits of Predictive Maintenance
Implementing predictive maintenance in fleet management offers several key benefits:
1. Reduced Downtime
Predictive maintenance enables fleet managers to identify potential issues and address them proactively, reducing the risk of unexpected breakdowns or failures. By scheduling maintenance and repairs based on data-driven insights, fleet managers can minimize downtime and keep their vehicles on the road, ensuring timely deliveries and customer satisfaction.
2. Increased Efficiency
Predictive maintenance allows fleet managers to optimize maintenance scheduling based on the actual condition and usage of each vehicle. This ensures that maintenance activities are performed at the right time, maximizing the efficiency of fleet operations. By avoiding unnecessary maintenance or overhauls, fleet managers can save time and resources, leading to cost savings.
3. Cost Savings
By identifying potential issues before they become major problems, predictive maintenance can help fleet managers avoid costly repairs or replacements. The early detection of equipment failures allows for timely repairs, which are often less expensive than emergency repairs or replacements. Additionally, predictive maintenance can help extend the lifespan of vehicles and equipment, reducing the need for frequent replacements and improving the overall cost-effectiveness of fleet operations.
4. Improved Safety
Predictive maintenance not only helps prevent breakdowns and failures but also enhances the safety of drivers and other road users. By ensuring that vehicles are in optimal condition, fleet managers can reduce the risk of accidents caused by mechanical failures. This not only protects lives but also helps organizations avoid potential legal liabilities and reputational damage.
Implementing Predictive Maintenance in Fleet Management
Integrating predictive maintenance into fleet management requires a combination of technology, data analytics, and organizational processes. Here are some key steps to consider:
1. Collecting Real-Time Fleet Data
The foundation of predictive maintenance is the availability of accurate and up-to-date data. Fleet managers need to implement systems and technologies that can collect real-time data on various parameters, such as engine performance, fuel consumption, tire pressure, and vehicle usage. This data can be collected through telematics devices, sensors, and other IoT-enabled technologies.
2. Analyzing and Interpreting Data
Once the data is collected, it needs to be analyzed and interpreted to identify patterns, trends, and anomalies. Advanced analytics tools and algorithms can be used to process large volumes of data and generate actionable insights. These insights can help fleet managers identify potential maintenance issues and make informed decisions regarding maintenance scheduling and resource allocation.
3. Integrating with Maintenance Scheduling
The insights generated through predictive maintenance should be integrated with the existing maintenance scheduling system. This ensures that maintenance activities are planned and scheduled based on the actual condition and performance of each vehicle. By automating the maintenance scheduling process, fleet managers can streamline operations and optimize resource allocation.
4. Training and Skill Development
Implementing predictive maintenance requires a certain level of technical expertise and knowledge. Fleet managers should provide training and skill development opportunities to their maintenance staff to ensure they have the necessary skills to analyze and interpret the data collected. This will enable them to effectively use the predictive maintenance insights to make informed decisions and take appropriate actions.
Conclusion
Predictive maintenance plays a crucial role in reducing fleet downtime and maximizing efficiency. By leveraging real-time fleet data and advanced analytics, fleet managers can proactively identify potential maintenance issues and schedule repairs in a planned and efficient manner. This not only reduces downtime but also increases efficiency, saves costs, and improves safety. The implementation of predictive maintenance requires a comprehensive approach that combines technology, data analytics, and organizational processes. With the right systems and processes in place, organizations can achieve a data-driven and proactive approach to fleet maintenance, leading to streamlined logistics and optimized supply chain operations.
Related Blogs
The benefits of implementing a preventive maintenance schedule for facility management
Read More