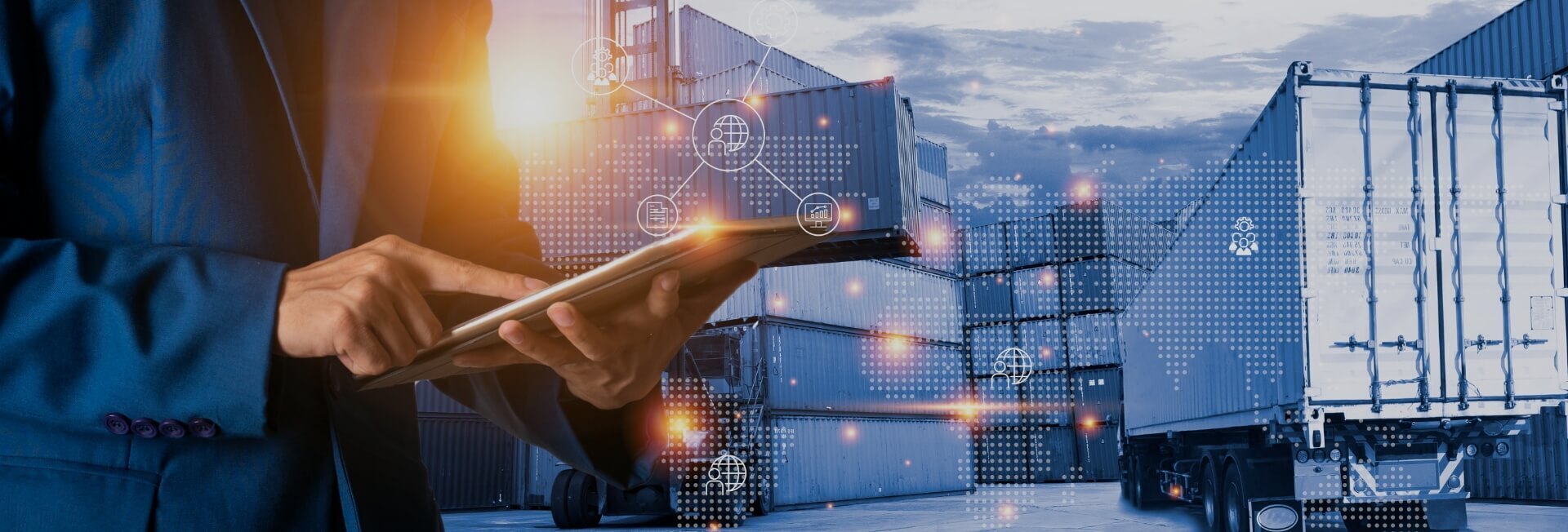
The role of predictive maintenance in reducing downtime and costs
- Home
- Resources
- Fleet Operations and Optimization
- The role of predictive maintenance in reducing downtime and costs
The Power of Predictive Maintenance in Reducing Downtime and Costs
In today's fast-paced business environment, where supply chain optimization and streamlined logistics play a crucial role in maintaining a competitive edge, preventing downtime and minimizing costs are top priorities for fleet managers. Traditional maintenance practices, such as preventive maintenance, have long been used to keep vehicles in good condition and minimize breakdowns. However, with the advent of technology and the availability of real-time fleet data, a new approach called predictive maintenance is revolutionizing the way fleet maintenance is managed.
What is Predictive Maintenance?
Predictive maintenance is a proactive approach to fleet maintenance that leverages data analytics and machine learning algorithms to predict and prevent equipment failures before they occur. By continuously monitoring and analyzing real-time data from vehicles and equipment, fleet managers can identify potential issues and take proactive measures to address them, avoiding costly breakdowns and unplanned downtime.
The Benefits of Predictive Maintenance
Predictive maintenance offers several key benefits for businesses looking to optimize their fleet maintenance and logistics efficiency:
1. Reduced Downtime
One of the most significant advantages of predictive maintenance is its ability to reduce downtime. By detecting potential equipment failures in advance, fleet managers can schedule maintenance and repairs during planned downtime, minimizing the impact on operations. This proactive approach ensures that vehicles and equipment are always in optimal working condition, reducing the risk of unexpected breakdowns and the associated costs.
2. Cost Savings
Predictive maintenance can help businesses save significant costs by preventing equipment failures and minimizing the need for unscheduled repairs. By addressing maintenance issues before they escalate, fleet managers can avoid costly repairs, spare part replacements, and the associated labor costs. Additionally, by optimizing maintenance scheduling, businesses can reduce the number of maintenance visits and the associated downtime, resulting in further cost savings.
3. Improved Fleet Efficiency
Predictive maintenance enables fleet managers to optimize their maintenance schedules based on real-time data and actionable insights. By analyzing historical data, such as vehicle usage patterns, maintenance records, and environmental conditions, fleet managers can identify trends and patterns that can help them make informed decisions about maintenance scheduling. This data-driven approach ensures that maintenance activities are performed when needed, maximizing fleet uptime and efficiency.
4. Enhanced Safety
By proactively addressing maintenance issues before they become critical, predictive maintenance can contribute to improved safety. Regular maintenance and inspections can help identify potential safety hazards, such as worn-out tires or faulty brakes, and take corrective actions to ensure the safety of drivers and other road users. This proactive approach can help businesses maintain compliance with safety regulations and reduce the risk of accidents.
Implementing Predictive Maintenance
Implementing a predictive maintenance program involves several key steps:
1. Data Collection
The first step in implementing predictive maintenance is to collect and analyze relevant data from vehicles and equipment. This includes data such as engine performance, fuel consumption, temperature, vibration, and other sensor readings. Fleet management software and telematics systems can play a crucial role in collecting and aggregating this data, providing fleet managers with real-time insights into the health and performance of their fleet.
2. Data Analysis
Once the data is collected, it needs to be analyzed to identify patterns, trends, and potential issues. Data analytics tools and machine learning algorithms can help fleet managers make sense of the vast amount of data collected and provide actionable insights. These insights can help fleet managers predict equipment failures, identify maintenance needs, and optimize maintenance schedules.
3. Integration with Maintenance Processes
Predictive maintenance should be integrated into the existing maintenance processes and workflows of the business. This includes updating maintenance schedules, coordinating maintenance activities with service providers, and ensuring that the necessary spare parts and resources are available when needed. Effective communication and collaboration between fleet managers, maintenance teams, and service providers are essential for successful implementation.
4. Continuous Improvement
Predictive maintenance is an ongoing process that requires continuous monitoring, analysis, and improvement. Fleet managers should regularly review and analyze the performance of their predictive maintenance program, identify areas for improvement, and make necessary adjustments. This iterative approach helps businesses refine their maintenance strategies and optimize fleet performance over time.
The Future of Predictive Maintenance
As advancements in technology continue to reshape the logistics industry, predictive maintenance is poised to play a significant role in the future of fleet management. The increasing availability of real-time fleet data, coupled with the advancements in data analytics and machine learning, will enable businesses to take a proactive approach to maintenance, reduce downtime, and optimize fleet performance.
Furthermore, the integration of predictive maintenance with other technologies, such as fleet tracking and supply chain visibility solutions, will enable businesses to achieve even greater efficiencies. By combining real-time fleet data with supply chain optimization algorithms, businesses can make data-driven decisions that not only optimize fleet maintenance but also streamline logistics operations and improve overall supply chain efficiency.
In conclusion, predictive maintenance offers significant benefits for businesses looking to reduce downtime, minimize costs, and improve fleet maintenance and logistics efficiency. By leveraging real-time fleet data, analytics, and machine learning algorithms, businesses can take a proactive approach to maintenance, identify potential issues before they occur, and optimize maintenance schedules. As technology continues to advance, predictive maintenance is expected to become an integral part of comprehensive fleet management and logistics automation solutions.
Related Blogs
The benefits of implementing a preventive maintenance schedule for facility management
Read More