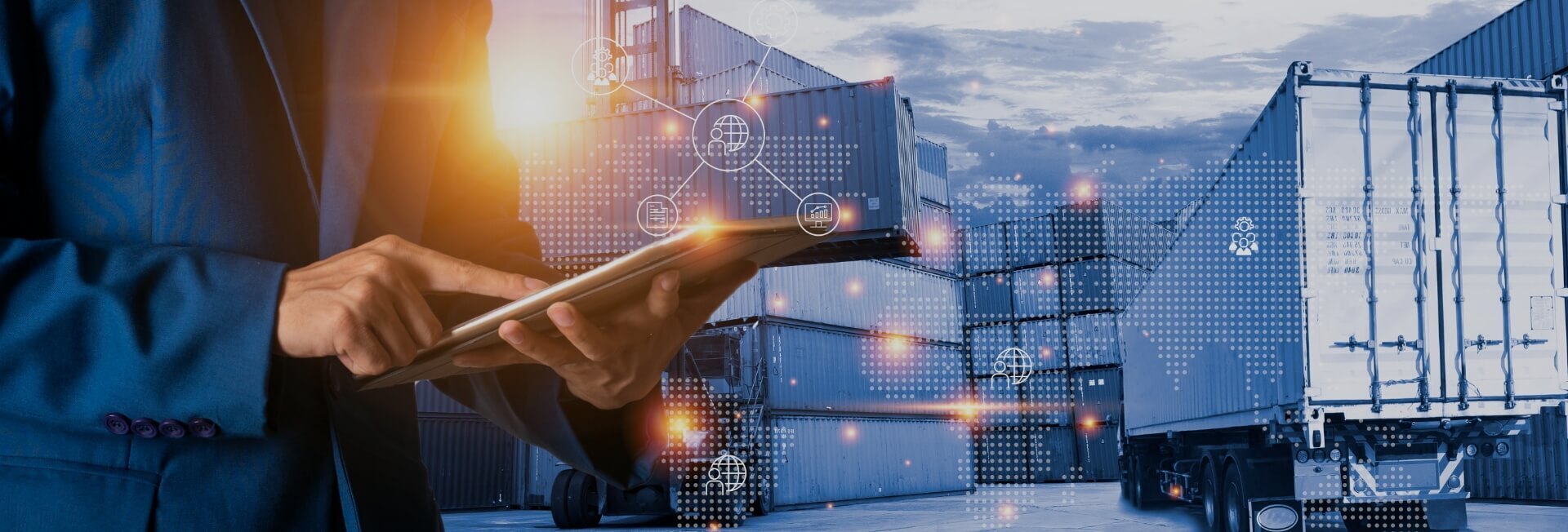
The role of predictive maintenance in preventing downtime for logistics automation systems
- Home
- Resources
- Fleet Operations and Optimization
- The role of predictive maintenance in preventing downtime for logistics automation systems
The Importance of Predictive Maintenance in Preventing Downtime for Logistics Automation Systems
In today's fast-paced world, where efficient logistics and streamlined supply chains are crucial for businesses to stay competitive, logistics automation systems play a vital role. These systems, which include fleet tracking, supply chain visibility, and data-driven fleet management, help optimize operations, improve efficiency, and ensure timely deliveries. However, like any other machinery, logistics automation systems are prone to wear and tear, breakdowns, and unexpected downtime, which can significantly impact the overall efficiency and profitability of a business.
This is where predictive maintenance comes into play. Predictive maintenance is a proactive approach that uses data and analytics to predict when equipment or machinery is likely to fail, allowing for timely repairs or replacements before a breakdown occurs. By implementing predictive maintenance strategies, businesses can prevent downtime, reduce maintenance costs, and maximize the lifespan of their logistics automation systems.
Preventive Maintenance vs. Predictive Maintenance
Before diving into the role of predictive maintenance in preventing downtime for logistics automation systems, it's important to understand the difference between preventive maintenance and predictive maintenance.
Preventive maintenance is a scheduled maintenance approach where equipment or machinery is regularly inspected, repaired, or replaced based on a predetermined schedule. This helps prevent unexpected breakdowns and ensures that equipment operates at optimal levels. However, preventive maintenance can be time-consuming and costly, as it often involves maintenance activities that may not be necessary.
Predictive maintenance, on the other hand, takes a data-driven approach to maintenance scheduling. It uses real-time data and advanced analytics to predict when equipment is likely to fail, allowing businesses to schedule maintenance activities only when necessary. This not only saves time and reduces maintenance costs but also minimizes downtime and increases overall efficiency.
The Role of Predictive Maintenance in Preventing Downtime
Predictive maintenance plays a crucial role in preventing downtime for logistics automation systems. By continuously monitoring the condition of equipment and analyzing real-time data, businesses can identify potential issues before they escalate into major problems. This allows for proactive repairs or replacements, preventing unexpected breakdowns and minimizing downtime.
Here are some key ways in which predictive maintenance helps prevent downtime:
1. Early Detection of Equipment Issues
Predictive maintenance utilizes sensors and monitoring devices to collect data on various parameters such as temperature, vibration, and performance metrics. This data is then analyzed using advanced analytics algorithms to detect any anomalies or deviations from normal operating conditions. By detecting these issues early on, businesses can take immediate action to address them, preventing more significant problems and potential breakdowns.
Fleet maintenance is a critical aspect of logistics automation systems. By implementing predictive maintenance strategies, businesses can identify potential vehicle repairs or maintenance needs before they become major issues. This ensures that the fleet remains in optimal condition, reducing the risk of breakdowns and maximizing uptime.
2. Optimal Maintenance Scheduling
Predictive maintenance allows businesses to optimize maintenance scheduling based on the actual condition of the equipment. Instead of following a fixed maintenance schedule, which may result in unnecessary maintenance activities, businesses can schedule maintenance tasks only when they are needed. This not only saves time and reduces maintenance costs but also minimizes disruptions to operations, as maintenance can be planned during non-peak hours or downtime.
For logistics automation systems, optimal maintenance scheduling is crucial to ensure uninterrupted operations. By leveraging real-time fleet data and predictive analytics, businesses can schedule maintenance activities for individual vehicles or equipment based on their usage patterns, performance data, and predicted failure probabilities. This ensures that maintenance tasks are performed at the most opportune times, minimizing downtime and maximizing fleet efficiency.
3. Improved Equipment Reliability
Predictive maintenance helps improve the reliability of logistics automation systems by addressing potential issues before they lead to breakdowns or failures. By regularly monitoring the condition of equipment and addressing any anomalies or deviations, businesses can ensure that their logistics automation systems operate at optimal levels. This not only reduces the risk of downtime but also enhances the overall efficiency and performance of the systems.
Furthermore, by analyzing the data collected from predictive maintenance activities, businesses can gain actionable insights into the performance and reliability of their logistics automation systems. This data-driven approach allows for continuous improvements and optimization, leading to more reliable and efficient operations.
4. Cost Savings and Increased Efficiency
Predictive maintenance can result in significant cost savings and increased efficiency for businesses. By preventing unexpected breakdowns and minimizing downtime, businesses can avoid the costs associated with emergency repairs, replacement equipment rentals, and missed delivery deadlines. Additionally, by optimizing maintenance scheduling and reducing unnecessary maintenance activities, businesses can save on maintenance costs and allocate resources more effectively.
Furthermore, by maximizing the lifespan of logistics automation systems through proactive maintenance and addressing potential issues early on, businesses can avoid premature equipment replacements and extend the return on investment. This not only reduces capital expenses but also contributes to sustainable and cost-effective operations.
Conclusion
Predictive maintenance plays a critical role in preventing downtime for logistics automation systems. By leveraging real-time data, advanced analytics, and actionable insights, businesses can detect equipment issues early on, schedule maintenance tasks optimally, improve equipment reliability, and achieve cost savings and increased efficiency. By implementing predictive maintenance strategies, businesses can ensure that their logistics automation systems operate at optimal levels, ensuring streamlined logistics, efficient supply chain management, and real-time decision-making.
Related Blogs
The benefits of implementing a preventive maintenance schedule for facility management
Read More