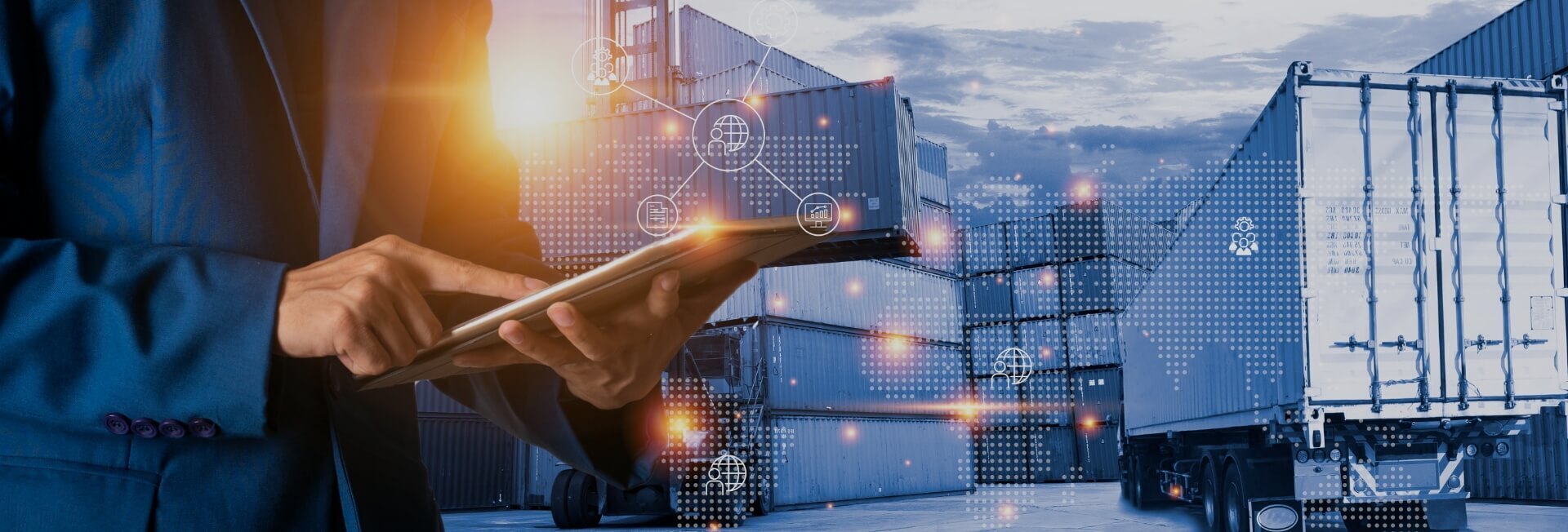
The role of predictive maintenance in minimizing equipment downtime in streamlining logistics.
- Home
- Resources
- Fleet Operations and Optimization
- The role of predictive maintenance in minimizing equipment downtime in streamlining logistics.
The Importance of Predictive Maintenance in Streamlining Logistics
In today's fast-paced business environment, efficient logistics and supply chain management are crucial for the success of any organization. The ability to streamline operations, minimize equipment downtime, and optimize fleet maintenance plays a vital role in ensuring smooth and cost-effective logistics operations. One of the key strategies in achieving these goals is the implementation of predictive maintenance.
What is Predictive Maintenance?
Predictive maintenance is a proactive approach to equipment maintenance that uses data and analytics to predict when and how equipment is likely to fail. By analyzing real-time fleet data, organizations can identify potential issues before they become major problems, allowing for timely repairs and maintenance. This approach helps minimize the risk of unexpected breakdowns, reduce downtime, and increase the overall efficiency of logistics operations.
The Benefits of Predictive Maintenance in Logistics
Implementing predictive maintenance in logistics brings several benefits to organizations. Let's explore some of the key advantages:
1. Minimizing Equipment Downtime
One of the primary advantages of predictive maintenance is its ability to minimize equipment downtime. By continuously monitoring the health and performance of vehicles and equipment, organizations can detect signs of potential failures and take proactive measures to address them. This helps prevent unexpected breakdowns and reduces the time and cost associated with equipment repairs. Additionally, by scheduling maintenance activities based on real-time data, organizations can ensure minimal disruption to logistics operations.
2. Optimizing Fleet Maintenance
Predictive maintenance enables organizations to optimize their fleet maintenance schedules. Instead of relying on fixed maintenance intervals, which can result in unnecessary maintenance and downtime, organizations can use real-time data to determine the optimal time for maintenance activities. This ensures that vehicles and equipment receive maintenance when needed, minimizing costs and maximizing their lifespan. By avoiding over-maintenance and under-maintenance, organizations can achieve significant cost savings and improve fleet efficiency.
3. Enhancing Logistics Efficiency
Predictive maintenance plays a crucial role in enhancing logistics efficiency. By minimizing equipment downtime and optimizing fleet maintenance, organizations can ensure that vehicles and equipment are in optimal condition, reducing the risk of delays and disruptions in supply chain operations. With efficient logistics operations, organizations can meet customer demands more effectively, improve on-time delivery performance, and gain a competitive edge in the market.
4. Data-Driven Decision Making
Another significant advantage of predictive maintenance is its ability to provide actionable insights for data-driven decision making. By analyzing real-time fleet data, organizations can identify patterns, trends, and potential issues, allowing them to make informed decisions regarding maintenance activities, fleet optimization, and resource allocation. This data-driven approach enables organizations to prioritize maintenance tasks, allocate resources efficiently, and make strategic decisions that positively impact logistics operations.
Implementing Predictive Maintenance in Logistics
Implementing predictive maintenance in logistics requires a comprehensive fleet management system that can collect, analyze, and interpret real-time fleet data. Here are some key steps for successful implementation:
1. Fleet Tracking and Monitoring
Implement a fleet tracking and monitoring system that can collect real-time data on vehicle performance, including engine health, fuel consumption, tire pressure, and more. This data will serve as the foundation for predictive maintenance.
2. Data Analysis and Predictive Modeling
Utilize advanced analytics and predictive modeling techniques to analyze the collected real-time data and identify patterns, trends, and potential equipment failures. This analysis will help in developing predictive maintenance models and algorithms.
3. Maintenance Scheduling and Automation
Develop a maintenance scheduling system that utilizes the predictive maintenance models to determine the optimal time for maintenance activities. Automate the scheduling process to ensure timely execution of maintenance tasks.
4. Integration with Supply Chain Visibility and Optimization
Integrate the predictive maintenance system with supply chain visibility and optimization tools to ensure seamless coordination between maintenance activities and overall logistics operations. This integration will enable organizations to make real-time decisions based on accurate and up-to-date information.
Conclusion
Predictive maintenance plays a crucial role in minimizing equipment downtime and streamlining logistics operations. By leveraging real-time fleet data and predictive analytics, organizations can proactively identify and address potential equipment failures, optimize fleet maintenance schedules, enhance logistics efficiency, and make data-driven decisions. Implementing predictive maintenance requires a comprehensive fleet management system and integration with supply chain visibility tools. With the right approach, organizations can achieve significant cost savings, improve operational efficiency, and gain a competitive advantage in the dynamic logistics industry.
Related Blogs
The benefits of implementing a preventive maintenance schedule for facility management
Read More