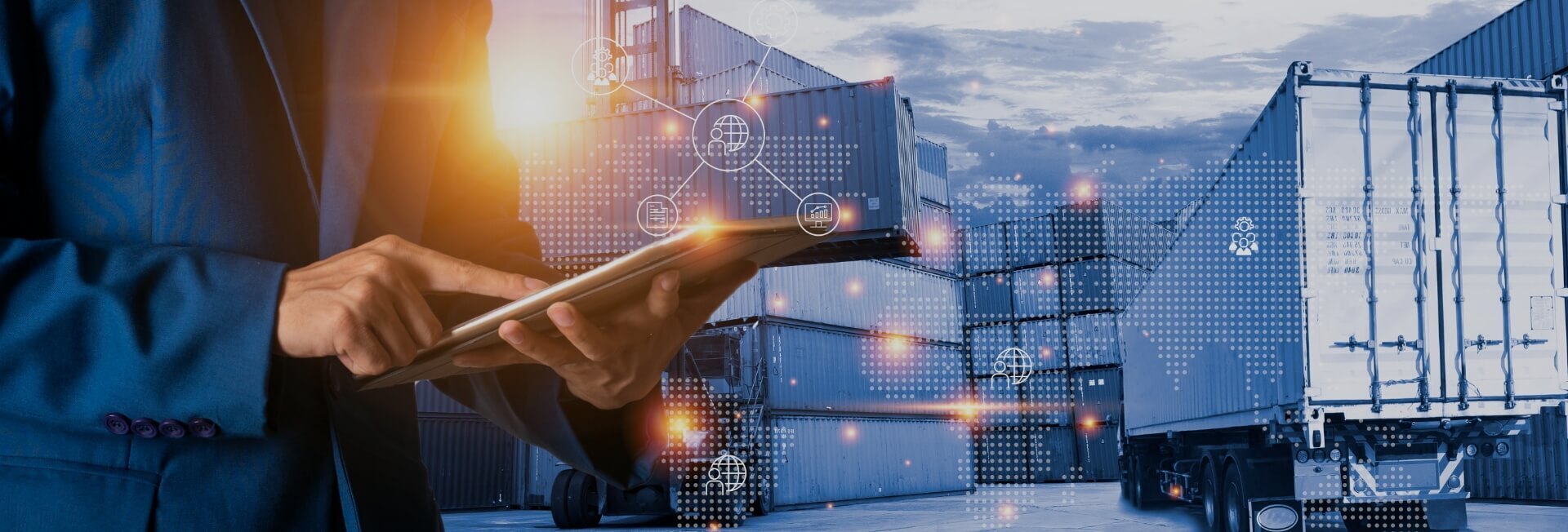
The role of predictive maintenance in ensuring uptime for logistics automation systems
- Home
- Resources
- Fleet Operations and Optimization
- The role of predictive maintenance in ensuring uptime for logistics automation systems
The Importance of Predictive Maintenance in Logistics Automation Systems
In today's fast-paced and highly competitive business landscape, logistics companies are constantly striving to improve efficiency and reduce costs. One key area where companies can achieve significant gains is in the maintenance and management of their fleet. By implementing predictive maintenance strategies, logistics companies can ensure the uptime of their automation systems, optimize fleet performance, and minimize costly downtime.
What is Predictive Maintenance?
Predictive maintenance is a proactive approach to maintenance that leverages data and analytics to predict when equipment is likely to fail. By analyzing real-time data from sensors and other sources, logistics companies can identify potential issues before they result in equipment failure or downtime. This allows them to schedule maintenance and repairs at the most opportune times, reducing the impact on operations and minimizing costs.
The Benefits of Predictive Maintenance for Logistics Automation Systems
Implementing predictive maintenance strategies in logistics automation systems offers several key benefits:
1. Increased Uptime
By proactively identifying and addressing maintenance needs, logistics companies can significantly increase the uptime of their automation systems. This ensures that operations run smoothly and that products are delivered on time, improving customer satisfaction and loyalty.
2. Cost Savings
By avoiding unexpected breakdowns and reducing the need for costly emergency repairs, predictive maintenance can help logistics companies save money. It allows companies to plan maintenance activities in advance, schedule repairs during off-peak times, and reduce the need for expensive replacement parts.
3. Improved Safety
Regular maintenance and inspections can help identify potential safety issues before they cause accidents or injuries. By implementing predictive maintenance strategies, logistics companies can ensure that their automation systems are operating safely and in compliance with relevant regulations.
4. Enhanced Efficiency
Predictive maintenance enables logistics companies to optimize the performance of their automation systems. By addressing maintenance needs proactively, companies can reduce the likelihood of system failures and ensure that equipment is operating at peak efficiency. This allows companies to achieve higher throughput, reduce cycle times, and improve overall productivity.
Implementing Predictive Maintenance in Logistics Automation Systems
Implementing predictive maintenance in logistics automation systems requires a combination of technology, data analytics, and expertise. Here are some key steps to consider:
1. Data Collection and Analysis
The first step in implementing predictive maintenance is to collect and analyze relevant data. This includes data from sensors on automation equipment, as well as data from other sources such as maintenance records and historical performance data. By analyzing this data, logistics companies can identify patterns and trends that can help predict future maintenance needs.
2. Predictive Analytics
Predictive analytics tools and algorithms are used to analyze the collected data and identify patterns and anomalies. These tools can help logistics companies predict when equipment is likely to fail and recommend appropriate maintenance actions. By leveraging the power of predictive analytics, companies can optimize maintenance schedules and reduce the risk of equipment failures.
3. Integration with Fleet Management Systems
In order to effectively implement predictive maintenance, it is important to integrate the predictive analytics tools with existing fleet management systems. This allows companies to leverage real-time fleet data to make informed decisions about maintenance scheduling, optimize fleet performance, and improve overall efficiency.
4. Continuous Improvement
Predictive maintenance is an ongoing process that requires continuous monitoring and improvement. By regularly reviewing and analyzing data, logistics companies can refine their predictive models, identify new maintenance needs, and further optimize their maintenance schedules. Continuous improvement is key to maximizing the benefits of predictive maintenance and ensuring the long-term success of automation systems.
Conclusion
Predictive maintenance plays a crucial role in ensuring the uptime of logistics automation systems. By leveraging real-time data and analytics, logistics companies can proactively identify and address maintenance needs, optimize fleet performance, and minimize costly downtime. Implementing predictive maintenance strategies not only improves efficiency and reduces costs but also enhances safety and customer satisfaction. In today's highly competitive business environment, logistics companies cannot afford to overlook the importance of predictive maintenance in their automation systems.
Related Blogs
The benefits of implementing a preventive maintenance schedule for facility management
Read More