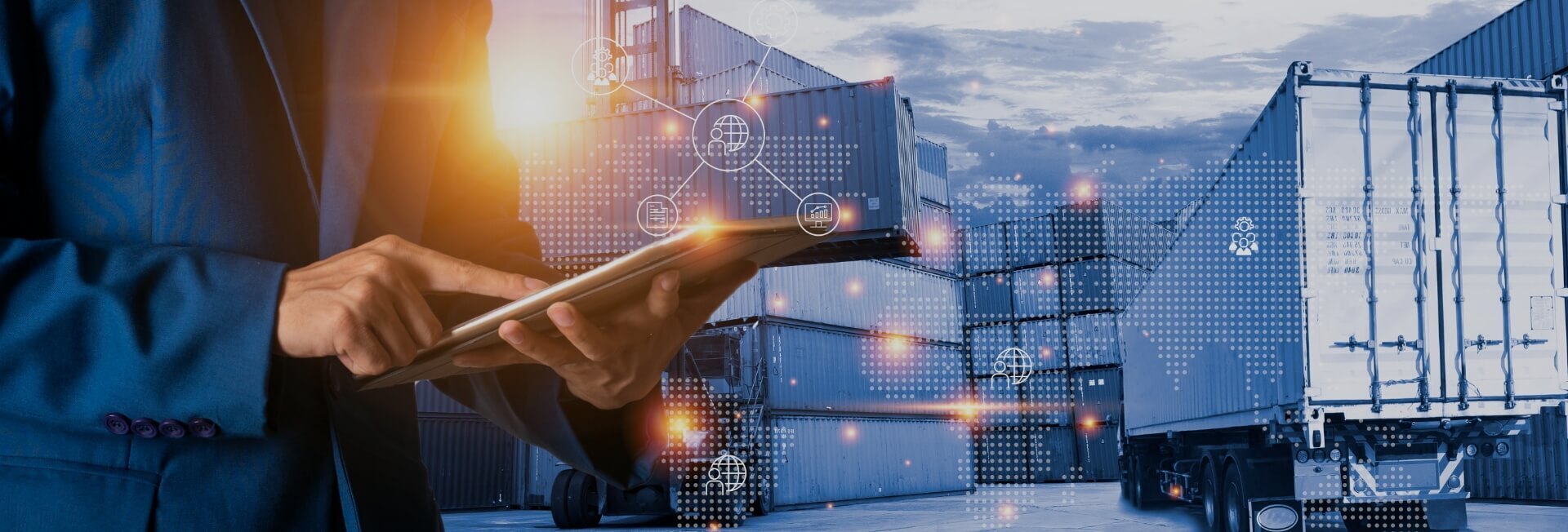
The role of maintenance scheduling in reducing downtime in manufacturing plants
- Home
- Resources
- Fleet Operations and Optimization
- The role of maintenance scheduling in reducing downtime in manufacturing plants
The Importance of Maintenance Scheduling in Manufacturing Plants
In the highly competitive world of manufacturing, minimizing downtime is crucial for maintaining productivity and profitability. Unplanned equipment failures and breakdowns can lead to costly delays, decreased production output, and unhappy customers. That's why implementing an effective maintenance scheduling system is essential for ensuring smooth operations and reducing downtime in manufacturing plants.
Preventive Maintenance: The Key to Avoiding Costly Breakdowns
Preventive maintenance is a proactive approach to equipment maintenance that involves regularly scheduled inspections, servicing, and repairs. By performing maintenance tasks before equipment failure occurs, manufacturing plants can prevent unexpected breakdowns and minimize downtime. Preventive maintenance not only helps to extend the lifespan of equipment but also avoids the need for costly repairs or replacements.
Implementing a comprehensive preventive maintenance program requires proper planning and scheduling. This involves creating a maintenance schedule that outlines the frequency and tasks to be performed for each piece of equipment. By adhering to this schedule, manufacturing plants can ensure that maintenance activities are carried out on time, reducing the risk of unexpected equipment failures.
The Benefits of Maintenance Scheduling
Maintenance scheduling offers several benefits for manufacturing plants, including:
1. Minimizing Downtime
Maintenance scheduling allows manufacturing plants to identify potential issues and address them before they cause equipment breakdowns. By proactively maintaining equipment, the risk of unexpected failures and subsequent downtime is significantly reduced. This ensures uninterrupted production and minimizes the impact on overall productivity.
2. Improved Equipment Performance
Regular maintenance helps to keep equipment in optimal condition, ensuring that it operates at peak performance. By scheduling routine inspections and servicing, manufacturing plants can identify and address minor issues before they escalate into major problems. This not only improves the reliability of equipment but also enhances its efficiency and effectiveness.
3. Enhanced Safety
Maintaining equipment in good working condition is essential for ensuring the safety of manufacturing plant personnel. Regular inspections and maintenance help to identify potential safety hazards and address them promptly. By minimizing the risk of accidents and injuries, maintenance scheduling creates a safer working environment for employees.
4. Cost Savings
While implementing a maintenance scheduling system requires an investment of time and resources, it can result in significant cost savings in the long run. By preventing equipment breakdowns and minimizing downtime, manufacturing plants can avoid costly repairs, replacements, and production delays. Additionally, regular maintenance helps to extend the lifespan of equipment, reducing the need for frequent replacements.
Implementing an Effective Maintenance Scheduling System
To implement an effective maintenance scheduling system, manufacturing plants should consider the following steps:
1. Equipment Inventory and Prioritization
Begin by creating an inventory of all the equipment in the manufacturing plant. This includes machinery, tools, vehicles, and any other assets that require regular maintenance. Once the inventory is complete, prioritize the equipment based on its criticality to operations and the potential impact of failure.
2. Establish Maintenance Intervals
For each piece of equipment, establish the appropriate maintenance intervals based on manufacturer recommendations and industry best practices. This includes determining the frequency of inspections, servicing, and repairs. Consider factors such as equipment age, usage, and operating conditions when establishing maintenance intervals.
3. Create a Maintenance Schedule
Using the equipment inventory and established maintenance intervals, create a comprehensive maintenance schedule. This schedule should clearly outline the tasks, frequency, and responsible personnel for each maintenance activity. Consider using maintenance management software to streamline scheduling and ensure timely execution of tasks.
4. Regularly Review and Update
Maintenance scheduling is an ongoing process that requires regular review and updates. As equipment ages or operating conditions change, the maintenance intervals and tasks may need to be adjusted. It's essential to periodically review the effectiveness of the maintenance scheduling system and make necessary modifications to optimize its performance.
The Role of Technology in Maintenance Scheduling
Advances in technology have greatly enhanced maintenance scheduling in manufacturing plants. The use of maintenance management software, fleet tracking systems, and real-time data analytics has revolutionized the way maintenance activities are planned and executed.
Maintenance management software provides a centralized platform for creating and managing maintenance schedules. It allows manufacturing plants to track equipment maintenance history, schedule tasks, assign responsibilities, and generate reports. By automating these processes, maintenance management software streamlines operations and ensures that maintenance activities are executed efficiently.
Fleet tracking systems, combined with real-time data analytics, enable manufacturing plants to monitor the health and performance of their equipment in real-time. These systems provide valuable insights into equipment usage, maintenance requirements, and potential issues. By leveraging this data, manufacturing plants can optimize maintenance scheduling and make data-driven decisions to prevent unplanned downtime.
Conclusion
Maintenance scheduling plays a critical role in reducing downtime and optimizing productivity in manufacturing plants. By implementing a comprehensive preventive maintenance program and utilizing technology-driven solutions, manufacturing plants can minimize equipment failures, improve performance, enhance safety, and achieve cost savings. Investing in maintenance scheduling is a proactive approach that pays off in the long run, ensuring uninterrupted operations and maintaining a competitive edge in the manufacturing industry.
Related Blogs
The benefits of implementing a preventive maintenance schedule for facility management
Read More