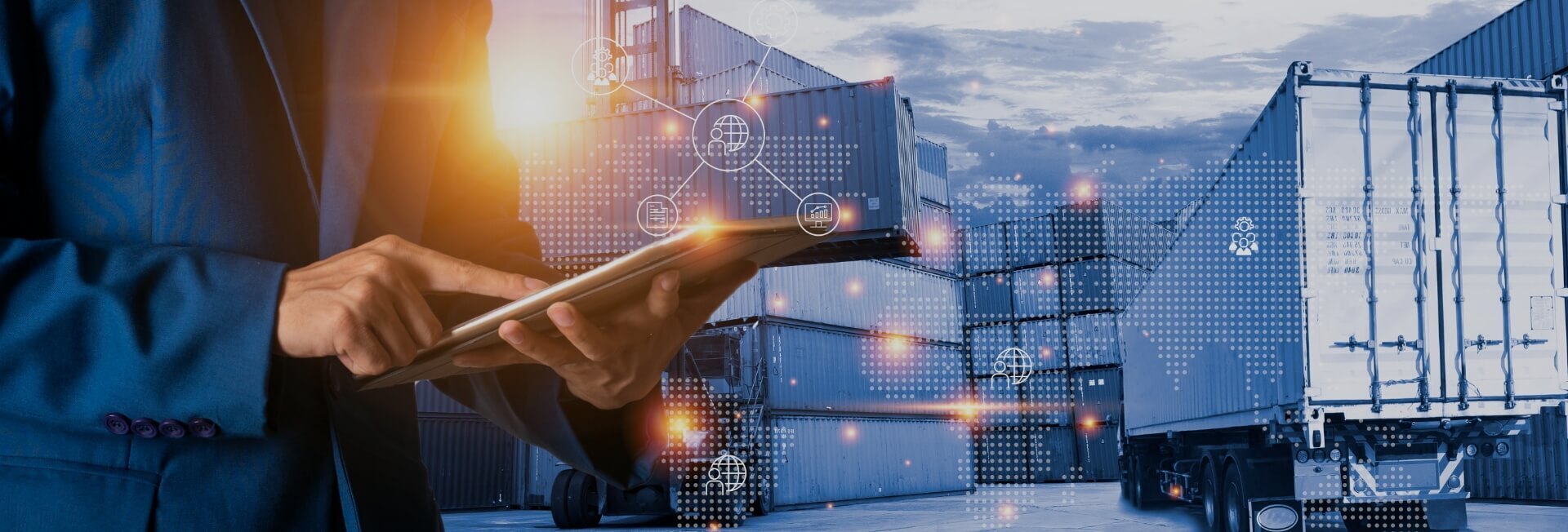
The role of maintenance scheduling in managing spare parts inventory
- Home
- Resources
- Fleet Operations and Optimization
- The role of maintenance scheduling in managing spare parts inventory
The Importance of Maintenance Scheduling in Managing Spare Parts Inventory
In any industry that relies on machinery and equipment, regular maintenance and repairs are essential to ensure smooth operations and prevent costly downtime. An effective maintenance scheduling system plays a crucial role in managing spare parts inventory and optimizing the overall maintenance process.
What is Maintenance Scheduling?
Maintenance scheduling refers to the process of planning and organizing maintenance activities to maximize equipment uptime while minimizing disruptions to operations. It involves creating a detailed schedule for conducting inspections, preventive maintenance tasks, repairs, and replacement of spare parts.
By implementing a well-designed maintenance scheduling system, organizations can ensure that equipment and machinery are regularly inspected and maintained according to manufacturer guidelines and industry best practices. This proactive approach helps identify and address potential issues before they escalate into costly breakdowns, ensuring smooth operations and extending the lifespan of assets.
The Role of Maintenance Scheduling in Spare Parts Inventory Management
Effective spare parts inventory management is crucial for organizations to minimize downtime and optimize maintenance costs. By incorporating maintenance scheduling into the overall spare parts management strategy, organizations can achieve the following benefits:
1. Preventive Maintenance
Preventive maintenance involves conducting routine inspections and maintenance tasks to identify and address potential issues before they lead to equipment failure. By implementing a maintenance scheduling system, organizations can ensure that preventive maintenance tasks are scheduled and performed regularly, reducing the risk of unexpected breakdowns and the need for emergency repairs.
Regular preventive maintenance also helps identify the need for spare parts replacement in advance, allowing organizations to stock the necessary parts and minimize downtime during maintenance activities.
2. Efficient Spare Parts Inventory Management
Maintenance scheduling provides organizations with a clear understanding of the spare parts required for each maintenance activity. By planning ahead and scheduling maintenance tasks, organizations can optimize their spare parts inventory by stocking the right parts in the right quantities.
With accurate inventory management, organizations can avoid overstocking or understocking of spare parts, reducing costs associated with storage and procurement. Additionally, it ensures that the required spare parts are readily available when needed, minimizing equipment downtime and improving overall operational efficiency.
3. Streamlined Logistics and Supply Chain
By incorporating maintenance scheduling into the spare parts inventory management process, organizations can streamline logistics and supply chain operations. With a clear schedule of maintenance activities, organizations can optimize the procurement and delivery of spare parts, ensuring they are available at the right time and place.
Integrating maintenance scheduling with fleet tracking and supply chain visibility systems allows organizations to track the movement and availability of spare parts in real-time. This enables proactive decision-making and ensures that spare parts are delivered to the required maintenance location promptly, minimizing delays and optimizing overall logistics efficiency.
4. Data-Driven Maintenance Decisions
Maintenance scheduling systems enable organizations to collect and analyze data related to equipment performance and maintenance activities. By leveraging this data, organizations can gain actionable insights into the maintenance requirements of different equipment, identify patterns and trends, and make data-driven decisions.
With access to real-time fleet data and comprehensive maintenance records, organizations can identify equipment that requires frequent repairs or spare parts replacement. This information can help prioritize maintenance activities, allocate resources efficiently, and optimize the overall maintenance process.
The Benefits of Maintenance Scheduling in Spare Parts Inventory Management
Implementing an effective maintenance scheduling system in spare parts inventory management offers several benefits:
1. Improved Fleet Maintenance Efficiency
Maintenance scheduling ensures that regular maintenance tasks are performed on time, minimizing the risk of unexpected breakdowns and maximizing equipment uptime. By proactively addressing maintenance needs, organizations can improve fleet maintenance efficiency and reduce the overall maintenance costs.
With a well-maintained fleet, organizations can also enhance operational safety, improve vehicle performance, and extend the lifespan of assets, resulting in significant cost savings in the long run.
2. Enhanced Logistics Automation
Integrating maintenance scheduling with logistics automation systems allows organizations to automate the process of spare parts procurement and delivery. By leveraging real-time fleet data and maintenance requirements, organizations can automate the generation of purchase orders, track spare parts inventory levels, and ensure timely delivery to maintenance locations.
This automation eliminates manual errors, reduces administrative tasks, and improves overall logistics efficiency. It also enables organizations to allocate resources effectively, optimize routes, and minimize transportation costs.
3. Real-Time Decision-Making
Maintenance scheduling systems provide organizations with real-time visibility into equipment status, maintenance activities, and spare parts availability. This enables proactive decision-making, allowing organizations to respond promptly to maintenance needs and minimize downtime.
With access to real-time data, organizations can prioritize maintenance activities based on equipment criticality, allocate resources efficiently, and make informed decisions regarding spare parts procurement and inventory management.
4. Optimal Spare Parts Inventory Management
By incorporating maintenance scheduling into spare parts inventory management, organizations can optimize their inventory levels. With accurate demand forecasting and planned maintenance activities, organizations can stock the required spare parts in the right quantities, eliminating excess inventory and reducing carrying costs.
Optimal spare parts inventory management ensures that the required parts are readily available when needed, minimizing equipment downtime and improving overall operational efficiency.
Conclusion
Maintenance scheduling plays a critical role in managing spare parts inventory and optimizing the overall maintenance process. By implementing an effective maintenance scheduling system, organizations can improve fleet maintenance efficiency, streamline logistics and supply chain operations, make data-driven decisions, and achieve optimal spare parts inventory management.
With the right combination of preventive maintenance, efficient spare parts inventory management, streamlined logistics, and real-time decision-making, organizations can minimize downtime, reduce maintenance costs, and enhance operational efficiency.
Related Blogs
The benefits of implementing a preventive maintenance schedule for facility management
Read More