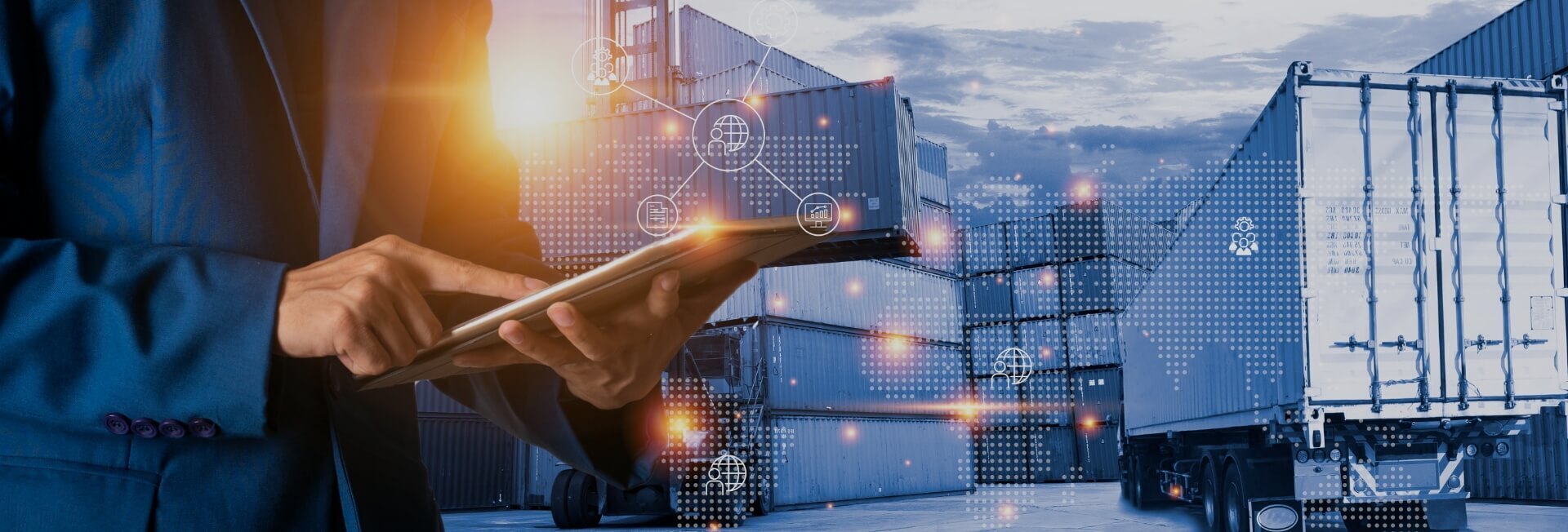
The role of maintenance scheduling in managing equipment recall and safety notifications
- Home
- Resources
- Fleet Operations and Optimization
- The role of maintenance scheduling in managing equipment recall and safety notifications
The Importance of Maintenance Scheduling in Managing Equipment Recall and Safety Notifications
Maintenance scheduling plays a crucial role in managing equipment recall and safety notifications in various industries. Whether it's a fleet of vehicles, manufacturing equipment, or medical devices, regular maintenance is essential to ensure optimal performance, prevent breakdowns, and address any safety concerns. By implementing a strategic maintenance schedule, companies can streamline operations, minimize downtime, and ensure compliance with safety regulations.
Preventive Maintenance for Fleet Optimization
One area where maintenance scheduling is particularly critical is fleet management. Fleet optimization involves maximizing efficiency, reducing costs, and improving overall performance. Preventive maintenance plays a key role in achieving these objectives. By implementing a proactive maintenance schedule, fleet managers can identify and address potential issues before they escalate, avoiding costly breakdowns and ensuring that vehicles are safe to operate.
Preventive maintenance involves regularly scheduled inspections, servicing, and repairs based on manufacturer recommendations and industry best practices. This proactive approach helps extend the lifespan of fleet vehicles, reduce the likelihood of accidents due to mechanical failures, and maintain compliance with safety regulations. It also allows fleet managers to plan and allocate resources effectively, reducing operational disruptions and improving customer satisfaction.
Streamlined Logistics and Supply Chain Optimization
Maintenance scheduling is not only crucial for fleet optimization but also for streamlined logistics and supply chain optimization. In the logistics industry, efficient operations and timely deliveries are essential for meeting customer demands and maintaining a competitive edge. Any disruptions in the supply chain can result in delays, increased costs, and customer dissatisfaction.
By implementing a comprehensive maintenance schedule, logistics companies can minimize the risk of equipment failures and breakdowns, ensuring that their operations run smoothly. With real-time fleet data and actionable insights, logistics managers can identify potential maintenance issues, schedule repairs or replacements, and ensure that all vehicles and equipment are in optimal condition.
Maintenance Automation and Real-Time Decision-Making
Advancements in technology have made maintenance scheduling more efficient and effective. With the help of fleet management software and automation tools, companies can streamline their maintenance processes and make real-time data-driven decisions. These tools provide real-time visibility into the condition of vehicles and equipment, allowing managers to prioritize maintenance tasks based on urgency and importance.
Maintenance automation also enables companies to track recall and safety notifications more effectively. By integrating maintenance scheduling with recall and safety databases, companies can ensure that all affected equipment is promptly identified and addressed. This proactive approach helps mitigate potential risks and ensures compliance with safety regulations.
Benefits of Effective Maintenance Scheduling
Implementing an effective maintenance scheduling system offers numerous benefits for companies across different industries:
1. Improved Equipment Reliability and Performance
Regular maintenance and inspections help identify potential issues and address them before they lead to breakdowns or accidents. This improves the reliability and performance of equipment, ensuring that it operates at its optimal level.
2. Minimized Downtime and Productivity Loss
Unplanned downtime due to equipment failures can result in significant productivity loss and increased costs. By implementing a proactive maintenance schedule, companies can minimize downtime and avoid disruptions in operations.
3. Enhanced Safety and Compliance
Maintenance scheduling ensures that equipment is regularly inspected and maintained to meet safety standards and comply with industry regulations. This reduces the risk of accidents, injuries, and potential legal liabilities.
4. Cost Savings
Regular maintenance helps identify and address minor issues before they escalate into major problems. This reduces the need for costly repairs or replacements and extends the lifespan of equipment, resulting in significant cost savings over time.
5. Improved Customer Satisfaction
Efficient maintenance scheduling ensures that equipment is in optimal condition, reducing the risk of breakdowns or delays in service. This improves customer satisfaction and helps maintain a positive reputation in the market.
Conclusion
Maintenance scheduling plays a crucial role in managing equipment recall and safety notifications. Whether it's for fleet optimization, streamlined logistics, or supply chain optimization, implementing an effective maintenance schedule helps companies minimize downtime, improve safety, and achieve cost savings. With the advancements in maintenance automation and real-time data-driven decision-making, companies can ensure that their equipment is in optimal condition, reduce the risk of accidents, and comply with safety regulations. By prioritizing maintenance scheduling, companies can enhance their overall operational efficiency and maintain a competitive edge in the market.
Related Blogs
The benefits of implementing a preventive maintenance schedule for facility management
Read More