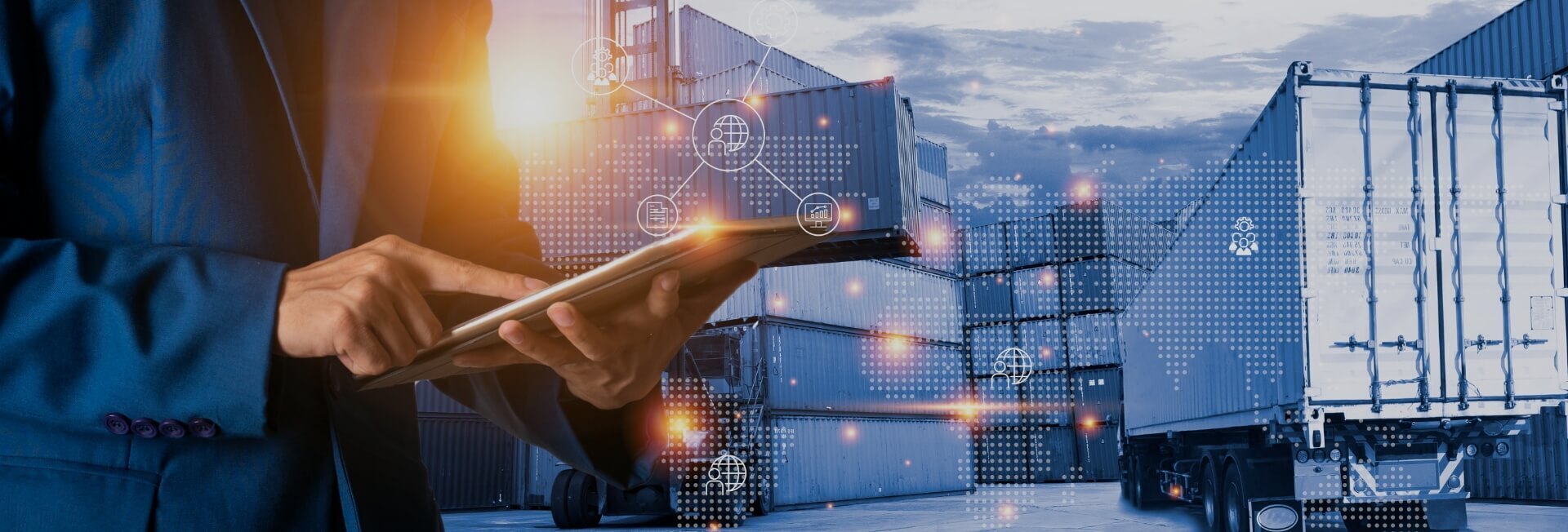
The role of maintenance scheduling in managing equipment failure analysis and root cause analysis
- Home
- Resources
- Fleet Operations and Optimization
- The role of maintenance scheduling in managing equipment failure analysis and root cause analysis
The Role of Maintenance Scheduling in Managing Equipment Failure Analysis and Root Cause Analysis
Preventive maintenance is a critical aspect of fleet management that helps ensure the smooth operation of vehicles and equipment. By implementing a comprehensive maintenance scheduling system, fleet managers can effectively manage equipment failure analysis and root cause analysis. This proactive approach to maintenance not only reduces downtime and repairs but also improves fleet maintenance efficiency and overall logistics operations.
Preventive Maintenance and Fleet Tracking
Preventive maintenance involves regular inspections, servicing, and repairs of vehicles and equipment to prevent breakdowns and extend their lifespan. By implementing a preventive maintenance program and integrating fleet tracking technologies, fleet managers can gain supply chain visibility and optimize their operations.
Fleet tracking systems use GPS and telematics technologies to provide real-time data and insights into the performance and location of vehicles. This data allows fleet managers to monitor the health of vehicles and equipment, identify potential issues, and schedule maintenance tasks proactively. With this information, they can ensure that vehicles are serviced and repaired before any major failures occur, preventing costly breakdowns and ensuring the efficient operation of the fleet.
Actionable Insights for Streamlined Logistics
Maintenance scheduling, when combined with fleet tracking, provides actionable insights that can streamline logistics operations. By analyzing the data collected from vehicles and equipment, fleet managers can identify patterns and trends that can help optimize their supply chain and improve overall efficiency.
For example, by analyzing fuel consumption data, fleet managers can identify vehicles that are consuming more fuel than usual. This could indicate a potential issue with the engine or fuel system, which can be addressed through scheduled maintenance. By addressing these issues promptly, fleet managers can avoid more significant problems and improve fuel efficiency, leading to cost savings and reduced environmental impact.
Maintenance Scheduling for Equipment Failure Analysis and Root Cause Analysis
Maintenance scheduling plays a crucial role in equipment failure analysis and root cause analysis. By implementing a structured maintenance schedule, fleet managers can collect data on the performance and condition of vehicles and equipment over time.
This data can then be used to analyze equipment failures and identify the root causes behind them. By understanding the underlying issues that lead to failures, fleet managers can take proactive measures to prevent similar incidents in the future. This could involve adjusting maintenance procedures, upgrading equipment, or providing additional training to operators.
For example, if a vehicle consistently experiences engine failures, maintenance scheduling can help identify whether it is due to a specific component or operator error. By analyzing the maintenance records and conducting root cause analysis, fleet managers can determine the necessary actions to prevent future failures. This could involve implementing additional maintenance tasks, replacing faulty components, or providing training to operators on proper vehicle operation and maintenance.
Benefits of Maintenance Scheduling
Implementing a maintenance scheduling system offers several benefits for fleet managers and logistics operations:
1. Improved Fleet Maintenance Efficiency: By proactively scheduling maintenance tasks, fleet managers can reduce unplanned downtime and repairs. This leads to improved fleet maintenance efficiency and ensures that vehicles and equipment are in optimal condition for operations.
2. Cost Savings: Preventive maintenance helps identify potential issues before they become major failures, reducing the cost of repairs and replacements. By addressing minor issues promptly, fleet managers can avoid more significant problems that could result in costly breakdowns and extended downtime.
3. Increased Equipment Lifespan: Regular inspections and maintenance tasks help extend the lifespan of vehicles and equipment. By properly maintaining assets, fleet managers can maximize their return on investment and reduce the need for frequent replacements.
4. Enhanced Safety: Maintenance scheduling ensures that vehicles and equipment are regularly inspected and serviced, reducing the risk of accidents and breakdowns. This promotes a safer working environment for operators and other road users.
5. Data-Driven Fleet Management: By collecting and analyzing maintenance data, fleet managers can make informed decisions regarding their fleet operations. This data-driven approach allows them to identify trends, optimize maintenance schedules, and allocate resources more effectively.
Implementing Maintenance Scheduling and Fleet Automation
To effectively implement maintenance scheduling and reap its benefits, fleet managers can leverage fleet automation solutions. These software platforms provide real-time fleet data, automated maintenance scheduling, and comprehensive fleet management tools.
By integrating fleet automation into their operations, fleet managers can streamline maintenance processes, reduce administrative tasks, and improve overall efficiency. These platforms provide a centralized dashboard where fleet managers can monitor the health and performance of vehicles, schedule maintenance tasks, and track repairs and replacements.
Fleet automation solutions also offer features such as predictive maintenance, which uses advanced analytics and machine learning algorithms to predict equipment failures and recommend maintenance actions. This proactive approach helps fleet managers address potential issues before they impact operations, further improving fleet maintenance efficiency and reducing costs.
Conclusion
Maintenance scheduling plays a crucial role in managing equipment failure analysis and root cause analysis. By implementing preventive maintenance and leveraging fleet tracking technologies, fleet managers can gain supply chain visibility, optimize logistics operations, and improve fleet maintenance efficiency.
By collecting and analyzing maintenance data, fleet managers can identify patterns and trends, leading to streamlined logistics and enhanced decision-making. Implementing maintenance scheduling and leveraging fleet automation solutions can further enhance these benefits, providing real-time fleet data, predictive maintenance, and comprehensive fleet management tools.
With a proactive approach to maintenance, fleet managers can ensure the smooth operation of their vehicles and equipment, reduce downtime and repairs, and maximize the lifespan of their assets. This ultimately leads to improved fleet efficiency, cost savings, and a safer working environment for operators and other road users.
Related Blogs
The benefits of implementing a preventive maintenance schedule for facility management
Read More