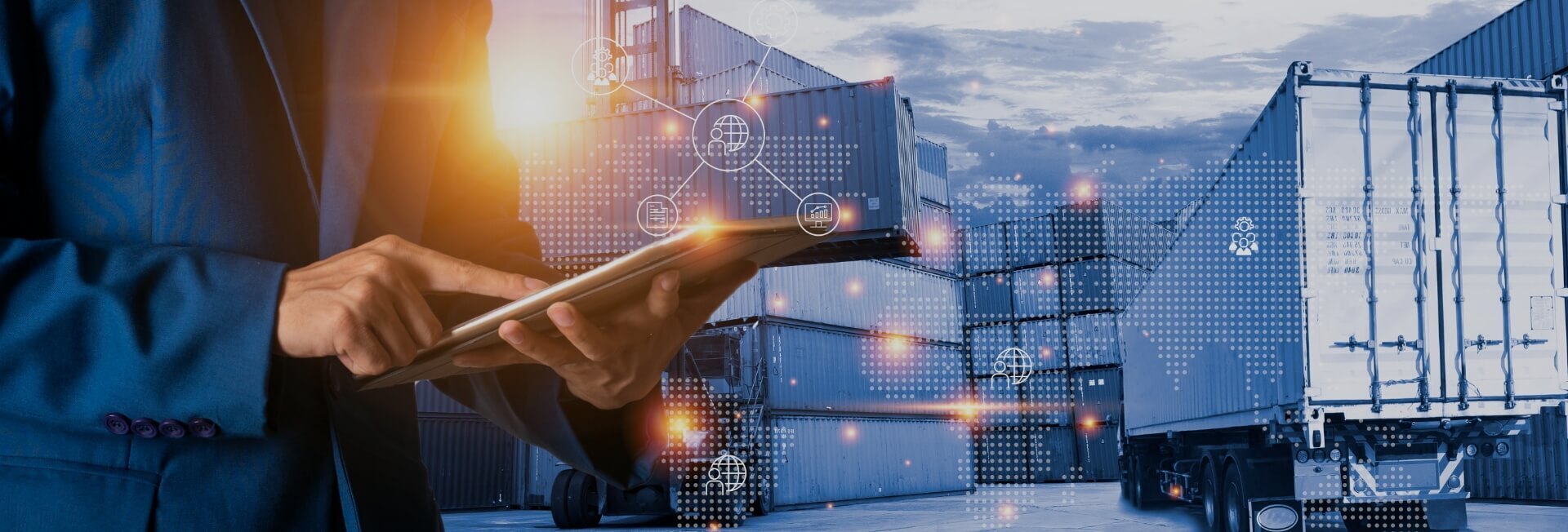
The role of maintenance scheduling in managing equipment documentation and maintenance records
- Home
- Resources
- Fleet Operations and Optimization
- The role of maintenance scheduling in managing equipment documentation and maintenance records
Proper maintenance scheduling plays a crucial role in managing equipment documentation and maintenance records. In industries that rely on fleet management and logistics, such as transportation, construction, and manufacturing, it is essential to have a well-organized system for scheduling and documenting maintenance activities. This ensures that equipment remains in optimal condition, downtime is minimized, and safety standards are upheld. In this article, we will explore the significance of maintenance scheduling and how it contributes to efficient fleet maintenance and streamlined logistics.
Preventive Maintenance and Fleet Optimization
Preventive maintenance is a proactive approach to equipment maintenance that aims to prevent breakdowns and minimize the need for corrective repairs. By following a regular maintenance schedule, fleet managers can address potential issues before they escalate, saving both time and money. Preventive maintenance includes tasks such as oil changes, filter replacements, tire rotations, and inspections. These routine maintenance activities not only keep equipment running smoothly but also extend their lifespan.
Incorporating maintenance scheduling into fleet management allows for optimization of resources and assets. By keeping track of maintenance activities, fleet managers can identify patterns and make informed decisions regarding equipment repairs, replacements, and retirements. This data-driven approach ensures that resources are allocated efficiently and that the fleet operates at its maximum potential.
Streamlined Logistics and Supply Chain Optimization
Efficient logistics is crucial for businesses that rely on the movement of goods and materials. Maintenance scheduling plays a significant role in ensuring streamlined logistics and optimizing the supply chain. By keeping equipment in top condition through regular maintenance, the risk of breakdowns and delays is minimized. This leads to improved delivery times, increased customer satisfaction, and enhanced supply chain visibility.
Supply chain optimization involves the integration of various processes and systems to maximize efficiency and minimize costs. By incorporating maintenance scheduling into the supply chain management strategy, businesses can ensure that equipment is available when needed, reducing unexpected downtime and disruptions. This proactive approach to maintenance contributes to the overall optimization of the supply chain, leading to improved operational performance and a competitive advantage in the market.
Actionable Insights and Real-Time Decision-Making
Maintenance scheduling allows fleet managers to collect and analyze data related to equipment performance and maintenance activities. This data provides actionable insights that can drive real-time decision-making. For example, by analyzing maintenance records, fleet managers can identify trends and patterns, such as recurring breakdowns or high maintenance costs for specific equipment. Armed with this information, they can make informed decisions regarding equipment replacements, upgrades, or changes in maintenance procedures.
Real-time fleet data is essential for effective maintenance scheduling. By utilizing fleet tracking and telematics technologies, fleet managers can monitor the performance of equipment in real-time. This enables them to detect potential issues early on and schedule maintenance accordingly. Real-time data also allows for more accurate and efficient scheduling, as fleet managers can take into account factors such as equipment availability, driver schedules, and geographic location.
Maintenance Automation and Documentation Management
Maintenance scheduling can be significantly enhanced through the use of automation and digital documentation management systems. Automated maintenance scheduling software can streamline the process by automatically generating maintenance tasks based on predefined schedules or equipment usage. This eliminates the need for manual scheduling and reduces the risk of errors or missed maintenance activities.
Additionally, digital documentation management systems allow for centralized storage and easy retrieval of maintenance records. This eliminates the need for manual record-keeping and reduces the risk of lost or misplaced documentation. Digital records can also be easily accessed and shared, improving collaboration between different departments and stakeholders.
Conclusion
Maintenance scheduling plays a vital role in managing equipment documentation and maintenance records. By implementing a well-organized system for scheduling and documenting maintenance activities, businesses can improve fleet maintenance efficiency, streamline logistics, and optimize the supply chain. Preventive maintenance and real-time monitoring contribute to the overall optimization of the fleet, minimizing downtime and maximizing equipment lifespan. Actionable insights derived from maintenance data enable informed decision-making, leading to improved operational performance and cost savings. Automation and digital documentation management systems further enhance maintenance scheduling processes, reducing manual tasks and improving record-keeping. In today's data-driven world, businesses that prioritize maintenance scheduling are better equipped to meet the demands of efficient fleet management and streamlined logistics.
Related Blogs
The benefits of implementing a preventive maintenance schedule for facility management
Read More