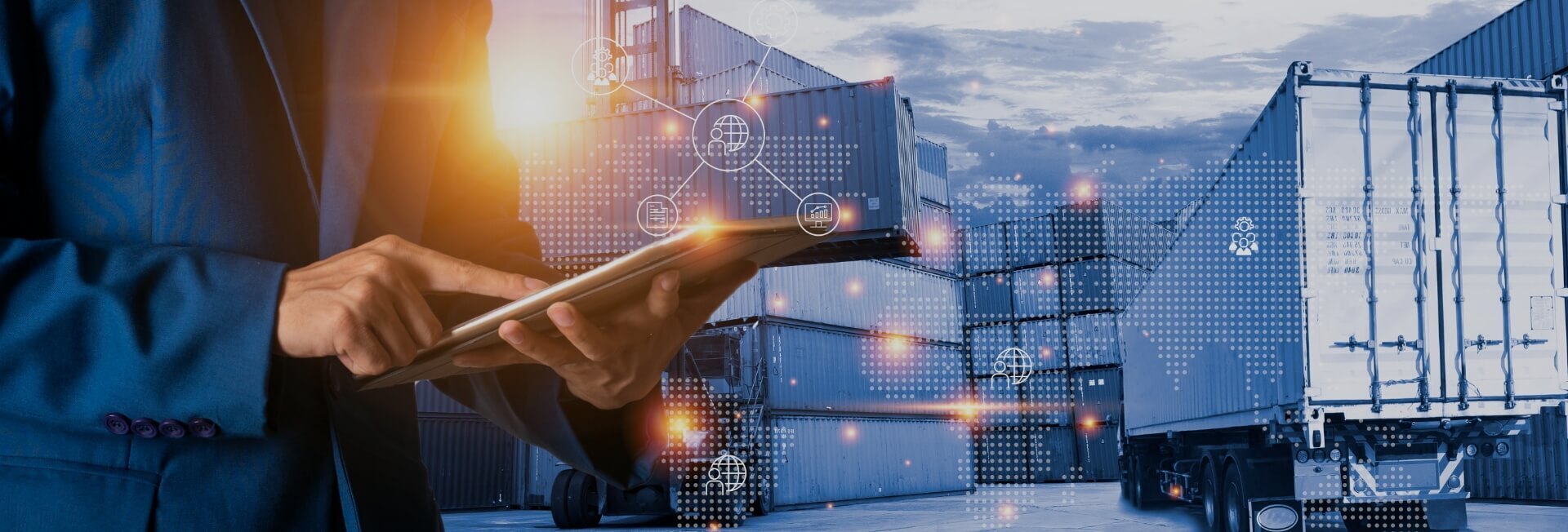
The role of maintenance scheduling in managing equipment calibration and validation processes
- Home
- Resources
- Fleet Operations and Optimization
- The role of maintenance scheduling in managing equipment calibration and validation processes
The Role of Maintenance Scheduling in Managing Equipment Calibration and Validation Processes
In industries that rely heavily on equipment and machinery, such as manufacturing, healthcare, and research, maintaining the accuracy and reliability of these assets is crucial. Equipment calibration and validation processes are essential to ensure that the equipment is functioning within the required specifications and producing accurate results. To effectively manage these processes, maintenance scheduling plays a crucial role. In this article, we will explore the importance of maintenance scheduling in managing equipment calibration and validation processes and how it contributes to overall operational efficiency.
Preventive Maintenance for Equipment Calibration and Validation
Preventive maintenance is a key component of equipment calibration and validation processes. It involves regularly scheduled inspections, adjustments, and maintenance activities to ensure that the equipment is functioning optimally and producing accurate results. By implementing an effective maintenance scheduling system, organizations can proactively plan and execute preventive maintenance tasks, minimizing the risk of equipment failure and reducing the need for unscheduled repairs.
Maintenance scheduling allows organizations to establish a routine maintenance plan for each piece of equipment, including calibration and validation activities. By adhering to a predetermined schedule, organizations can ensure that equipment is regularly calibrated and validated, reducing the risk of inaccuracies and errors in measurements and test results. This not only ensures the quality and accuracy of the products or services being produced but also helps organizations comply with industry regulations and standards.
Streamlined Logistics and Supply Chain Optimization
Efficient maintenance scheduling also contributes to streamlined logistics and supply chain optimization. By properly scheduling equipment calibration and validation activities, organizations can minimize downtime and disruptions in their operations. This allows for a more efficient use of resources and reduces the impact on overall production schedules and supply chain timelines.
With the integration of fleet tracking and maintenance scheduling systems, organizations can gain real-time visibility into the status and location of their assets. This enables them to allocate resources effectively, plan maintenance activities, and optimize logistics operations. By having access to actionable insights and comprehensive fleet management data, organizations can make data-driven decisions to improve fleet maintenance efficiency and overall logistics performance.
Enhanced Equipment Reliability and Longevity
Regular equipment calibration and validation, facilitated by maintenance scheduling, significantly contributes to the reliability and longevity of the equipment. By identifying and addressing potential issues early on, organizations can prevent major breakdowns or failures that could result in costly repairs or replacement.
Maintenance scheduling allows organizations to keep a detailed record of each equipment's maintenance history, including calibration and validation activities. This historical data provides valuable insights into the performance and condition of the equipment over time. By analyzing this data, organizations can identify patterns, predict maintenance needs, and proactively address potential issues before they escalate.
Efficient Resource Allocation and Cost Management
Effective maintenance scheduling enables organizations to allocate resources efficiently and manage costs associated with equipment calibration and validation processes. By planning and scheduling maintenance activities in advance, organizations can ensure that the necessary resources, such as skilled technicians, tools, and spare parts, are available when needed. This minimizes delays and reduces the time and effort required to complete the maintenance tasks.
Furthermore, maintenance scheduling allows organizations to optimize the use of resources by grouping similar maintenance activities together. For example, if multiple pieces of equipment require calibration, organizations can schedule these activities at the same time, reducing downtime and maximizing the productivity of technicians.
Conclusion
Maintenance scheduling plays a critical role in managing equipment calibration and validation processes. By implementing an effective maintenance scheduling system, organizations can ensure that equipment is regularly calibrated and validated, contributing to overall operational efficiency. Preventive maintenance, streamlined logistics, enhanced equipment reliability, and efficient resource allocation are just a few of the benefits that can be achieved through proper maintenance scheduling. With the integration of advanced technologies, such as fleet tracking and maintenance automation, organizations can further optimize their maintenance processes and achieve higher levels of efficiency and accuracy in their operations.
Related Blogs
The benefits of implementing a preventive maintenance schedule for facility management
Read More