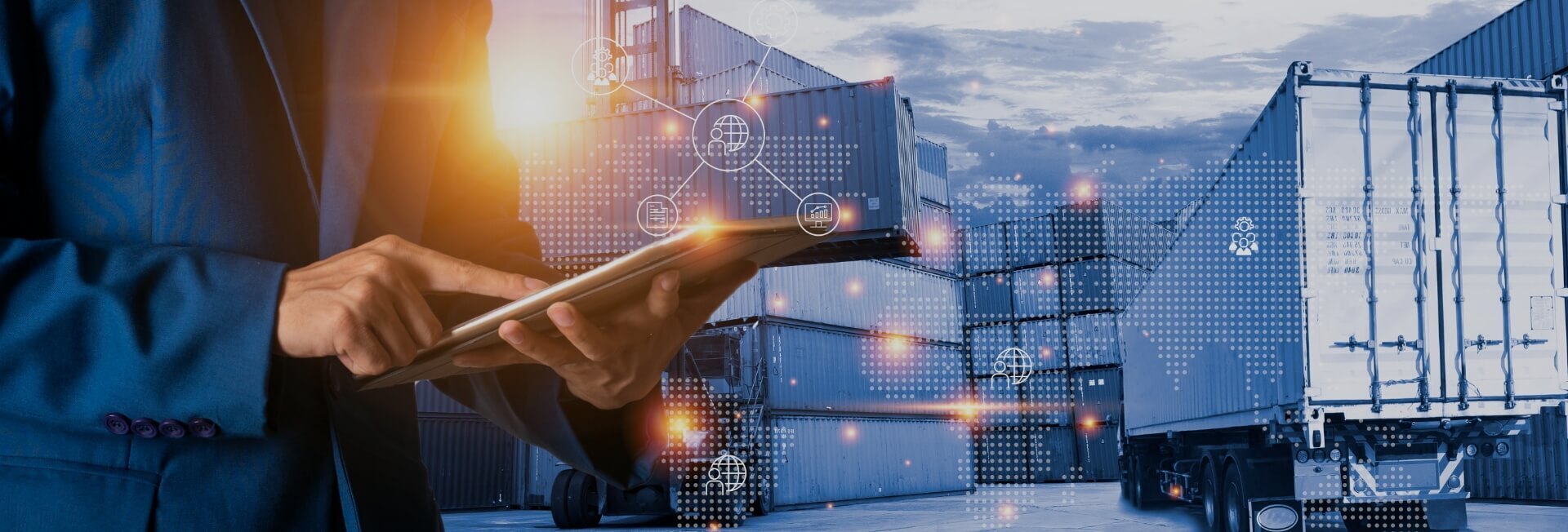
The role of maintenance automation in reducing human error
- Home
- Resources
- Fleet Operations and Optimization
- The role of maintenance automation in reducing human error
The Role of Maintenance Automation in Reducing Human Error
In today's fast-paced world, where logistics and supply chain operations are becoming increasingly complex, the role of maintenance automation has never been more crucial. Fleet maintenance plays a vital role in ensuring the smooth operation of businesses that rely on transportation and logistics. However, human error in maintenance processes can lead to costly breakdowns, delays, and safety issues. By implementing maintenance automation solutions, organizations can mitigate the risk of human error and improve overall fleet maintenance efficiency.
Preventive Maintenance: The Foundation of Fleet Maintenance Efficiency
Preventive maintenance is the cornerstone of effective fleet maintenance management. It involves regularly scheduled inspections, servicing, and repairs to identify and address potential issues before they escalate into major problems. By automating preventive maintenance tasks, organizations can ensure that all vehicles and equipment are maintained according to manufacturer recommendations and industry standards.
Automated maintenance scheduling systems can generate work orders based on predefined maintenance intervals, mileage, or engine hours. These systems can also send notifications and reminders to maintenance technicians, ensuring that preventive maintenance tasks are completed on time. By adhering to a proactive maintenance approach, organizations can minimize the risk of unplanned breakdowns, reduce vehicle downtime, and improve fleet reliability.
Fleet Tracking: Enhancing Supply Chain Visibility and Optimization
Effective fleet tracking is another crucial component of maintenance automation. By leveraging GPS technology, organizations can gain real-time visibility into the location and status of their vehicles. Fleet tracking systems provide comprehensive data on vehicle speed, fuel consumption, engine diagnostics, and driver behavior. This data can be used to identify potential maintenance issues, such as excessive idling, harsh braking, or engine faults.
With supply chain visibility, organizations can optimize their logistics operations by identifying inefficiencies and bottlenecks. By analyzing real-time fleet data, organizations can make data-driven decisions to streamline logistics processes, improve route planning, and reduce overall transportation costs. Fleet tracking also enables organizations to monitor vehicle utilization and identify opportunities for right-sizing their fleet, further optimizing operational efficiency.
Data-Driven Fleet Management: Actionable Insights for Efficient Maintenance
One of the key advantages of maintenance automation is the ability to collect and analyze vast amounts of data. By leveraging advanced analytics and machine learning algorithms, organizations can gain actionable insights into their fleet's performance and maintenance needs. Data-driven fleet management enables organizations to identify patterns, trends, and anomalies that may go unnoticed with manual processes.
With comprehensive fleet management software, organizations can generate customized reports and dashboards that provide real-time visibility into key maintenance metrics. These metrics can include average repair costs, mean time between failures, and overall fleet maintenance efficiency. By analyzing these metrics, organizations can identify areas for improvement, implement preventive measures, and optimize their maintenance strategies.
The Benefits of Maintenance Automation
Implementing maintenance automation solutions offers numerous benefits for organizations:
1. Improved Efficiency: Maintenance automation streamlines maintenance processes, reducing the time and effort required to manage and execute maintenance tasks. This allows maintenance technicians to focus on more complex and critical repairs, improving overall efficiency.
2. Cost Savings: By implementing preventive maintenance and addressing potential issues before they escalate, organizations can reduce the need for costly repairs and minimize vehicle downtime. Additionally, data-driven decision-making can help optimize maintenance schedules and minimize unnecessary maintenance expenses.
3. Enhanced Safety: Regular maintenance and inspections ensure that vehicles are in optimal condition, reducing the risk of accidents and ensuring the safety of drivers and other road users. Maintenance automation helps organizations stay compliant with safety regulations and industry standards.
4. Increased Reliability: By proactively addressing maintenance needs, organizations can improve the reliability of their fleet. This leads to fewer breakdowns, reduced service disruptions, and improved customer satisfaction.
5. Real-Time Fleet Data: With maintenance automation, organizations have access to real-time data on their fleet's performance and maintenance needs. This enables them to make informed decisions and take immediate action in response to critical maintenance issues.
Conclusion
Maintenance automation plays a vital role in reducing human error and improving fleet maintenance efficiency. By implementing preventive maintenance, leveraging fleet tracking technology, and embracing data-driven decision-making, organizations can optimize their maintenance processes and enhance overall operational efficiency. With streamlined logistics, improved fleet visibility, and actionable insights, organizations can minimize downtime, reduce costs, and ensure the smooth operation of their logistics and supply chain operations.
Related Blogs
The benefits of implementing a preventive maintenance schedule for facility management
Read More