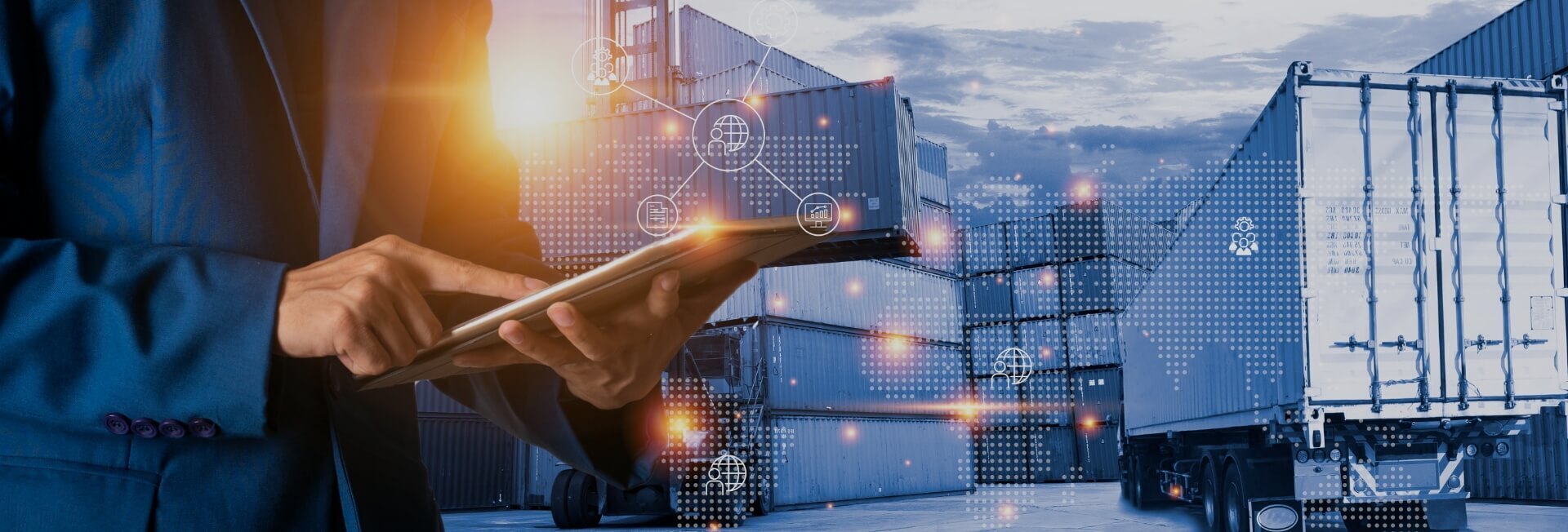
The role of digital twins in optimizing warehouse layouts for logistics automation
- Home
- Resources
- Fleet Operations and Optimization
- The role of digital twins in optimizing warehouse layouts for logistics automation
The Power of Digital Twins in Streamlining Warehouse Logistics
Logistics automation has become a key focus in today's fast-paced world. With the increasing demand for efficient supply chains and streamlined logistics processes, companies are turning to technology to optimize their warehouse layouts. One technology that is gaining traction in the industry is the use of digital twins. In this article, we will explore the role of digital twins in optimizing warehouse layouts for logistics automation.
What are Digital Twins?
Digital twins are virtual replicas of physical objects, processes, or systems. They are created using real-time data and advanced analytics to simulate the behavior and performance of the physical entity. In the context of warehouse logistics, a digital twin can represent the layout, equipment, and operations of a warehouse. By creating a digital twin, companies can gain a virtual representation of their warehouse and use it to make data-driven decisions to optimize their logistics processes.
Benefits of Digital Twins in Warehouse Layout Optimization
Using digital twins in warehouse layout optimization offers several benefits for companies:
1. Enhanced Supply Chain Visibility
Supply chain visibility is crucial for companies to monitor and manage their logistics operations effectively. With a digital twin of their warehouse, companies can gain real-time insights into the location and status of their inventory, equipment, and personnel. This visibility enables them to identify bottlenecks, optimize workflows, and make informed decisions to improve overall supply chain efficiency.
2. Improved Logistics Efficiency
Logistics efficiency is a key factor in ensuring timely deliveries and reducing costs. By analyzing the data generated by the digital twin, companies can identify inefficiencies in their warehouse layout and make necessary adjustments. For example, they can optimize the placement of inventory to minimize travel distances, reduce handling time, and improve order fulfillment rates. This leads to faster, more efficient logistics operations.
3. Real-Time Decision-Making
Real-time data is essential for making informed decisions and taking proactive actions. With a digital twin, companies can access real-time information about their warehouse operations, allowing them to respond quickly to any issues or changes in the supply chain. For example, if a certain area of the warehouse is experiencing a high volume of orders, the digital twin can provide insights on how to reorganize the layout to accommodate the increased demand.
4. Preventive Maintenance and Fleet Optimization
Preventive maintenance is crucial for keeping warehouse equipment and vehicles in optimal condition. By integrating sensors and IoT devices with the digital twin, companies can monitor the performance and health of their assets in real-time. This allows them to schedule maintenance activities proactively, reducing the risk of unexpected breakdowns and costly repairs. Additionally, the digital twin can be used to optimize fleet routes and schedules, ensuring efficient use of resources and minimizing downtime.
Implementing Digital Twins in Warehouse Layout Optimization
Implementing digital twins in warehouse layout optimization involves several steps:
1. Data Collection and Integration
The first step is to collect and integrate data from various sources, such as warehouse management systems, IoT devices, and sensors. This data includes information about inventory levels, equipment performance, personnel movements, and other relevant metrics. By integrating this data into the digital twin, companies can create a comprehensive and accurate representation of their warehouse operations.
2. Simulation and Analysis
Once the digital twin is created, companies can simulate different scenarios and analyze the impact of potential changes to the warehouse layout. For example, they can test the effects of relocating certain inventory items or rearranging equipment. By running simulations, companies can identify the most efficient layout that maximizes productivity and minimizes costs.
3. Optimization and Implementation
Based on the results of the simulations, companies can optimize their warehouse layout and implement the necessary changes. This may involve rearranging storage racks, reorganizing workstations, or adjusting material flow paths. The digital twin serves as a blueprint for the optimized layout, guiding the implementation process and ensuring consistency between the virtual and physical environments.
4. Continuous Monitoring and Improvement
Once the optimized layout is implemented, companies can continuously monitor and gather data from the warehouse operations. This data can be fed back into the digital twin to further improve its accuracy and effectiveness. By continuously monitoring and making data-driven adjustments, companies can ensure that their warehouse layout remains optimized and aligned with their evolving business needs.
The Future of Warehouse Logistics
Digital twins have the potential to revolutionize warehouse logistics by enabling companies to optimize their layouts for maximum efficiency and productivity. As technology continues to advance, digital twins will become more sophisticated, incorporating advanced analytics, machine learning, and artificial intelligence. This will further enhance the capabilities of digital twins in predicting and optimizing warehouse operations.
In conclusion, digital twins offer a powerful tool for companies to optimize their warehouse layouts for logistics automation. By creating a virtual replica of their warehouse, companies can gain valuable insights, make data-driven decisions, and continuously improve their logistics operations. With the benefits of enhanced supply chain visibility, improved logistics efficiency, real-time decision-making, and preventive maintenance, digital twins are shaping the future of warehouse logistics.
Related Blogs
The benefits of implementing a preventive maintenance schedule for facility management
Read More