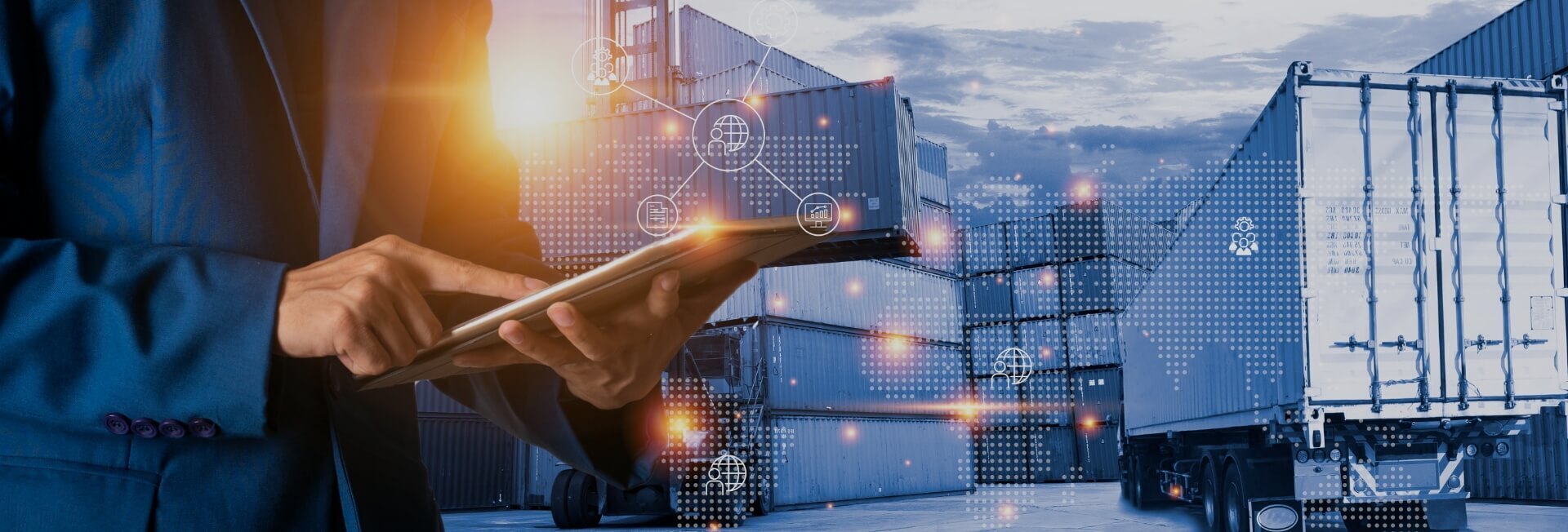
The role of collaborative robots in improving worker safety in logistics automation
- Home
- Resources
- Fleet Operations and Optimization
- The role of collaborative robots in improving worker safety in logistics automation
The Evolution of Logistics Automation
Logistics automation has come a long way in recent years, with advancements in technology revolutionizing the way products are stored, transported, and delivered. One of the most significant developments in this field is the integration of collaborative robots, or cobots, into the supply chain. These robots work alongside human workers to perform tasks such as picking, packing, and sorting, improving efficiency and productivity. However, beyond their ability to streamline operations, cobots also play a crucial role in enhancing worker safety.
Preventive Maintenance for Improved Safety
Preventive maintenance is a key aspect of ensuring worker safety in logistics automation. By regularly inspecting and servicing robots and equipment, potential issues can be identified and resolved before they lead to accidents or breakdowns. Collaborative robots are equipped with sensors and monitoring systems that allow them to detect abnormalities in their operation. These systems can provide real-time data on the robot's performance, enabling maintenance personnel to proactively address any issues. This preventive approach not only reduces the risk of accidents but also minimizes downtime and costly repairs.
Streamlined Logistics for Efficient Operations
Collaborative robots contribute to improved worker safety by streamlining logistics operations. By automating repetitive and physically demanding tasks, cobots reduce the risk of injuries associated with manual labor. For example, lifting heavy objects repeatedly can lead to musculoskeletal disorders, which can be prevented by delegating such tasks to robots. This not only protects the physical well-being of workers but also allows them to focus on more complex and intellectually stimulating tasks.
Real-Time Fleet Data for Data-Driven Decision-Making
Another way in which collaborative robots enhance worker safety is by providing real-time fleet data. By collecting and analyzing data on various aspects of logistics operations, cobots enable data-driven decision-making. For example, by monitoring the performance of robots and equipment, maintenance personnel can identify patterns of wear and tear and schedule repairs or replacements accordingly. This proactive approach ensures that equipment is in optimal condition, reducing the risk of accidents caused by faulty machinery.
Furthermore, real-time fleet data allows logistics managers to monitor the movement of goods and vehicles, ensuring that they are operating within safe parameters. By tracking factors such as speed, location, and vehicle conditions, potential risks can be identified and addressed promptly. This not only protects the safety of workers but also prevents accidents that could result in damage to products or delays in delivery.
The Role of Collaborative Robots in Supply Chain Optimization
Collaborative robots play a crucial role in optimizing the supply chain, which in turn contributes to improved worker safety. By automating various aspects of logistics operations, cobots enable faster and more efficient processes. This reduces the need for workers to rush or take shortcuts, which can lead to accidents. Additionally, by minimizing errors and delays in the supply chain, cobots help create a more predictable and stable work environment, further reducing the risk of accidents or incidents.
Moreover, collaborative robots can be programmed to work in harmony with human workers, enhancing collaboration and communication. This ensures that tasks are performed in a coordinated and efficient manner, reducing the likelihood of accidents caused by miscommunication or misunderstanding. By providing clear instructions and guidance, cobots enhance worker safety by eliminating ambiguity and confusion.
The Future of Worker Safety in Logistics Automation
As logistics automation continues to evolve, the role of collaborative robots in enhancing worker safety will become even more prominent. Advancements in technology will enable robots to perform increasingly complex tasks, further reducing the reliance on manual labor. This will not only improve efficiency and productivity but also minimize the risk of accidents and injuries.
Additionally, the integration of artificial intelligence and machine learning algorithms will enable cobots to learn from their experiences and adapt to changing circumstances. This will allow them to identify potential hazards and take preventive measures autonomously, further enhancing worker safety. Furthermore, the ability of cobots to communicate and collaborate with each other will enable them to work together seamlessly, minimizing the risk of collisions or accidents caused by human error.
In Conclusion
Collaborative robots are revolutionizing the field of logistics automation, and their role in improving worker safety cannot be overstated. Through preventive maintenance, streamlined logistics, real-time fleet data, and supply chain optimization, cobots contribute to a safer and more efficient work environment. As technology continues to advance, the future looks promising for the integration of collaborative robots in logistics automation, paving the way for a safer and more productive industry.
Related Blogs
The benefits of implementing a preventive maintenance schedule for facility management
Read More