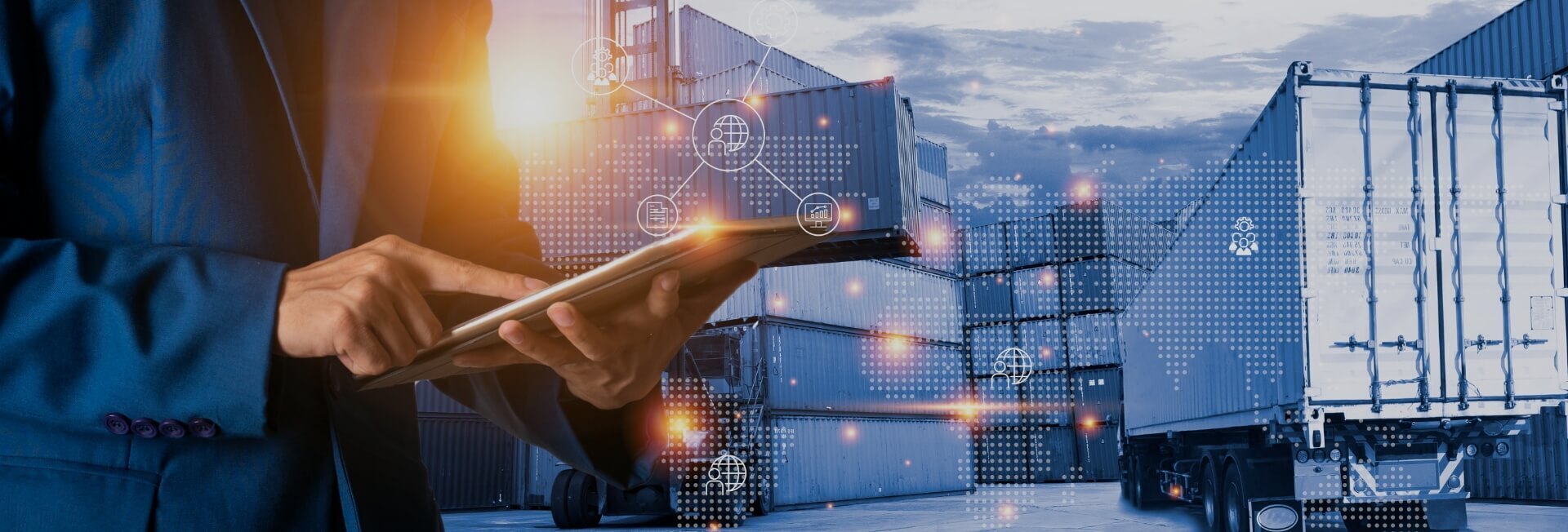
The importance of regular fluid analysis in fleet management
- Home
- Resources
- Fleet Operations and Optimization
- The importance of regular fluid analysis in fleet management
The Importance of Regular Fluid Analysis in Fleet Management
Fleet management is a complex task that involves overseeing and coordinating various aspects of a fleet of vehicles. One critical aspect of fleet management is regular fluid analysis. Fluid analysis involves monitoring the condition and performance of fluids used in vehicles, such as engine oil, coolant, transmission fluid, and hydraulic fluid. By regularly analyzing these fluids, fleet managers can identify potential issues, prevent breakdowns, and optimize the performance and efficiency of their fleet.
Preventive Maintenance and Fleet Maintenance
Preventive maintenance is a proactive approach to fleet management that focuses on preventing breakdowns and minimizing downtime. Regular fluid analysis is a key component of preventive maintenance. By analyzing the condition of fluids, fleet managers can detect early signs of wear and tear, contamination, or other issues that could lead to equipment failures. This allows them to schedule necessary repairs or replacements before a breakdown occurs, minimizing the impact on operations and reducing repair costs.
Fluid analysis is particularly important for vehicles operating in demanding conditions or high-mileage applications. These vehicles are more prone to wear and tear and require more frequent maintenance. By regularly monitoring the condition of fluids, fleet managers can ensure that these vehicles receive the necessary maintenance and repairs in a timely manner, reducing the risk of breakdowns and extending the lifespan of the vehicles.
Supply Chain Visibility and Optimization
Fluid analysis also plays a crucial role in supply chain visibility and optimization. By continuously monitoring the performance and condition of fluids, fleet managers gain actionable insights into the health of their vehicles. This data can be used to identify patterns or trends that might indicate underlying issues, such as excessive wear on certain components or the presence of contaminants in the fluids.
With this information, fleet managers can take proactive measures to address these issues, such as adjusting maintenance schedules, implementing preventive measures, or optimizing vehicle routes and operations. By addressing potential problems before they escalate, fleet managers can minimize disruptions in the supply chain, improve overall efficiency, and reduce costs.
Streamlined Logistics and Maintenance Scheduling
Regular fluid analysis also enables fleet managers to streamline logistics and maintenance scheduling. By knowing the condition of fluids in each vehicle, fleet managers can prioritize maintenance and repairs based on actual need, rather than relying on fixed schedules or arbitrary timelines.
This data-driven approach to maintenance scheduling ensures that resources are allocated more efficiently, reducing downtime and optimizing the use of manpower and equipment. By addressing maintenance needs in a timely manner, fleet managers can also minimize the risk of unexpected breakdowns or failures, improving overall fleet reliability and performance.
Fleet Maintenance Efficiency and Automation
Fluid analysis can also be integrated into fleet maintenance automation systems, further improving efficiency and reducing manual labor. By automating the process of fluid analysis, fleet managers can eliminate the need for manual data collection and analysis, reducing the risk of human error and saving valuable time and resources.
Automated fluid analysis systems can collect real-time data from vehicles, analyze it for potential issues or anomalies, and generate actionable insights or maintenance recommendations. This allows fleet managers to make informed decisions based on accurate and up-to-date information, improving the overall efficiency of fleet maintenance operations.
Conclusion
Regular fluid analysis is an essential practice in fleet management. By monitoring the condition and performance of fluids, fleet managers can detect early signs of wear and tear, prevent breakdowns, and optimize the performance and efficiency of their fleet. This proactive approach to maintenance not only reduces repair costs and downtime but also improves supply chain visibility, streamlines logistics and maintenance scheduling, and enables automation and data-driven decision-making. By investing in regular fluid analysis, fleet managers can ensure the long-term success and profitability of their fleet operations.
Related Blogs
The benefits of implementing a preventive maintenance schedule for facility management
Read More