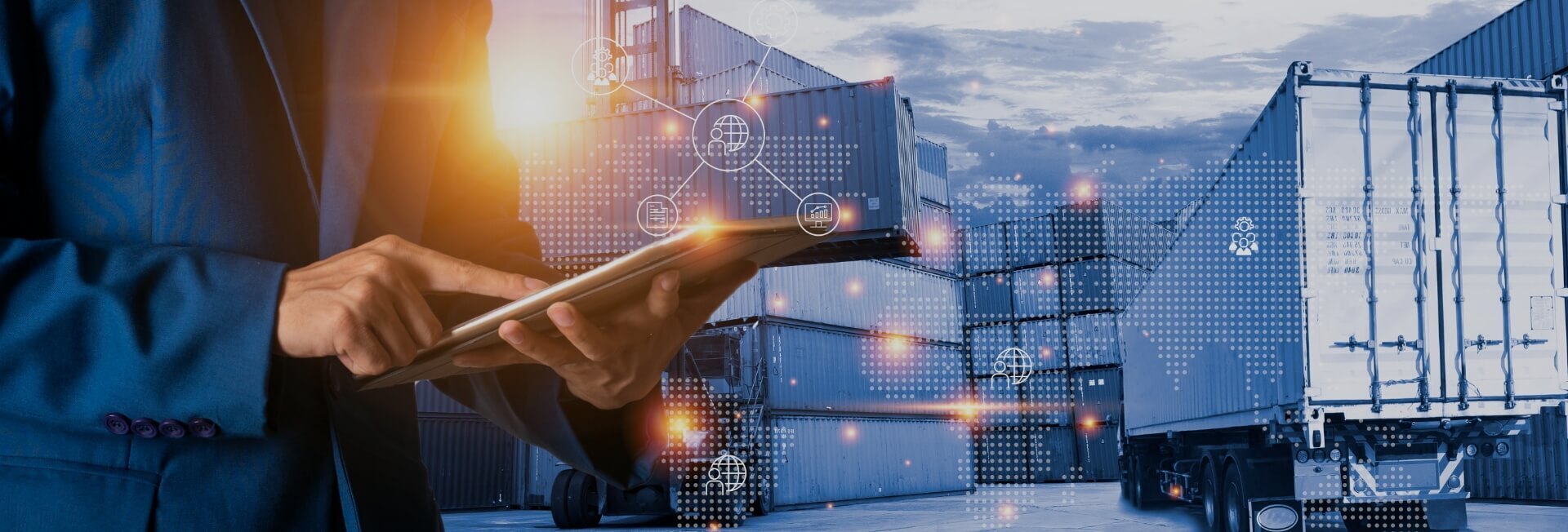
The importance of maintenance scheduling in minimizing equipment breakdowns during peak production periods
- Home
- Resources
- Fleet Operations and Optimization
- The importance of maintenance scheduling in minimizing equipment breakdowns during peak production periods
In any industry that relies on heavy equipment and machinery, equipment breakdowns can have a significant impact on productivity and profitability. This is especially true during peak production periods when every minute of downtime can result in lost revenue and missed opportunities. To minimize the risk of equipment breakdowns, companies need to prioritize maintenance scheduling and ensure that regular preventive maintenance is conducted. In this article, we will explore the importance of maintenance scheduling in minimizing equipment breakdowns during peak production periods and the key benefits it brings to the table.
Preventive Maintenance: The Key to Minimizing Equipment Breakdowns
Preventive maintenance is a proactive approach to equipment maintenance that aims to prevent breakdowns and extend the lifespan of machinery. It involves regular inspections, cleanings, lubrications, and other maintenance tasks to ensure that equipment is operating at its optimal level. By implementing a preventive maintenance program and adhering to a strict maintenance schedule, companies can identify and address potential issues before they develop into major problems.
One of the primary benefits of preventive maintenance is that it helps to identify and correct minor issues that can lead to equipment breakdowns. For example, a loose bolt or a worn-out belt may seem like minor issues, but if left unattended, they can cause significant damage to the equipment and result in costly repairs or even complete equipment failure.
Another advantage of preventive maintenance is that it helps to minimize unexpected downtime. By conducting regular inspections and addressing potential issues, companies can identify and resolve problems before they escalate and cause equipment breakdowns. This allows for planned downtime during non-peak periods when the impact on production is minimal.
Fleet Maintenance: Ensuring Optimal Performance and Efficiency
In industries that rely on a fleet of vehicles, such as logistics and transportation, fleet maintenance plays a crucial role in ensuring optimal performance and efficiency. Regular maintenance and inspections can help identify and address issues such as engine problems, tire wear, and brake system failures, which can lead to breakdowns and accidents if not properly maintained.
Fleet tracking systems and supply chain visibility solutions can further enhance fleet maintenance by providing real-time data on vehicle performance and maintenance needs. By leveraging actionable insights from these systems, companies can streamline their logistics operations and optimize their fleet maintenance scheduling. This not only reduces the risk of equipment breakdowns but also improves overall fleet efficiency and reduces operational costs.
The Importance of Maintenance Scheduling
Maintenance scheduling is the process of planning and organizing maintenance tasks to ensure that they are carried out at the right time and in the most efficient manner. It involves creating a maintenance calendar and assigning tasks to the appropriate personnel or maintenance teams. By implementing a well-structured maintenance scheduling system, companies can ensure that preventive maintenance tasks are completed on time and that equipment is properly maintained.
One of the key benefits of maintenance scheduling is that it helps to prevent equipment breakdowns during peak production periods. By scheduling preventive maintenance tasks during non-peak periods, companies can minimize the impact on production and avoid unexpected downtime. This allows for uninterrupted production during peak periods, maximizing productivity and profitability.
Maintenance scheduling also helps to optimize resource allocation and minimize costs. By planning maintenance tasks in advance, companies can allocate resources, such as manpower and spare parts, more effectively. This ensures that the necessary resources are available when needed, reducing downtime and eliminating the need for rush orders or emergency repairs, which can be costly.
The Role of Maintenance Automation in Streamlining Operations
With advancements in technology, maintenance scheduling and fleet management have become more streamlined and efficient. The use of maintenance automation tools and software allows companies to automate maintenance scheduling, track maintenance tasks, and generate comprehensive reports and analytics.
By leveraging maintenance automation, companies can benefit from real-time fleet data and actionable insights. This allows for data-driven fleet management, where decisions regarding maintenance scheduling and resource allocation are based on accurate and up-to-date information. Real-time fleet data enables companies to identify potential issues, such as equipment wear and tear or maintenance backlogs, and take proactive measures to address them before they lead to breakdowns.
Furthermore, maintenance automation helps to improve communication and collaboration among maintenance teams, reducing the risk of miscommunication and ensuring that tasks are completed on time. It also simplifies the tracking and recording of maintenance activities, making it easier to monitor compliance with maintenance schedules and regulatory requirements.
Conclusion
In conclusion, maintenance scheduling plays a crucial role in minimizing equipment breakdowns during peak production periods. By implementing a preventive maintenance program and adhering to a strict maintenance schedule, companies can identify and address potential issues before they develop into major problems. This not only reduces the risk of equipment breakdowns but also improves overall fleet efficiency and reduces operational costs.
With the help of maintenance automation tools and software, companies can further streamline their maintenance scheduling and fleet management processes. By leveraging real-time fleet data and actionable insights, companies can make data-driven decisions to optimize their maintenance schedules and resource allocation.
By prioritizing maintenance scheduling and investing in comprehensive fleet management solutions, companies can ensure that their equipment is properly maintained, and breakdowns are minimized during peak production periods. This ultimately leads to increased productivity, profitability, and customer satisfaction.
Related Blogs
The benefits of implementing a preventive maintenance schedule for facility management
Read More