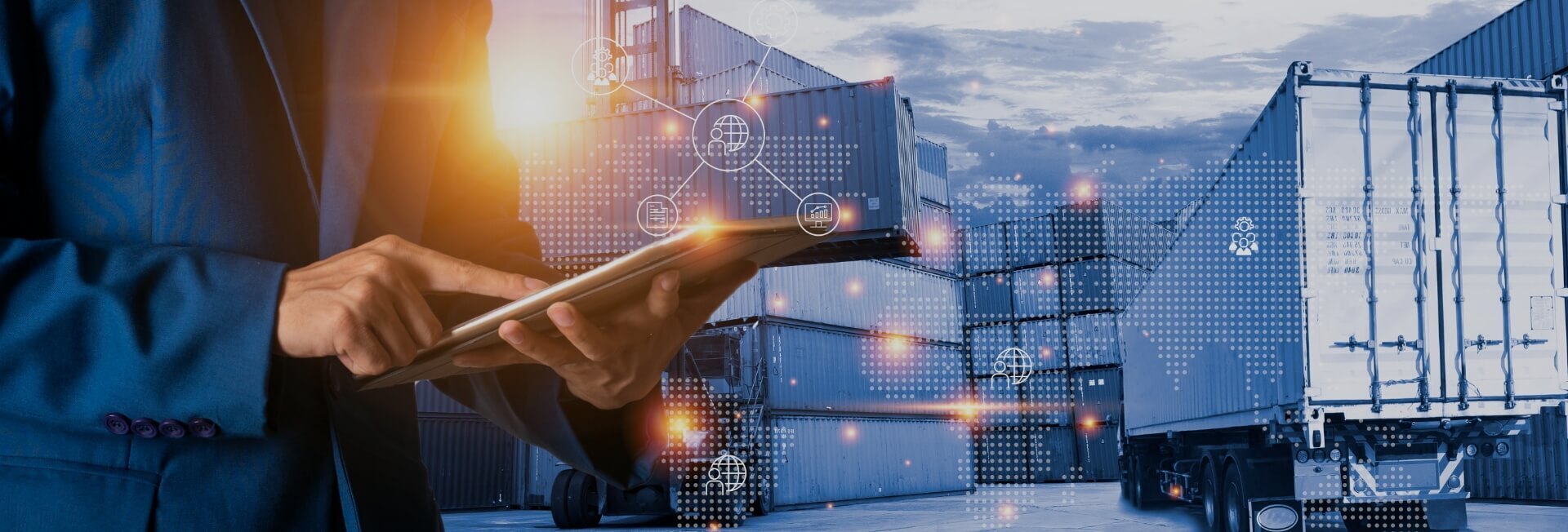
The importance of continuous improvement in logistics efficiency
- Home
- Resources
- Fleet Operations and Optimization
- The importance of continuous improvement in logistics efficiency
Enhancing Logistics Efficiency through Continuous Improvement
In today's fast-paced business environment, logistics efficiency plays a crucial role in determining the success of a company's supply chain. With increasing customer expectations and fierce competition, organizations need to continuously optimize their logistics operations to stay ahead. This article explores the importance of continuous improvement in logistics efficiency and how it can drive significant benefits for businesses.
The Benefits of Continuous Improvement in Logistics Efficiency
Continuous improvement in logistics efficiency offers several benefits to organizations, including:
1. Streamlined Operations
Continuous improvement helps identify and eliminate inefficiencies in logistics operations, leading to streamlined processes. By analyzing the entire supply chain, companies can identify bottlenecks, reduce lead times, and optimize resource allocation. This results in faster order fulfillment, improved customer satisfaction, and increased profitability.
2. Cost Savings
Efficient logistics management leads to cost savings through reduced transportation expenses, optimized inventory levels, and improved resource utilization. By continuously monitoring and analyzing data, companies can identify areas for improvement and implement cost-saving measures. For example, preventive maintenance and fleet optimization can help minimize vehicle breakdowns and repair costs.
3. Enhanced Supply Chain Visibility
Continuous improvement enables organizations to gain better visibility into their supply chain. By leveraging advanced technologies such as fleet tracking and supply chain visibility solutions, companies can track their assets in real-time and make data-driven decisions. This visibility allows for proactive management of potential disruptions and enables faster response times to customer demands.
4. Actionable Insights for Decision-Making
Continuous improvement generates actionable insights that drive informed decision-making. By analyzing data from various sources, including fleet maintenance records, inventory levels, and customer feedback, companies can identify patterns and trends. These insights help in making informed decisions to optimize logistics operations, improve customer service, and drive business growth.
Implementing Continuous Improvement in Logistics Efficiency
To effectively implement continuous improvement in logistics efficiency, organizations can follow these steps:
1. Set Clear Goals and Objectives
Start by setting clear goals and objectives for improving logistics efficiency. These goals should be specific, measurable, achievable, relevant, and time-bound (SMART). For example, a goal could be to reduce order lead time by 20% within six months. Clear goals provide direction and help in measuring progress.
2. Collect and Analyze Data
Data collection and analysis are crucial for identifying areas of improvement. Companies should gather data from various sources, such as fleet tracking systems, maintenance records, and customer feedback. Analyzing this data helps in identifying bottlenecks, inefficiencies, and opportunities for optimization.
3. Implement Automation and Technology Solutions
Automation and technology solutions play a vital role in enhancing logistics efficiency. Implementing fleet maintenance automation, logistics automation, and supply chain optimization software can streamline operations, improve visibility, and enable real-time decision-making. These solutions provide actionable insights and help in automating repetitive tasks.
4. Establish a Culture of Continuous Improvement
A culture of continuous improvement is essential for sustained success. Organizations should encourage employees to identify and propose improvements, provide training and resources for skill development, and recognize and reward innovative ideas. Continuous improvement should be ingrained in the company's values and embraced at all levels.
5. Monitor and Evaluate Progress
Regular monitoring and evaluation are necessary to ensure the effectiveness of continuous improvement efforts. Key performance indicators (KPIs) should be established and tracked to measure progress towards the set goals. This allows companies to identify areas that require further improvement and make adjustments accordingly.
Case Study: XYZ Company
XYZ Company, a leading logistics provider, implemented a continuous improvement program to enhance its logistics efficiency. By leveraging fleet tracking, supply chain visibility, and maintenance automation solutions, XYZ Company was able to achieve remarkable results. The company experienced a 30% reduction in transportation costs, a 20% improvement in order fulfillment time, and a 15% increase in customer satisfaction.
XYZ Company's success can be attributed to its proactive approach to continuous improvement. By consistently monitoring and analyzing data, implementing automated solutions, and fostering a culture of innovation, XYZ Company was able to optimize its logistics operations and gain a competitive edge.
Conclusion
In today's highly competitive business landscape, continuous improvement in logistics efficiency is crucial for organizations to stay ahead. By streamlining operations, reducing costs, enhancing supply chain visibility, and generating actionable insights, companies can drive significant benefits. Implementing automation and technology solutions, establishing a culture of continuous improvement, and monitoring progress are key steps towards achieving logistics excellence. Embracing continuous improvement empowers organizations to make data-driven decisions, meet customer expectations, and thrive in a rapidly evolving market.
Related Blogs
The benefits of implementing a preventive maintenance schedule for facility management
Read More