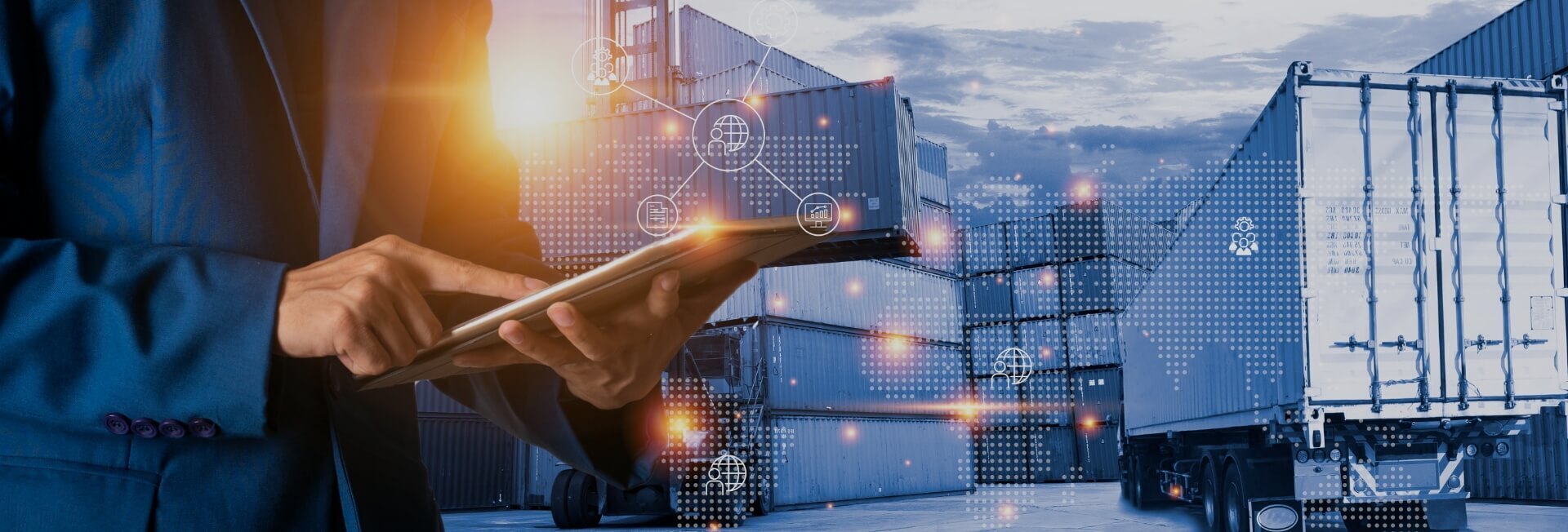
The impact of preventive maintenance scheduling on equipment reliability
- Home
- Resources
- Fleet Operations and Optimization
- The impact of preventive maintenance scheduling on equipment reliability
The Importance of Preventive Maintenance Scheduling for Equipment Reliability
In the world of fleet maintenance and logistics, ensuring equipment reliability is crucial for efficient operations. The ability to deliver goods on time and in optimal condition is essential for businesses to thrive in today's competitive market. One key factor that significantly impacts equipment reliability is preventive maintenance scheduling. By implementing a proactive maintenance strategy, businesses can minimize downtime, reduce repair costs, and extend the lifespan of their equipment.
Preventive Maintenance: A Strategic Approach
Preventive maintenance is a systematic approach to equipment maintenance that involves performing regular inspections, servicing, and repairs to prevent breakdowns and potential failures. Unlike reactive maintenance, which focuses on repairing equipment after it has already malfunctioned, preventive maintenance aims to identify and address issues before they escalate.
By implementing a preventive maintenance schedule, businesses can proactively address potential problems, such as worn-out parts, fluid leaks, or electrical issues. This proactive approach not only minimizes the risk of unexpected breakdowns but also helps prevent more extensive damage that could result in costly repairs or even the need for equipment replacement.
The Benefits of Preventive Maintenance Scheduling
Implementing a preventive maintenance schedule offers several benefits for businesses, including:
1. Improved Equipment Reliability
Regular maintenance ensures that equipment is in optimal condition, reducing the likelihood of unexpected breakdowns. By addressing potential issues early on, businesses can prevent minor problems from escalating into major failures. This ultimately improves equipment reliability and minimizes downtime, allowing for smoother operations and increased productivity.
2. Extended Equipment Lifespan
Proper maintenance and timely repairs can significantly extend the lifespan of equipment. By regularly inspecting and servicing machinery, businesses can identify and address wear-and-tear issues before they cause irreparable damage. This not only saves businesses money on premature equipment replacements but also maximizes the return on investment for their assets.
3. Cost Savings
Preventive maintenance can help businesses save money in the long run. By addressing minor issues early on, businesses can avoid costly repairs or major equipment failures that result in expensive downtime. Additionally, regular maintenance ensures that equipment operates at optimal efficiency, reducing energy consumption and potentially lowering utility costs.
4. Increased Safety
Regular maintenance not only improves equipment reliability but also contributes to a safer working environment. By identifying and addressing potential safety hazards, such as faulty wiring or worn-out parts, businesses can reduce the risk of accidents and injuries. This is particularly important in industries where employees work with heavy machinery or operate vehicles.
Implementing an Effective Preventive Maintenance Schedule
To reap the benefits of preventive maintenance, businesses need to implement an effective scheduling strategy. Here are some key steps to consider:
1. Create a Maintenance Plan
Start by creating a comprehensive maintenance plan that outlines the specific tasks, intervals, and responsibilities for each piece of equipment. This plan should be based on manufacturer recommendations, industry best practices, and the specific needs of your business. Consider factors such as usage patterns, environmental conditions, and equipment age when determining the frequency and scope of maintenance tasks.
2. Utilize Fleet Tracking and Maintenance Software
Fleet tracking and maintenance software can greatly simplify the preventive maintenance process. These tools provide real-time fleet data and actionable insights, allowing businesses to monitor equipment performance, track maintenance tasks, and schedule repairs efficiently. By automating maintenance scheduling and streamlining logistics, businesses can optimize fleet maintenance efficiency and reduce administrative overhead.
3. Train and Educate Staff
Properly trained staff plays a crucial role in implementing an effective preventive maintenance schedule. Ensure that your maintenance team is trained on equipment inspection techniques, maintenance procedures, and safety protocols. Regularly provide updates and training sessions to keep them up-to-date with the latest industry standards and best practices.
4. Regularly Evaluate and Adjust
Maintenance needs may change over time due to factors such as equipment usage, technological advancements, or business growth. Regularly evaluate your preventive maintenance schedule to ensure it remains effective and relevant. Consider feedback from your maintenance team, track equipment performance metrics, and make adjustments as necessary to optimize your maintenance strategy.
The Role of Technology in Preventive Maintenance
Advancements in technology have revolutionized the preventive maintenance landscape. Utilizing fleet management systems and IoT (Internet of Things) devices, businesses can collect real-time data on equipment performance, track usage patterns, and predict maintenance needs accurately. This data-driven approach enables businesses to make informed decisions, streamline maintenance operations, and optimize equipment reliability.
By integrating fleet tracking and maintenance software into their operations, businesses can automate maintenance scheduling, receive real-time alerts for potential issues, and ensure timely repairs. This level of automation and real-time visibility allows for proactive decision-making and efficient resource allocation, ultimately improving overall fleet and equipment performance.
Conclusion
In conclusion, preventive maintenance scheduling plays a vital role in ensuring equipment reliability and optimizing fleet performance. By implementing a proactive maintenance strategy, businesses can minimize downtime, reduce repair costs, and extend the lifespan of their equipment. Utilizing fleet tracking and maintenance software, training and educating staff, and regularly evaluating and adjusting the maintenance schedule are key steps towards effective preventive maintenance. Embracing technology and data-driven fleet management enables businesses to make informed decisions, streamline operations, and achieve optimal equipment reliability in today's fast-paced logistics industry.
Related Blogs
The benefits of implementing a preventive maintenance schedule for facility management
Read More