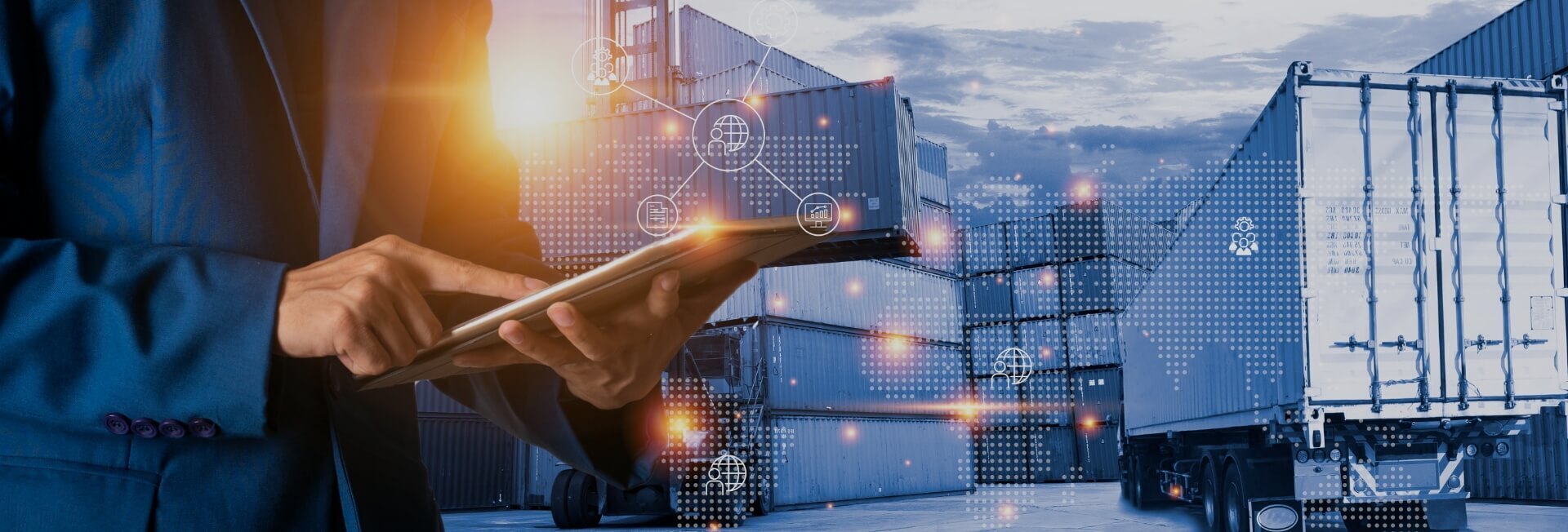
The impact of preventive maintenance on the performance of printing and packaging machinery.
- Home
- Resources
- Fleet Operations and Optimization
- The impact of preventive maintenance on the performance of printing and packaging machinery.
The Role of Preventive Maintenance in Printing and Packaging Machinery
In the fast-paced world of printing and packaging, machinery plays a crucial role in ensuring efficient production and timely delivery of goods. However, like any other type of equipment, printing and packaging machinery is prone to wear and tear over time. To ensure optimal performance and avoid unexpected breakdowns, preventive maintenance is essential. In this article, we will explore the impact of preventive maintenance on the performance of printing and packaging machinery, and why it should be an integral part of any business's maintenance strategy.
The Benefits of Preventive Maintenance
Preventive maintenance involves regular inspections, cleaning, and servicing of machinery to identify and address potential issues before they escalate into major problems. By implementing a preventive maintenance program, businesses can reap several benefits, including:
1. Increased Reliability: Regular maintenance helps identify and fix minor issues that can lead to unexpected breakdowns. This ensures that the machinery operates reliably, minimizing production downtime and associated costs.
2. Extended Lifespan: Proper maintenance can significantly extend the lifespan of printing and packaging machinery. By addressing wear and tear promptly, businesses can avoid premature equipment failure and the need for costly replacements.
3. Improved Performance: Preventive maintenance optimizes the performance of printing and packaging machinery. Regular cleaning, lubrication, and calibration ensure that the equipment operates at its peak efficiency, resulting in high-quality output and reduced waste.
4. Cost Savings: While preventive maintenance requires an investment of time and resources, it can lead to significant cost savings in the long run. By preventing major breakdowns and minimizing the need for emergency repairs, businesses can avoid expensive downtime and reduce overall maintenance costs.
Implementing an Effective Preventive Maintenance Program
To harness the benefits of preventive maintenance, businesses should establish a comprehensive program tailored to the specific needs of their printing and packaging machinery. Here are some key steps to consider:
1. Create a Maintenance Schedule: Develop a schedule that outlines the frequency and type of maintenance tasks required for each piece of machinery. This schedule should be based on manufacturer recommendations, industry best practices, and the specific operating conditions of the equipment.
2. Conduct Regular Inspections: Regularly inspect the machinery for signs of wear, damage, or malfunction. This includes checking for loose or worn-out parts, leaks, unusual noises, and abnormal vibrations. By identifying potential issues early on, businesses can take proactive measures to prevent further damage.
3. Perform Routine Cleaning and Lubrication: Dust, debris, and excessive friction can significantly impact the performance of printing and packaging machinery. Regular cleaning and lubrication of moving parts are essential to prevent premature wear and ensure smooth operation.
4. Train and Educate Staff: Properly trained operators can play a vital role in preventive maintenance. Provide comprehensive training to your staff on how to operate and maintain the machinery correctly. Encourage them to report any issues or abnormalities they observe during their daily tasks.
The Role of Technology in Preventive Maintenance
In today's digital age, technology has revolutionized the way businesses approach preventive maintenance. The advent of fleet tracking systems, supply chain visibility tools, and data-driven analytics has made it easier than ever to monitor and manage printing and packaging machinery. Here are some ways technology can enhance preventive maintenance practices:
1. Real-Time Fleet Data: Fleet tracking systems provide real-time data on the performance and condition of printing and packaging machinery. This data allows businesses to identify potential issues, track maintenance activities, and make data-driven decisions to optimize performance and efficiency.
2. Predictive Analytics: By analyzing historical data and patterns, predictive analytics can anticipate when maintenance is likely to be required. This enables businesses to schedule maintenance activities proactively, minimizing unplanned downtime and maximizing productivity.
3. Remote Monitoring: Remote monitoring technology allows businesses to track the performance and health of printing and packaging machinery from anywhere. This enables timely identification and resolution of issues, even without physical presence at the site.
4. Automation: Automation tools can streamline maintenance scheduling, work order generation, and parts inventory management. By automating these tasks, businesses can improve efficiency, reduce human errors, and ensure timely execution of maintenance activities.
Conclusion
Preventive maintenance is a critical aspect of maintaining the performance and reliability of printing and packaging machinery. By implementing a comprehensive preventive maintenance program and leveraging technology, businesses can optimize productivity, reduce costs, and extend the lifespan of their equipment. Investing in preventive maintenance today can lead to significant long-term benefits and ensure smooth operations in the competitive printing and packaging industry.
Related Blogs
The benefits of implementing a preventive maintenance schedule for facility management
Read More