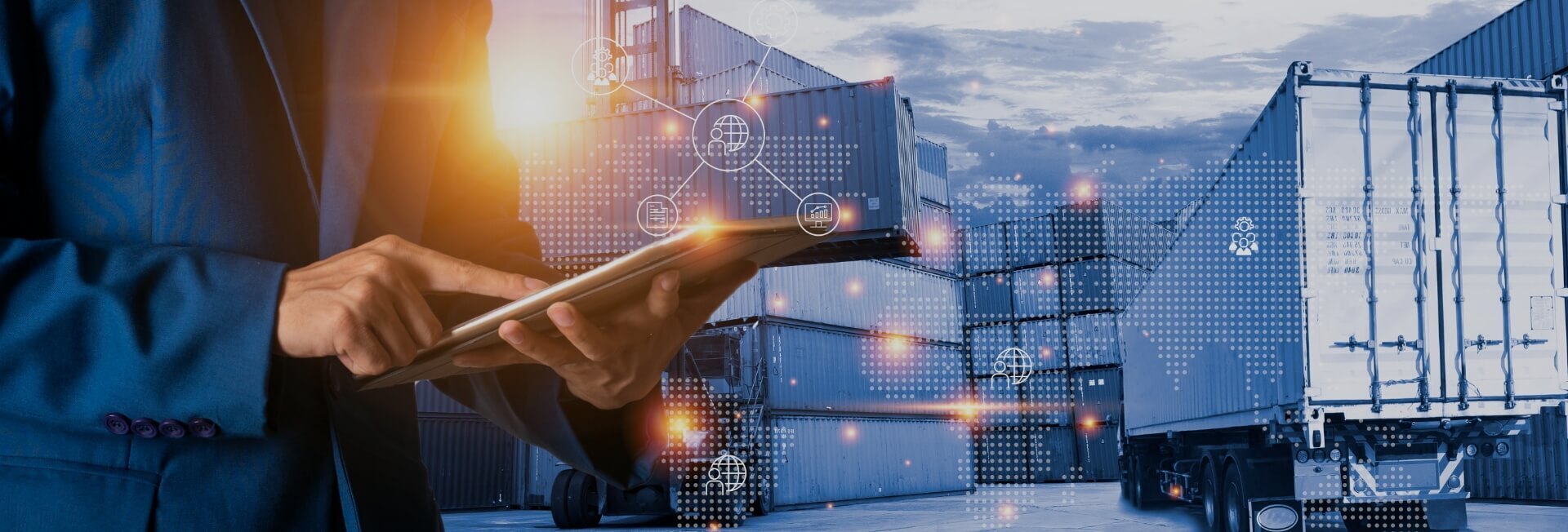
The impact of preventive maintenance on the performance of manufacturing robots
- Home
- Resources
- Fleet Operations and Optimization
- The impact of preventive maintenance on the performance of manufacturing robots
The Impact of Preventive Maintenance on the Performance of Manufacturing Robots
Manufacturing robots play a crucial role in the efficiency and productivity of modern industries. These advanced machines are responsible for performing various tasks, from assembly to packaging, with precision and speed. However, like any other equipment, robots require regular maintenance to ensure optimal performance and longevity. In this article, we will explore the importance of preventive maintenance for manufacturing robots and its impact on overall operations.
What is Preventive Maintenance?
Preventive maintenance refers to the systematic inspection, cleaning, and repair of equipment or machines to prevent breakdowns and minimize unplanned downtime. Unlike reactive maintenance, which involves fixing a problem after it occurs, preventive maintenance focuses on anticipating and preventing potential issues. By adhering to a maintenance schedule and conducting routine checks, manufacturers can identify and address any emerging problems before they escalate.
The Benefits of Preventive Maintenance for Manufacturing Robots
Implementing a preventive maintenance program for manufacturing robots offers several key benefits:
1. Increased Reliability and Reduced Downtime
Regular maintenance ensures that robots are operating at their optimal condition, reducing the risk of unexpected breakdowns. By conducting routine inspections and addressing minor issues promptly, manufacturers can prevent major malfunctions that could lead to costly downtime. This proactive approach to maintenance increases the reliability of manufacturing robots, allowing them to operate efficiently and consistently.
2. Extended Lifespan of Robots
Manufacturing robots are a significant investment for any company. By implementing preventive maintenance measures, businesses can protect their investment and extend the lifespan of their robots. Regular cleaning, lubrication, and part replacements help prevent wear and tear, ensuring that robots continue to perform at their best for years to come.
3. Improved Safety
Regular maintenance not only improves the performance of manufacturing robots but also enhances safety in the workplace. By conducting thorough inspections and addressing any potential safety hazards, manufacturers can create a safer working environment for their employees. This proactive approach helps prevent accidents and injuries, reducing the risk of costly legal issues and damage to the company's reputation.
4. Cost Savings
While preventive maintenance requires an upfront investment, it ultimately leads to significant cost savings in the long run. By preventing major breakdowns and reducing unplanned downtime, manufacturers can avoid expensive repairs and production losses. Additionally, regular maintenance helps identify and address minor issues before they become major problems, saving businesses from costly repairs or even the need to replace an entire robot.
Implementing an Effective Preventive Maintenance Program
To reap the benefits of preventive maintenance for manufacturing robots, companies should follow these key steps:
1. Create a Maintenance Schedule
Start by developing a comprehensive maintenance schedule that outlines the tasks and frequency of inspections. Consider the manufacturer's recommendations and industry best practices when determining the appropriate maintenance intervals. A well-planned schedule ensures that robots receive regular maintenance without disrupting production schedules.
2. Conduct Regular Inspections
Regular inspections are essential to identify any potential issues early on. Inspect robots for signs of wear and tear, loose connections, and abnormal noises. Pay attention to critical components such as sensors, actuators, and motors. If any issues are discovered, address them immediately to prevent further damage or performance issues.
3. Clean and Lubricate
Cleaning and lubrication are vital for maintaining the performance and longevity of manufacturing robots. Remove any dust, debris, or contaminants that could affect the robot's operation. Lubricate moving parts as recommended by the manufacturer to minimize friction and ensure smooth operation.
4. Train Maintenance Staff
Properly trained maintenance staff is crucial for implementing an effective preventive maintenance program. Ensure that technicians are knowledgeable about the specific requirements of the robots in use and have the necessary skills to perform maintenance tasks. Ongoing training and education should be provided to keep maintenance staff up to date with the latest technologies and best practices.
5. Utilize Technology for Maintenance Tracking
Modern technology offers various tools and software solutions for tracking and managing preventive maintenance tasks. Utilize fleet tracking systems or maintenance management software to streamline maintenance scheduling, track maintenance history, and generate maintenance reports. These tools provide actionable insights and help optimize maintenance operations.
The Future of Preventive Maintenance for Manufacturing Robots
As technology continues to advance, the future of preventive maintenance for manufacturing robots looks promising. With the advent of artificial intelligence (AI) and the Internet of Things (IoT), robots can now collect and analyze real-time data about their own performance and maintenance needs. This allows for predictive maintenance, where robots can anticipate maintenance requirements and schedule maintenance activities autonomously. Predictive maintenance reduces the risk of unexpected breakdowns and further optimizes robot performance.
In conclusion, preventive maintenance is essential for maximizing the performance, reliability, and lifespan of manufacturing robots. By implementing a proactive maintenance program, companies can minimize downtime, improve safety, and achieve cost savings. As technology evolves, the future of preventive maintenance holds even more potential for streamlining maintenance operations and optimizing robot performance.
Related Blogs
The benefits of implementing a preventive maintenance schedule for facility management
Read More