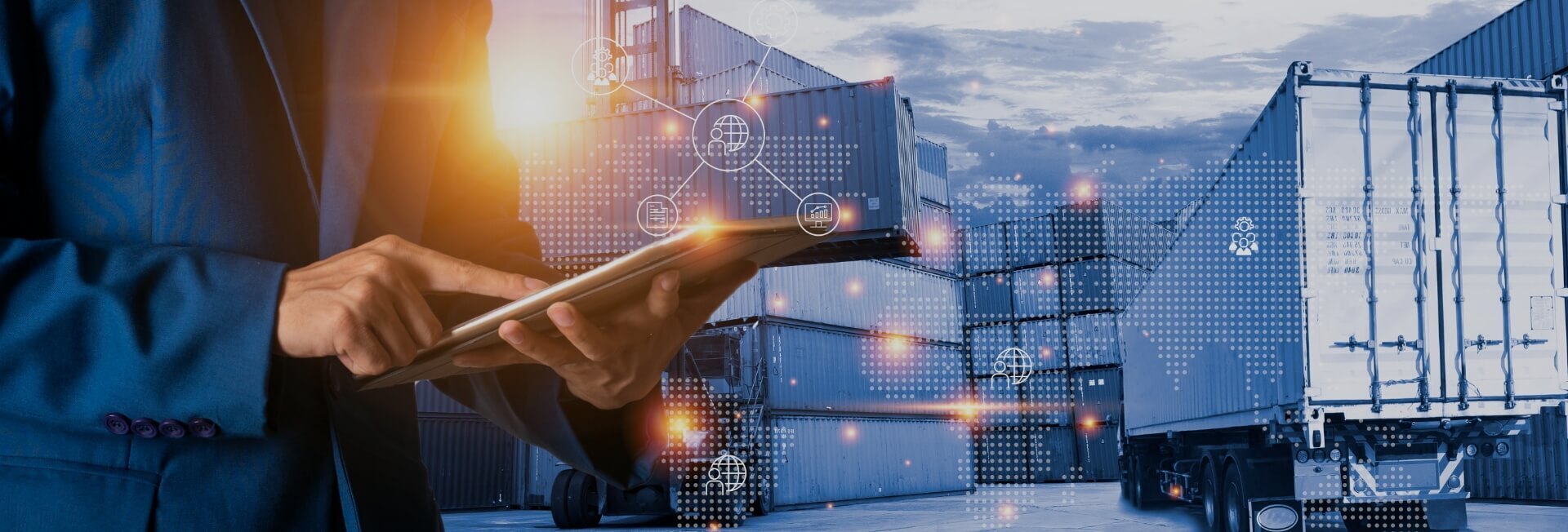
The impact of predictive maintenance scheduling on equipment performance and reliability
- Home
- Resources
- Fleet Operations and Optimization
- The impact of predictive maintenance scheduling on equipment performance and reliability
The Impact of Predictive Maintenance Scheduling on Equipment Performance and Reliability
In today's fast-paced business world, maintaining efficient and reliable equipment is crucial for the success of any organization. Whether it's a manufacturing plant, a transportation fleet, or a logistics operation, the ability to keep equipment running smoothly is essential. This is where predictive maintenance scheduling comes into play. By using advanced technology and data-driven insights, organizations can optimize their maintenance schedules, leading to improved equipment performance and reliability.
Preventive Maintenance and its Challenges
Traditionally, organizations have relied on preventive maintenance to keep their equipment in good working condition. Preventive maintenance involves performing routine maintenance tasks, such as inspections, lubrication, and component replacements, on a regular schedule. While this approach can help prevent unexpected breakdowns and extend equipment lifespan, it has its limitations.
One of the main challenges with preventive maintenance is that it is often based on fixed time intervals or predetermined usage limits. This means that maintenance tasks are performed regardless of the actual condition of the equipment. As a result, organizations may end up performing unnecessary maintenance, leading to increased costs and downtime.
Furthermore, preventive maintenance does not take into account the unique operating conditions and usage patterns of each individual piece of equipment. This can result in either over-maintenance or under-maintenance, both of which can impact equipment performance and reliability.
The Advantages of Predictive Maintenance
Predictive maintenance, on the other hand, uses real-time data and advanced analytics to determine the optimal time for maintenance activities. By monitoring key performance indicators and using algorithms to analyze historical data, organizations can predict when a piece of equipment is likely to fail or require maintenance. This enables them to schedule maintenance tasks proactively, minimizing downtime and maximizing equipment availability.
One of the main advantages of predictive maintenance is that it allows organizations to move from a reactive to a proactive maintenance approach. Instead of waiting for equipment failures to occur, organizations can take preventive action based on data-driven insights. This not only reduces the risk of unexpected breakdowns but also helps prevent more serious and costly damage to the equipment.
Another advantage of predictive maintenance is that it takes into account the actual condition and usage patterns of each individual piece of equipment. By analyzing real-time data, organizations can optimize their maintenance schedules based on the specific needs of each asset. This ensures that maintenance tasks are performed when they are actually needed, resulting in improved equipment performance and reliability.
Integration with Fleet Maintenance and Logistics Automation
Predictive maintenance scheduling goes hand in hand with fleet maintenance and logistics automation. By integrating real-time fleet data and actionable insights, organizations can optimize their maintenance schedules to improve fleet efficiency and reduce downtime.
Fleet maintenance involves the regular upkeep and repair of vehicles and equipment used in transportation and logistics operations. By implementing predictive maintenance scheduling, organizations can identify potential issues before they cause breakdowns or accidents. This helps to ensure that vehicles are in optimal condition, reducing the risk of delays and disruptions in the supply chain.
Logistics automation, on the other hand, involves the use of technology and software solutions to streamline logistics operations and optimize supply chain visibility. By integrating predictive maintenance scheduling with logistics automation, organizations can achieve comprehensive fleet management and logistics efficiency.
Real-time fleet data allows organizations to make informed decisions and take immediate action when maintenance issues arise. By leveraging this data, organizations can prioritize maintenance tasks based on their impact on overall fleet performance and reliability. This helps to ensure that resources are allocated efficiently and that maintenance activities are performed in a timely manner.
The Future of Predictive Maintenance Scheduling
As technology continues to advance, the future of predictive maintenance scheduling looks promising. The use of IoT (Internet of Things) devices and sensors allows organizations to collect even more data on equipment performance and condition. This data can then be analyzed in real-time to further optimize maintenance schedules and improve equipment reliability.
Furthermore, the integration of predictive maintenance scheduling with machine learning and artificial intelligence algorithms can enable organizations to gain even deeper insights into equipment performance. By continuously learning from historical data and identifying patterns, these algorithms can predict equipment failures with a high degree of accuracy. This allows organizations to take proactive measures to prevent downtime and optimize maintenance activities.
In conclusion, predictive maintenance scheduling has a significant impact on equipment performance and reliability. By moving from a reactive to a proactive maintenance approach, organizations can minimize downtime, reduce costs, and improve overall operational efficiency. By integrating predictive maintenance scheduling with fleet maintenance and logistics automation, organizations can achieve streamlined logistics, optimized supply chain visibility, and efficient fleet management. As technology continues to evolve, the future of predictive maintenance scheduling looks promising, with even greater potential for enhancing equipment performance and reliability.
Related Blogs
The benefits of implementing a preventive maintenance schedule for facility management
Read More