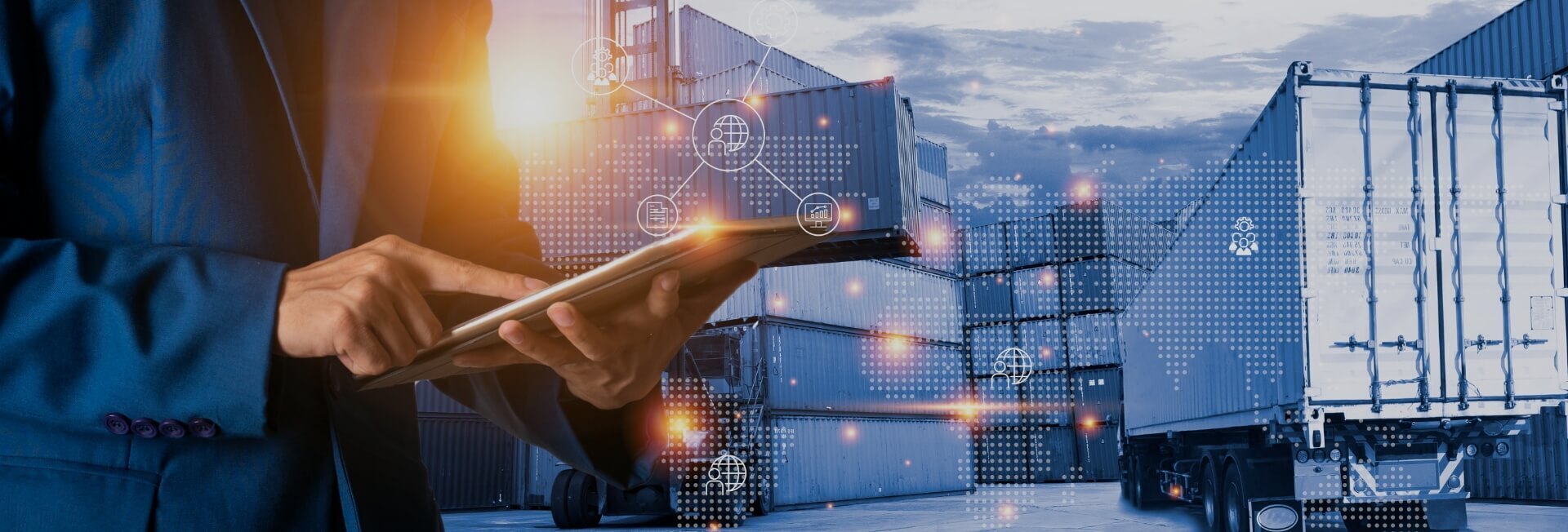
The impact of maintenance scheduling on production planning and scheduling
- Home
- Resources
- Fleet Operations and Optimization
- The impact of maintenance scheduling on production planning and scheduling
The Impact of Maintenance Scheduling on Production Planning and Scheduling
Maintenance plays a crucial role in ensuring the efficiency and reliability of production processes. In industries that heavily rely on machinery and vehicles, such as manufacturing and logistics, proper maintenance scheduling is essential for minimizing downtime, reducing costs, and maximizing productivity. This article explores the impact of maintenance scheduling on production planning and scheduling, and how technologies like preventive maintenance and fleet tracking can enhance supply chain visibility and optimize logistics.
Preventive Maintenance for Efficient Production Planning and Scheduling
Preventive maintenance involves regularly scheduled inspections, cleanings, and repairs to prevent equipment breakdowns and failures. By conducting maintenance activities at planned intervals, companies can avoid unexpected downtime and minimize the impact on production planning and scheduling.
Implementing a preventive maintenance program provides several benefits for production planning and scheduling:
- Reduced downtime: By proactively addressing potential issues, preventive maintenance reduces the risk of unexpected breakdowns that could disrupt production schedules. This ensures that production lines can operate smoothly and efficiently.
- Increased equipment lifespan: Regular maintenance helps extend the lifespan of machinery and equipment. By preventing excessive wear and tear, companies can avoid premature replacements and reduce capital expenditures.
- Improved safety: Maintenance activities also contribute to a safer working environment. Regular inspections and repairs help identify and address potential safety hazards, reducing the risk of accidents and injuries.
- Optimized maintenance resources: With a preventive maintenance program in place, companies can allocate maintenance resources more effectively. By scheduling maintenance activities in advance, they can ensure that the right personnel and resources are available when needed.
Fleet Tracking and Supply Chain Visibility
In industries like logistics, where fleets of vehicles are used to transport goods, maintenance scheduling is crucial for ensuring the smooth operation of supply chains. Fleet tracking technologies play a significant role in improving supply chain visibility and optimizing logistics processes.
Fleet tracking systems use GPS and telematics technology to monitor and track vehicles in real-time. By capturing data on vehicle location, speed, and performance, these systems provide actionable insights for efficient maintenance scheduling and logistics management.
Here's how fleet tracking enhances supply chain visibility and optimization:
- Real-time fleet data: Fleet tracking systems provide real-time data on vehicle status and performance. This data helps identify potential maintenance issues and allows companies to take proactive measures to prevent breakdowns and delays.
- Comprehensive fleet management: Fleet tracking solutions offer a centralized platform for managing and monitoring the entire fleet. This enables companies to track maintenance schedules, monitor fuel consumption, and analyze driver behavior for improved efficiency.
- Streamlined logistics: By tracking vehicle locations and performance, companies can optimize routing and scheduling, reducing delivery times and improving customer satisfaction.
- Efficient maintenance planning: Fleet tracking systems provide valuable insights into vehicle usage patterns and maintenance requirements. This data helps companies optimize maintenance schedules, ensuring that vehicles receive timely repairs and inspections without disrupting operations.
Benefits of Maintenance Scheduling for Production Planning and Scheduling
Implementing an effective maintenance scheduling strategy offers numerous benefits for production planning and scheduling:
- Improved production efficiency: Proper maintenance scheduling minimizes unplanned downtime and equipment failures, allowing production lines to operate at optimal efficiency. This ensures that production targets can be met consistently.
- Reduced maintenance costs: By conducting regular maintenance activities, companies can identify and address potential issues before they escalate into costly repairs. Preventive maintenance is often more cost-effective than reactive repairs.
- Enhanced equipment reliability: Regular maintenance helps ensure that machinery and equipment perform reliably. This reduces the risk of unexpected breakdowns and disruptions to production schedules.
- Increased customer satisfaction: By minimizing delays and maintaining consistent production output, companies can meet customer demand more effectively. This leads to higher customer satisfaction and loyalty.
- Optimized inventory management: Maintenance scheduling allows companies to plan and allocate inventory more effectively. By minimizing downtime and disruptions, they can reduce excess inventory and improve inventory turnover.
- Improved safety and compliance: Regular maintenance inspections and repairs contribute to a safer working environment and ensure compliance with safety regulations and industry standards.
Automation and Data-Driven Decision-Making for Efficient Maintenance Scheduling
Advancements in technology have paved the way for automation and data-driven decision-making in maintenance scheduling. By leveraging the power of data and analytics, companies can optimize maintenance processes and improve overall efficiency.
Here are some key technologies and strategies that enable efficient maintenance scheduling:
- Maintenance automation: Automated systems and software can streamline maintenance scheduling and workflows. These systems can generate work orders, schedule maintenance activities, and track progress, reducing manual effort and improving efficiency.
- IoT-enabled sensors: Internet of Things (IoT) sensors can be installed on machinery and equipment to collect real-time data on performance and condition. By analyzing this data, companies can identify maintenance needs and schedule repairs or replacements proactively.
- Predictive analytics: Advanced analytics algorithms can analyze historical and real-time data to predict equipment failures and maintenance requirements. By identifying patterns and trends, companies can schedule maintenance activities at optimal times, minimizing disruptions to production.
- Integration with enterprise systems: Integrating maintenance scheduling with enterprise resource planning (ERP) systems and production planning software ensures seamless coordination between maintenance activities and production schedules. This enables companies to optimize resource allocation and minimize downtime.
In conclusion, maintenance scheduling plays a critical role in production planning and scheduling. By implementing preventive maintenance programs and leveraging technologies like fleet tracking and automation, companies can enhance supply chain visibility, optimize logistics, and improve overall operational efficiency. Efficient maintenance scheduling minimizes downtime, reduces costs, and ensures reliable production output, leading to increased customer satisfaction and improved profitability.
Related Blogs
The benefits of implementing a preventive maintenance schedule for facility management
Read More