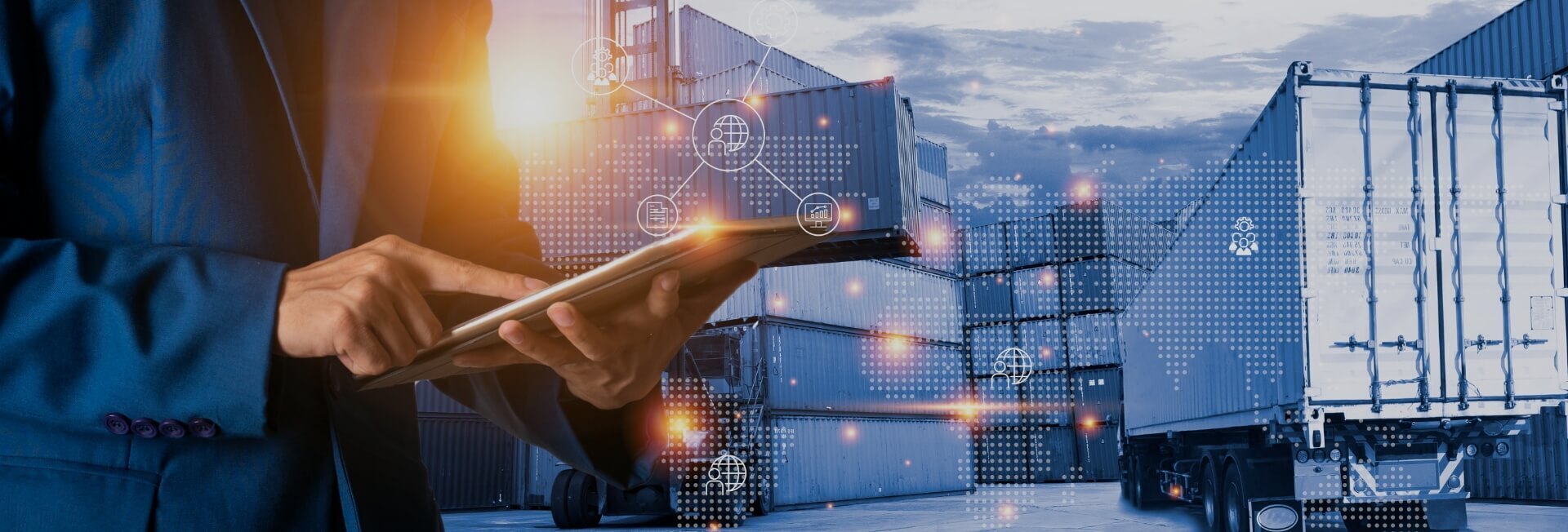
The impact of maintenance scheduling on overall plant safety and compliance with regulatory standards
- Home
- Resources
- Fleet Operations and Optimization
- The impact of maintenance scheduling on overall plant safety and compliance with regulatory standards
The Impact of Maintenance Scheduling on Plant Safety and Regulatory Compliance
Maintenance scheduling plays a crucial role in ensuring the overall safety and regulatory compliance of industrial plants. By implementing effective maintenance practices, plant operators can minimize the risk of accidents, equipment failures, and non-compliance with environmental and safety regulations. This article explores the significance of maintenance scheduling in maintaining plant safety, enhancing compliance with regulatory standards, and optimizing the efficiency of fleet management and logistics.
Preventive Maintenance for Plant Safety and Compliance
Preventive maintenance is the cornerstone of efficient plant operations, safety, and compliance. It involves regular inspections, servicing, and repairs of equipment and machinery to prevent potential failures and breakdowns. By adhering to a well-planned maintenance schedule, plant operators can identify and address issues before they escalate into safety hazards or result in non-compliance with regulatory requirements.
Implementing a preventive maintenance program not only ensures the safe and reliable operation of equipment but also helps in extending its lifespan. Regular inspections and maintenance activities allow operators to identify and address minor issues before they turn into major problems. This proactive approach reduces the risk of accidents, unplanned downtime, and costly repairs.
Furthermore, preventive maintenance plays a significant role in compliance with regulatory standards. Industrial plants are subject to various environmental, health, and safety regulations that require regular inspections, testing, and maintenance. By following a structured maintenance schedule, plant operators can ensure that their equipment and processes meet the necessary standards and guidelines, minimizing the risk of fines, penalties, and reputational damage.
The Role of Fleet Maintenance and Tracking
Fleet maintenance and tracking are essential components of plant safety, compliance, and logistics optimization. Industrial plants often rely on a fleet of vehicles for transportation, material handling, and other operational tasks. These vehicles require regular maintenance to ensure their safe and efficient operation.
By implementing a comprehensive fleet maintenance program, plant operators can track and manage the maintenance needs of their vehicles. This includes scheduling inspections, servicing, and repairs based on usage, mileage, and other parameters. Fleet maintenance automation solutions provide real-time data on the condition of vehicles, enabling operators to make data-driven maintenance decisions and prioritize repairs.
Effective fleet tracking also plays a crucial role in plant safety and compliance. By utilizing fleet tracking technologies, plant operators can monitor the location, speed, and behavior of their vehicles in real-time. This helps in enforcing safe driving practices, ensuring compliance with traffic regulations, and reducing the risk of accidents or incidents caused by reckless driving or unauthorized vehicle use.
Optimizing Logistics with Maintenance Scheduling
Maintenance scheduling not only contributes to plant safety and compliance but also plays a vital role in optimizing logistics and supply chain operations. By implementing a well-planned maintenance schedule, plant operators can minimize the risk of unexpected equipment failures or breakdowns that can disrupt production and delay shipments.
By utilizing maintenance automation solutions and fleet tracking technologies, plant operators can gain real-time insights into the condition of their equipment and vehicles. This data-driven approach enables them to make proactive decisions regarding maintenance and repairs, ensuring that their fleet is in optimal condition for transportation and material handling tasks.
Streamlined logistics and supply chain visibility are crucial for meeting customer demands and maintaining a competitive edge. By incorporating maintenance scheduling into logistics planning, plant operators can optimize the efficiency of their fleet and minimize delays. Real-time fleet data allows for better route planning, load optimization, and improved delivery schedules.
The Benefits of Data-Driven Fleet Management
Data-driven fleet management is the key to efficient logistics and maintenance scheduling. By leveraging advanced technologies and analytics, plant operators can gain actionable insights into the performance and maintenance needs of their fleet. This enables them to make informed decisions and prioritize maintenance activities based on actual data and fleet usage patterns.
Comprehensive fleet management solutions provide real-time visibility into the condition and location of vehicles, allowing for efficient maintenance planning and scheduling. With access to accurate and up-to-date information, plant operators can minimize downtime, reduce maintenance costs, and ensure compliance with regulatory requirements.
Furthermore, data-driven fleet management enables plant operators to identify trends and patterns in equipment failures, allowing for proactive measures to prevent future issues. By analyzing historical maintenance data, operators can identify common failure modes, develop preventive maintenance strategies, and optimize the lifespan of their equipment.
In Conclusion
Maintenance scheduling plays a crucial role in ensuring plant safety, compliance with regulatory standards, and optimized logistics operations. By implementing preventive maintenance practices, utilizing fleet tracking technologies, and embracing data-driven fleet management, plant operators can minimize the risk of accidents, equipment failures, and costly non-compliance issues.
Effective maintenance scheduling not only enhances safety and regulatory compliance but also improves overall operational efficiency. By proactively addressing maintenance needs and utilizing real-time fleet data, plant operators can optimize logistics, streamline operations, and meet customer demands in a timely manner.
Investing in comprehensive fleet management solutions and maintenance automation technologies is a strategic move towards efficient and compliant plant operations. By leveraging the power of preventive maintenance, fleet tracking, and data-driven decision-making, plant operators can ensure the long-term success and sustainability of their operations.
Related Blogs
The benefits of implementing a preventive maintenance schedule for facility management
Read More