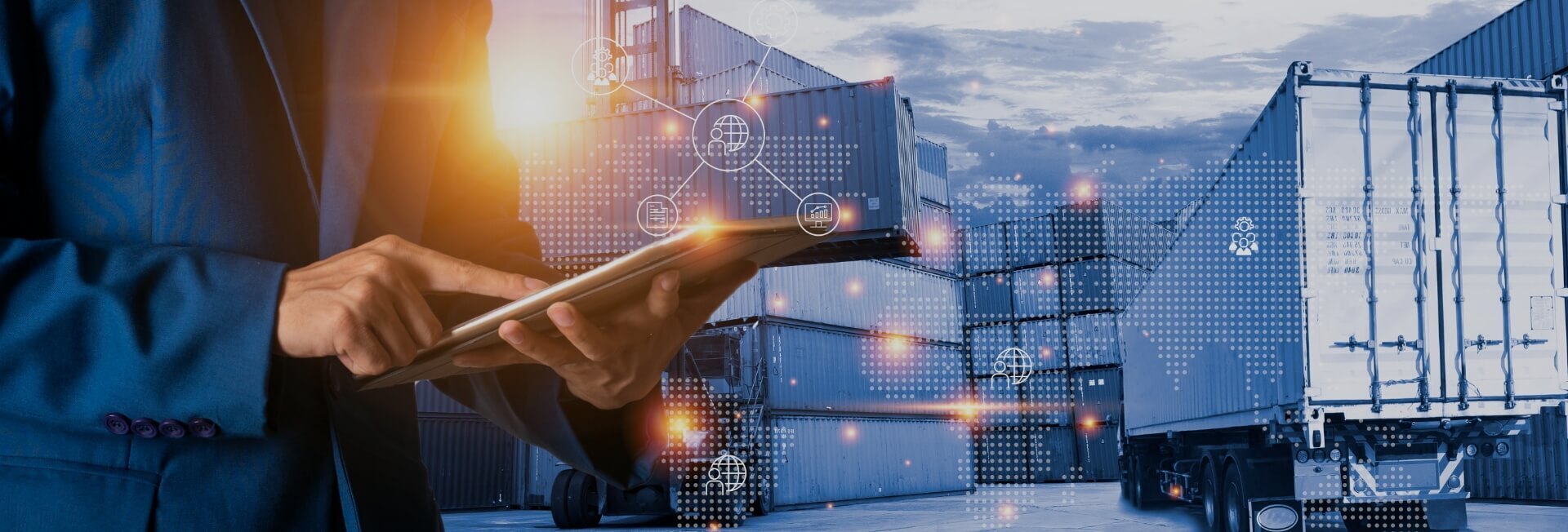
The impact of maintenance scheduling on equipment reliability and warranty claims
- Home
- Resources
- Fleet Operations and Optimization
- The impact of maintenance scheduling on equipment reliability and warranty claims
The Importance of Maintenance Scheduling for Equipment Reliability and Warranty Claims
In today's fast-paced business environment, companies rely heavily on their equipment and machinery to ensure smooth operations and maintain a competitive edge. Whether it's a fleet of vehicles, manufacturing equipment, or logistics machinery, the reliability and performance of these assets are critical to the success of any enterprise. To ensure optimal functioning and minimize downtime, proactive maintenance scheduling plays a crucial role.
Preventive Maintenance and Equipment Reliability
Preventive maintenance refers to the systematic inspection, cleaning, and replacement of components before they fail or cause a breakdown. By implementing preventive maintenance practices, businesses can identify potential issues early on and take corrective action to prevent costly breakdowns and repairs.
Regular inspections and maintenance help to identify and rectify small issues before they escalate into larger problems. By addressing these issues proactively, businesses can avoid unexpected downtime, reduce repair costs, and extend the lifespan of their equipment.
Implementing a preventive maintenance schedule ensures that maintenance tasks are performed on a regular basis, reducing the risk of equipment failure and maximizing reliability. By adhering to a well-planned maintenance schedule, businesses can minimize the chances of unexpected breakdowns and disruptions in their operations.
Reducing Warranty Claims and Costs
Proper maintenance scheduling not only improves equipment reliability but also helps reduce warranty claims and associated costs. Most equipment manufacturers provide warranties that cover repairs or replacements for a certain period. However, these warranties are subject to certain conditions, including regular maintenance as per the manufacturer's guidelines.
Failure to adhere to the recommended maintenance schedule can void the warranty, leaving businesses responsible for repair costs. By following a proactive maintenance schedule, companies can ensure compliance with warranty requirements, reducing the risk of warranty claims being rejected due to inadequate maintenance.
Additionally, regular maintenance helps identify potential issues that may be covered under warranty before they become major problems. By addressing these issues early on, businesses can take advantage of warranty coverage and avoid incurring unnecessary repair expenses.
Optimizing Fleet Maintenance Efficiency
Fleet maintenance is a critical aspect of many businesses, especially those involved in logistics and transportation. Vehicles are the lifeline of these operations, and any breakdown or downtime can have a significant impact on the overall supply chain.
Implementing an efficient maintenance scheduling system for fleets can help optimize maintenance activities, reduce breakdowns, and improve overall fleet performance. By tracking and scheduling regular maintenance tasks such as oil changes, tire rotations, and inspections, businesses can minimize the risk of unexpected breakdowns and costly repairs.
Furthermore, maintenance scheduling allows businesses to plan maintenance activities during off-peak periods, ensuring minimal disruption to daily operations. This strategic approach to fleet maintenance helps maintain a consistent level of service to customers and prevents delays in the supply chain.
Data-Driven Maintenance Scheduling for Improved Efficiency
Advancements in technology have revolutionized the way businesses approach maintenance scheduling. With the help of fleet tracking and comprehensive fleet management solutions, companies can now collect real-time data on their equipment's performance, usage, and maintenance requirements.
By leveraging this data, businesses can implement data-driven maintenance scheduling, where maintenance activities are planned based on the actual condition and usage of the equipment. This approach helps optimize maintenance resources, reduce unnecessary maintenance tasks, and focus efforts on areas that require immediate attention.
Real-time fleet data also enables businesses to identify patterns and trends in equipment performance, helping them make informed decisions regarding repairs, replacements, and upgrades. This data-driven approach to maintenance scheduling ensures that maintenance efforts are targeted, efficient, and cost-effective.
Streamlined Logistics and Supply Chain Optimization
Maintenance scheduling not only impacts the reliability of individual equipment but also plays a crucial role in optimizing the entire supply chain. By ensuring that equipment is well-maintained and in optimum condition, businesses can minimize disruptions, delays, and bottlenecks in their operations.
Efficient logistics and supply chain management rely on accurate and timely information. By implementing maintenance scheduling practices that provide real-time insights into equipment performance and maintenance requirements, businesses can make informed decisions regarding inventory management, route planning, and resource allocation.
Additionally, proactive maintenance scheduling helps prevent equipment failures and breakdowns in key areas of the supply chain, such as warehouses, distribution centers, and transportation hubs. By minimizing the risk of equipment failures, businesses can maintain a smooth flow of goods, reduce transit times, and improve customer satisfaction.
Conclusion
Maintenance scheduling plays a crucial role in ensuring the reliability and performance of equipment, as well as reducing warranty claims and associated costs. By implementing preventive maintenance practices, businesses can identify and address potential issues before they escalate, minimizing downtime and extending the lifespan of their assets.
Fleet maintenance efficiency is particularly important in logistics and transportation operations, where any breakdown or downtime can have a significant impact on the supply chain. By implementing data-driven maintenance scheduling and leveraging real-time fleet data, businesses can optimize maintenance resources, reduce unnecessary tasks, and focus efforts on areas that require immediate attention.
Furthermore, maintenance scheduling also contributes to streamlined logistics and supply chain optimization by minimizing disruptions, delays, and bottlenecks. By ensuring that equipment is well-maintained and in optimum condition, businesses can maintain a smooth flow of goods, reduce transit times, and improve overall efficiency.
In conclusion, businesses that prioritize maintenance scheduling and take a proactive approach to equipment maintenance can reap the benefits of improved reliability, reduced warranty claims, and optimized operations.
Related Blogs
The benefits of implementing a preventive maintenance schedule for facility management
Read More