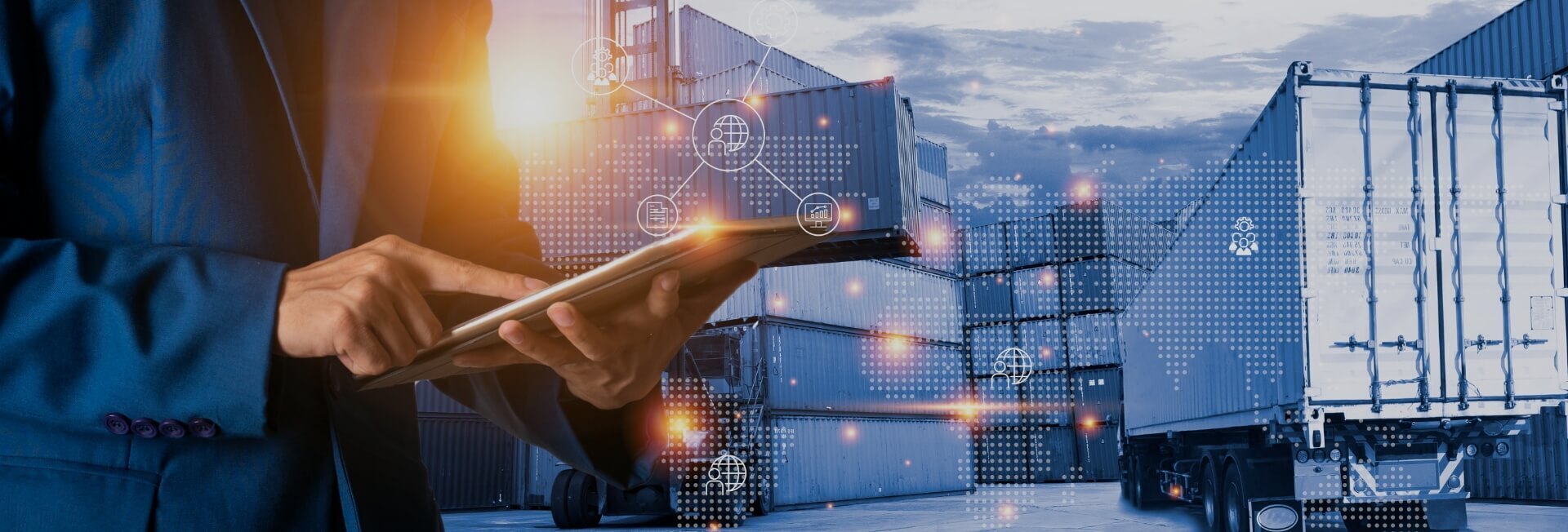
The impact of maintenance automation on maintenance planning and scheduling
- Home
- Resources
- Fleet Operations and Optimization
- The impact of maintenance automation on maintenance planning and scheduling
The Evolution of Maintenance Automation in Planning and Scheduling
Maintenance planning and scheduling are critical aspects of fleet management and supply chain operations. The ability to efficiently schedule maintenance tasks and repairs ensures that vehicles and equipment are in optimal condition, minimizing downtime and reducing costs. Traditionally, this process has been manual and time-consuming, relying on spreadsheets and paper-based systems. However, with the advent of maintenance automation, organizations can now streamline their maintenance planning and scheduling processes, leading to improved fleet maintenance efficiency and logistics optimization.
The Role of Preventive Maintenance
Preventive maintenance plays a crucial role in fleet management and maintenance planning. By regularly inspecting and servicing vehicles and equipment, organizations can identify potential issues before they become major problems, reducing the risk of breakdowns and costly repairs. Preventive maintenance is typically based on predetermined schedules, which can be time-consuming to create and manage manually.
With maintenance automation, organizations can automate the entire preventive maintenance process. Fleet tracking and monitoring systems collect real-time data on vehicle health and performance, allowing organizations to proactively schedule maintenance tasks based on actual usage and condition. By integrating fleet tracking systems with maintenance management software, organizations can automatically generate maintenance schedules, ensuring that each vehicle and piece of equipment receives the necessary maintenance at the right time.
The Benefits of Maintenance Automation
The adoption of maintenance automation brings numerous benefits to organizations, improving fleet maintenance efficiency and streamlining logistics operations. Here are some key advantages:
1. Streamlined Maintenance Scheduling
Maintenance automation enables organizations to streamline their maintenance scheduling processes. By automatically generating maintenance schedules based on real-time fleet data, organizations can ensure that maintenance tasks are scheduled in the most efficient manner possible. This not only minimizes downtime but also optimizes resource allocation, ensuring that maintenance personnel and equipment are utilized effectively.
2. Improved Fleet Maintenance Efficiency
Automation allows organizations to optimize their fleet maintenance processes, resulting in improved efficiency. By automating maintenance alerts and notifications, organizations can ensure that maintenance tasks are performed on time, reducing the risk of breakdowns and costly repairs. Real-time fleet data also allows organizations to prioritize maintenance tasks based on criticality, ensuring that vehicles and equipment essential to operations receive prompt attention.
3. Enhanced Logistics Optimization
Maintenance automation contributes to overall logistics optimization by minimizing disruptions and delays caused by unexpected breakdowns. By proactively scheduling maintenance tasks, organizations can reduce the likelihood of unexpected equipment failures, ensuring that vehicles and equipment are available when needed. This leads to improved supply chain visibility and optimization, enabling organizations to meet customer demands more efficiently.
4. Actionable Insights and Data-Driven Decision-Making
Maintenance automation provides organizations with valuable insights and data for data-driven decision-making. Real-time fleet data allows organizations to monitor the health and performance of their vehicles and equipment, identifying trends and patterns that can help optimize maintenance strategies. By leveraging this data, organizations can make informed decisions regarding preventive maintenance schedules, parts inventory management, and overall fleet optimization.
The Future of Maintenance Automation
The evolution of maintenance automation is set to continue, with advancements in technology and connectivity driving further improvements in maintenance planning and scheduling. Here are some emerging trends to watch:
1. Integration with IoT and Telematics
Integrated maintenance automation systems are increasingly incorporating Internet of Things (IoT) and telematics technology. IoT sensors can provide real-time data on various vehicle parameters, such as engine performance, fuel consumption, and tire pressure. This data can be used to predict maintenance requirements accurately, enabling organizations to proactively schedule maintenance tasks and reduce the risk of unexpected breakdowns.
2. Artificial Intelligence and Machine Learning
Artificial intelligence (AI) and machine learning (ML) algorithms are being employed to analyze vast amounts of fleet data and generate predictive maintenance models. These models can identify patterns and anomalies, allowing organizations to anticipate potential issues and take preventive actions. AI and ML can also optimize maintenance schedules based on historical data, ensuring that maintenance tasks are performed at the most opportune times.
3. Predictive Analytics for Parts Inventory Management
Predictive analytics can play a significant role in parts inventory management. By analyzing historical data on parts usage, maintenance automation systems can accurately forecast future parts requirements. This enables organizations to maintain optimal inventory levels, reducing the risk of stockouts and minimizing carrying costs.
4. Integration with Supply Chain Optimization
Maintenance automation is increasingly being integrated with supply chain optimization systems. By combining real-time fleet data with supply chain visibility tools, organizations can optimize their overall logistics operations. This integration enables organizations to make data-driven decisions regarding maintenance schedules, route planning, and inventory management, resulting in improved efficiency and customer satisfaction.
In conclusion, maintenance automation has revolutionized maintenance planning and scheduling in fleet management and supply chain operations. By automating preventive maintenance processes and leveraging real-time fleet data, organizations can improve fleet maintenance efficiency, streamline logistics operations, and make data-driven decisions. As technology continues to advance, the future of maintenance automation holds even greater potential for optimizing maintenance strategies and enhancing overall operational efficiency.
Related Blogs
The benefits of implementing a preventive maintenance schedule for facility management
Read More