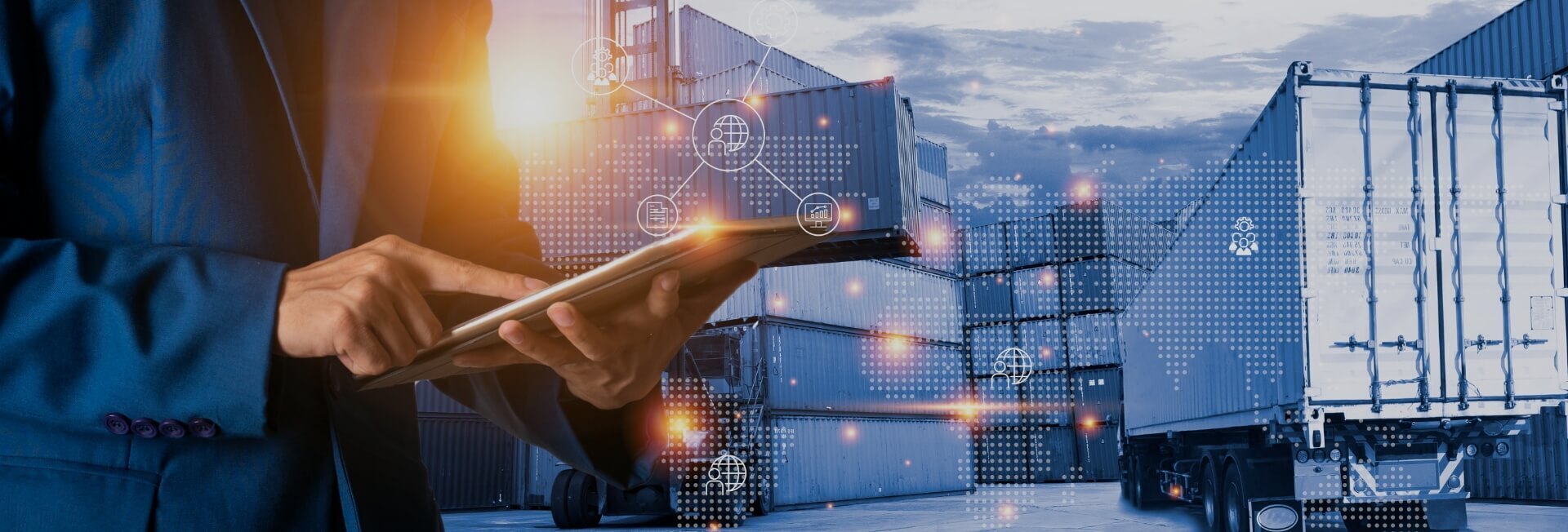
The impact of maintenance automation on industrial productivity
- Home
- Resources
- Fleet Operations and Optimization
- The impact of maintenance automation on industrial productivity
The Impact of Maintenance Automation on Industrial Productivity
In today's rapidly evolving industrial landscape, businesses are constantly seeking ways to streamline operations and improve productivity. One area where significant advancements have been made is maintenance automation. By leveraging technology and data-driven solutions, companies can optimize their maintenance processes, enhance fleet efficiency, and achieve streamlined logistics.
Preventive Maintenance: The Key to Fleet Optimization
Preventive maintenance is a crucial aspect of fleet management, as it helps identify potential issues before they turn into costly breakdowns or major repairs. By automating maintenance scheduling and implementing real-time fleet data monitoring, businesses can ensure that their vehicles are always in top condition.
With the help of fleet tracking and maintenance automation systems, companies can proactively schedule maintenance tasks based on mileage, engine hours, or specific time intervals. This proactive approach minimizes the risk of unexpected breakdowns, reduces downtime, and extends the lifespan of the fleet.
Moreover, preventive maintenance enables businesses to optimize their supply chain visibility. By having access to real-time data on the status and condition of their vehicles, companies can make data-driven decisions and ensure efficient logistics. This level of visibility allows for better planning, improved delivery times, and ultimately, enhanced customer satisfaction.
Streamlined Logistics and Supply Chain Optimization
Inefficient logistics can have a significant impact on a company's bottom line. Delays, breakdowns, and unexpected repairs can disrupt the entire supply chain and lead to increased costs and customer dissatisfaction. However, by implementing maintenance automation solutions, businesses can streamline their logistics processes and achieve greater supply chain optimization.
One of the key benefits of maintenance automation is the ability to generate actionable insights. By analyzing real-time fleet data, businesses can identify patterns, trends, and potential issues that may affect their operations. These insights can then be used to optimize logistics routes, improve fuel efficiency, and reduce maintenance costs.
Additionally, maintenance automation allows for more efficient vehicle repairs. By diagnosing and identifying issues in real-time, businesses can quickly address problems and minimize downtime. This not only keeps the fleet running smoothly but also ensures that customers receive their products on time.
The Power of Data-Driven Fleet Management
Data-driven fleet management is revolutionizing the way companies approach maintenance and operations. By harnessing the power of real-time fleet data, businesses can make informed decisions, optimize resources, and improve overall productivity.
Comprehensive fleet management solutions provide businesses with a holistic view of their operations. From monitoring fuel consumption and driver behavior to tracking maintenance schedules and vehicle performance, these solutions offer a wealth of data that can be used to drive efficiency and reduce costs.
Real-time decision-making is another significant advantage of data-driven fleet management. With access to up-to-date information on vehicle status, businesses can quickly respond to issues or make changes to their operations. Whether it's rerouting a delivery or adjusting maintenance schedules, this real-time decision-making capability enables companies to adapt to challenges and maximize productivity.
The Future of Maintenance Automation
As technology continues to advance, the future of maintenance automation looks promising. With the advent of artificial intelligence (AI) and machine learning, businesses can expect even greater efficiency and productivity gains.
AI-powered maintenance automation systems can analyze vast amounts of data and identify patterns and anomalies that humans may miss. By leveraging machine learning algorithms, these systems can continuously improve and optimize maintenance processes based on historical data and real-time inputs. This level of automation not only saves time and resources but also enables predictive maintenance, reducing the risk of unexpected breakdowns and costly repairs.
Furthermore, with the rise of the Internet of Things (IoT) and connected devices, maintenance automation can become even more advanced. IoT sensors can provide real-time data on various aspects of a vehicle, including engine performance, tire pressure, and fuel consumption. This data can be combined with other sources, such as weather conditions and traffic patterns, to generate comprehensive insights and enable proactive maintenance.
Conclusion
Maintenance automation has a profound impact on industrial productivity. By implementing preventive maintenance, streamlining logistics, and embracing data-driven fleet management, businesses can achieve greater efficiency, optimize their supply chain visibility, and make informed decisions.
Looking ahead, the future of maintenance automation holds even more promise with the integration of AI and IoT technologies. As businesses continue to leverage these advancements, they will be able to further streamline operations, reduce costs, and maximize productivity.
Related Blogs
The benefits of implementing a preventive maintenance schedule for facility management
Read More