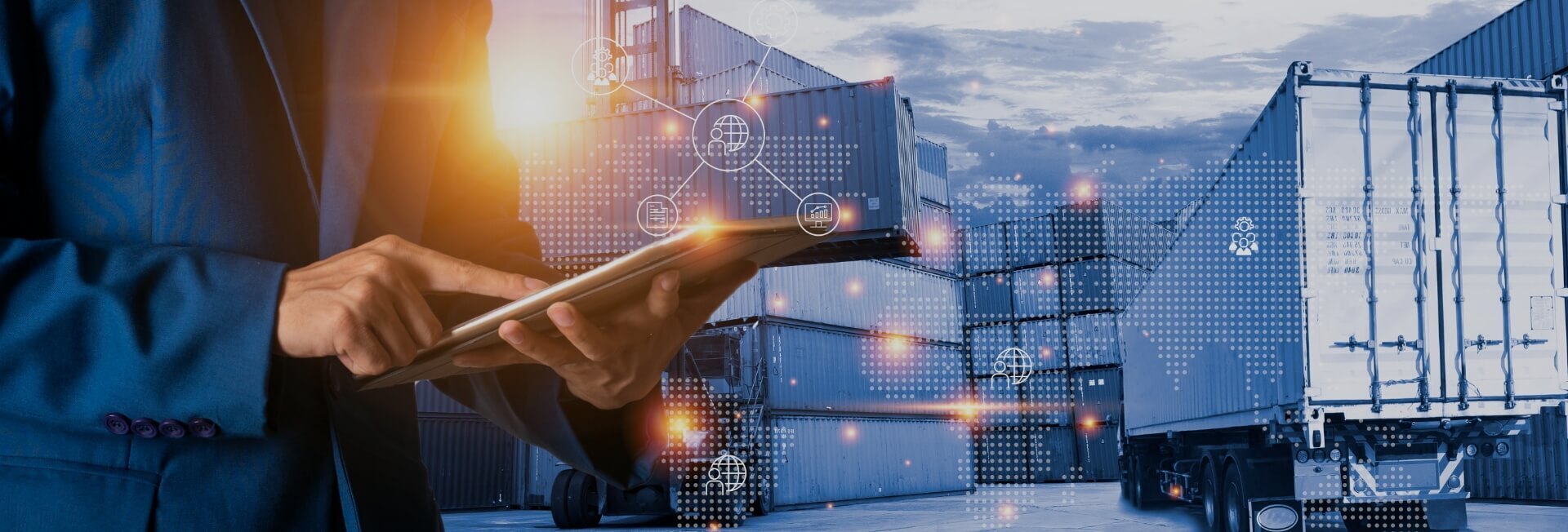
The impact of maintenance automation on equipment performance metrics
- Home
- Resources
- Fleet Operations and Optimization
- The impact of maintenance automation on equipment performance metrics
In today's fast-paced and highly competitive business landscape, organizations are constantly looking for ways to improve their operations and stay ahead of the curve. One area that holds significant potential for optimization is equipment maintenance. By implementing maintenance automation solutions, companies can not only enhance the performance of their equipment but also streamline their logistics and improve overall supply chain visibility.
Preventive Maintenance for Optimal Equipment Performance
Preventive maintenance is a proactive approach to equipment maintenance that focuses on preventing breakdowns and minimizing downtime. By regularly inspecting and servicing equipment based on predetermined schedules, organizations can identify and address potential issues before they escalate into major problems. This approach not only extends the lifespan of the equipment but also ensures optimal performance and reduces the risk of costly repairs.
With maintenance automation, organizations can take preventive maintenance to the next level. By leveraging technology such as fleet tracking and real-time data collection, companies can monitor the condition of their equipment in real-time and proactively schedule maintenance activities. This data-driven approach allows organizations to optimize their maintenance schedules, ensuring that equipment is serviced at the right time and minimizing the impact on operations.
Streamlining Logistics with Maintenance Automation
Maintenance automation goes beyond just optimizing equipment performance. It also plays a crucial role in streamlining logistics and improving overall supply chain visibility. By integrating maintenance data with other supply chain systems, organizations can gain comprehensive insights into their fleet's performance and make data-driven decisions to enhance efficiency.
For example, by combining maintenance data with fleet tracking information, organizations can identify patterns and trends in equipment performance. This allows them to identify areas for improvement and take proactive measures to address them. Additionally, by integrating maintenance scheduling with supply chain optimization tools, companies can ensure that maintenance activities are aligned with overall logistics plans, minimizing disruptions and maximizing efficiency.
The Power of Actionable Insights
One of the key benefits of maintenance automation is the ability to generate actionable insights. By collecting and analyzing data on equipment performance, organizations can identify opportunities for improvement and implement targeted strategies to enhance efficiency.
For example, by analyzing maintenance data, organizations can identify common issues and develop preventive measures to mitigate their impact. This could include implementing regular maintenance tasks, upgrading or replacing faulty components, or adjusting operational procedures. These data-driven insights enable organizations to make informed decisions that drive continuous improvement and optimize equipment performance metrics.
Real-Time Fleet Data for Efficient Decision-Making
Real-time fleet data is a game-changer when it comes to maintenance automation. By equipping equipment with sensors and leveraging IoT (Internet of Things) technology, organizations can collect real-time data on equipment performance and condition. This data can then be used to trigger maintenance alerts, schedule repairs, and provide valuable insights into equipment health.
With real-time fleet data, organizations can make proactive decisions regarding maintenance activities. For example, if a piece of equipment is showing signs of potential failure, the system can automatically generate a maintenance request and trigger an alert to the maintenance team. This allows organizations to address issues before they escalate and minimize the impact on operations.
Conclusion
Maintenance automation has a significant impact on equipment performance metrics. By implementing preventive maintenance strategies and leveraging technology such as fleet tracking and real-time data collection, organizations can optimize their supply chain visibility, streamline logistics, and make data-driven decisions to enhance efficiency. With maintenance automation, companies can stay ahead of the curve and ensure that their equipment is performing at its best, ultimately leading to improved operational performance and a competitive edge in the market.
Related Blogs
The benefits of implementing a preventive maintenance schedule for facility management
Read More