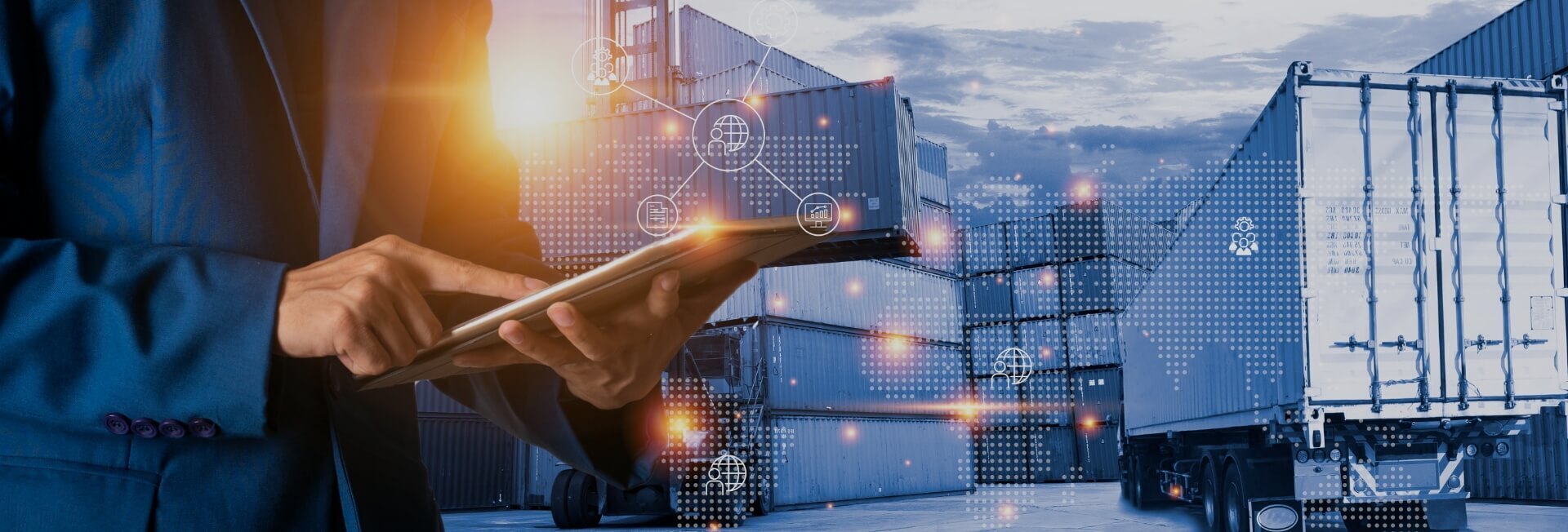
The impact of maintenance automation on equipment failure rates
- Home
- Resources
- Fleet Operations and Optimization
- The impact of maintenance automation on equipment failure rates
The Advantages of Maintenance Automation in Reducing Equipment Failure Rates
In today's fast-paced and highly competitive business environment, fleet maintenance plays a crucial role in ensuring efficient and reliable operations. Equipment failure can lead to costly repairs, unplanned downtime, and disruptions in the supply chain. To mitigate these risks, many businesses are turning to maintenance automation to optimize their fleet maintenance processes and reduce equipment failure rates.
Preventive Maintenance: A Key Component of Fleet Maintenance
Preventive maintenance is a proactive approach to maintenance that focuses on performing regular inspections, servicing, and repairs to prevent equipment breakdowns. By implementing a preventive maintenance program, businesses can identify and address potential issues before they escalate into major problems. This not only helps in reducing equipment failure rates but also extends the lifespan of the equipment, resulting in cost savings in the long run.
One of the challenges of preventive maintenance is ensuring timely and accurate maintenance scheduling. This is where maintenance automation comes into play. With the help of advanced fleet tracking and management solutions, businesses can automate maintenance scheduling based on factors such as usage, mileage, and time. This ensures that equipment is serviced and inspected at the right intervals, minimizing the risk of failure due to neglect or oversight.
The Role of Data-Driven Fleet Management in Maintenance Automation
Data-driven fleet management is at the core of maintenance automation. By leveraging real-time fleet data, businesses can gain comprehensive visibility into the health and performance of their equipment. This data includes information on fuel consumption, engine diagnostics, tire pressure, and more. By analyzing this data, businesses can identify patterns and trends that indicate potential maintenance issues.
For example, if a certain type of equipment consistently shows a higher failure rate after a certain number of hours of operation, the maintenance team can proactively schedule preventive maintenance tasks for that specific equipment before it reaches the critical threshold. This data-driven approach allows businesses to take proactive measures and address potential issues before they lead to equipment failure.
Streamlined Logistics and Improved Decision-Making
Maintenance automation not only reduces equipment failure rates but also improves overall logistics efficiency. By automating maintenance processes, businesses can streamline their operations and reduce the time and effort required to manage maintenance tasks. This frees up resources that can be allocated to other critical areas of the business, such as supply chain optimization and customer service.
Furthermore, maintenance automation provides real-time fleet data and actionable insights that enable businesses to make informed and timely decisions. For example, if a piece of equipment requires immediate repairs, the maintenance team can quickly assess the situation, prioritize the repair, and allocate resources accordingly. This real-time decision-making capability minimizes downtime and ensures that equipment is back in operation as soon as possible.
The Benefits of Maintenance Automation
Maintenance automation offers several benefits that contribute to the reduction of equipment failure rates:
- Improved Maintenance Scheduling: By automating maintenance scheduling, businesses can ensure that equipment is serviced and inspected at the right intervals, reducing the risk of failure due to neglect or oversight.
- Early Detection of Issues: Data-driven fleet management allows businesses to identify potential maintenance issues before they lead to equipment failure. This early detection enables proactive measures to be taken, minimizing downtime and costly repairs.
- Increased Equipment Lifespan: Preventive maintenance, enabled by automation, extends the lifespan of equipment by addressing potential issues before they escalate into major problems. This results in cost savings in the long run.
- Optimized Resource Allocation: By automating maintenance processes, businesses can free up resources that can be allocated to other critical areas of the business, such as supply chain optimization and customer service.
- Enhanced Decision-Making: Real-time fleet data and actionable insights enable businesses to make informed and timely decisions, minimizing downtime and ensuring efficient operations.
Conclusion
Maintenance automation plays a vital role in reducing equipment failure rates and optimizing fleet maintenance processes. By implementing preventive maintenance programs and leveraging data-driven fleet management solutions, businesses can proactively address potential issues, extend the equipment lifespan, and improve overall logistics efficiency. With the ability to make informed and timely decisions, businesses can minimize downtime, reduce costly repairs, and ensure smooth operations.
Related Blogs
The benefits of implementing a preventive maintenance schedule for facility management
Read More