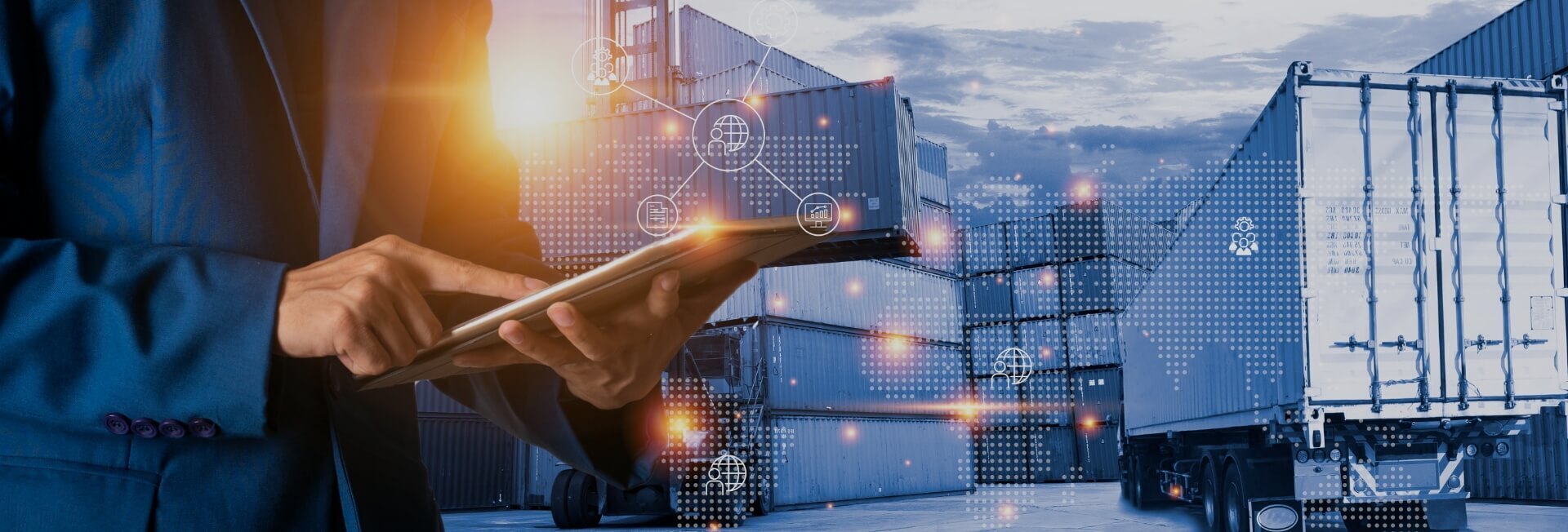
The impact of effective maintenance scheduling on overall equipment effectiveness (OEE)
- Home
- Resources
- Fleet Operations and Optimization
- The impact of effective maintenance scheduling on overall equipment effectiveness (OEE)
Introduction
In today's fast-paced business environment, it is crucial for companies to ensure the smooth operation of their fleets and equipment. Effective maintenance scheduling plays a vital role in maintaining the efficiency and reliability of these assets. By implementing a proactive approach to maintenance, companies can prevent breakdowns, minimize downtime, and optimize overall equipment effectiveness (OEE).
What is Overall Equipment Effectiveness (OEE)?
Overall Equipment Effectiveness (OEE) is a key performance indicator used to measure the productivity and efficiency of equipment and machinery. It takes into account three factors:
- Availability: The percentage of scheduled time that the equipment is available for production.
- Performance: The speed at which the equipment operates compared to its maximum designed speed.
- Quality: The number of defect-free products produced by the equipment.
By improving these three factors, companies can enhance their overall equipment effectiveness and maximize production output.
The Importance of Preventive Maintenance
Preventive maintenance is a proactive approach that involves performing regular inspections, servicing, and repairs on equipment to prevent breakdowns and extend the lifespan of assets. By implementing a preventive maintenance strategy, companies can reduce the likelihood of unexpected failures, minimize downtime, and improve overall equipment effectiveness.
Fleet maintenance is a critical aspect of preventive maintenance, especially for companies that rely on transportation for their operations. Fleet tracking and supply chain visibility are vital for maintaining the efficiency and reliability of logistics operations. By investing in comprehensive fleet management solutions, companies can optimize their supply chain, streamline logistics, and gain actionable insights through real-time fleet data.
Maintenance scheduling is a key component of preventive maintenance. It involves creating a schedule for routine inspections, servicing, and repairs based on equipment usage, manufacturer recommendations, and historical data. By adhering to a well-planned maintenance schedule, companies can ensure that their equipment operates at peak performance, minimize the risk of unexpected breakdowns, and optimize overall equipment effectiveness.
The Benefits of Effective Maintenance Scheduling
1. Minimizes Downtime: Effective maintenance scheduling helps minimize downtime by identifying and addressing potential issues before they escalate into major problems. By performing regular inspections and addressing maintenance needs proactively, companies can prevent unexpected breakdowns and keep their equipment operational.
2. Maximizes Equipment Efficiency: Regular maintenance and servicing ensure that equipment operates at its optimal efficiency. By addressing wear and tear, lubrication needs, and other maintenance requirements, companies can maximize the performance and lifespan of their equipment.
3. Reduces Repair Costs: By conducting regular maintenance, companies can identify and address minor issues before they turn into major repairs. This proactive approach helps reduce repair costs and extends the lifespan of equipment, resulting in long-term cost savings.
4. Increases Safety: Regular maintenance inspections help identify potential safety hazards and ensure that equipment meets safety standards. By addressing safety concerns promptly, companies can create a safer working environment for their employees and minimize the risk of accidents.
How to Optimize Maintenance Scheduling
1. Collect and Analyze Data: To optimize maintenance scheduling, it is essential to collect and analyze relevant data. This includes equipment usage, historical maintenance records, manufacturer recommendations, and any other relevant information. By analyzing this data, companies can identify patterns, predict maintenance needs, and optimize scheduling accordingly.
2. Prioritize Critical Equipment: Not all equipment requires the same level of maintenance. It is crucial to prioritize critical equipment that has a significant impact on production and operations. By focusing resources on the most critical assets, companies can ensure maximum uptime and minimize disruptions.
3. Implement Predictive Maintenance Techniques: Predictive maintenance involves using advanced technologies such as IoT sensors and data analytics to monitor equipment performance in real-time. By collecting and analyzing real-time data, companies can identify potential failures before they occur and schedule maintenance proactively.
4. Use Maintenance Management Software: Maintenance management software can streamline the maintenance scheduling process by automating tasks, generating work orders, and providing real-time visibility into maintenance activities. By using such software, companies can optimize their maintenance schedules and improve overall equipment effectiveness.
Conclusion
Effective maintenance scheduling is essential for optimizing overall equipment effectiveness and ensuring the smooth operation of fleets and equipment. By implementing a proactive approach to maintenance and investing in comprehensive fleet management solutions, companies can prevent breakdowns, minimize downtime, and maximize production output. With the help of maintenance automation, real-time fleet data, and data-driven decision-making, companies can achieve efficient logistics operations and gain a competitive edge in today's fast-paced business environment.
Related Blogs
The benefits of implementing a preventive maintenance schedule for facility management
Read More