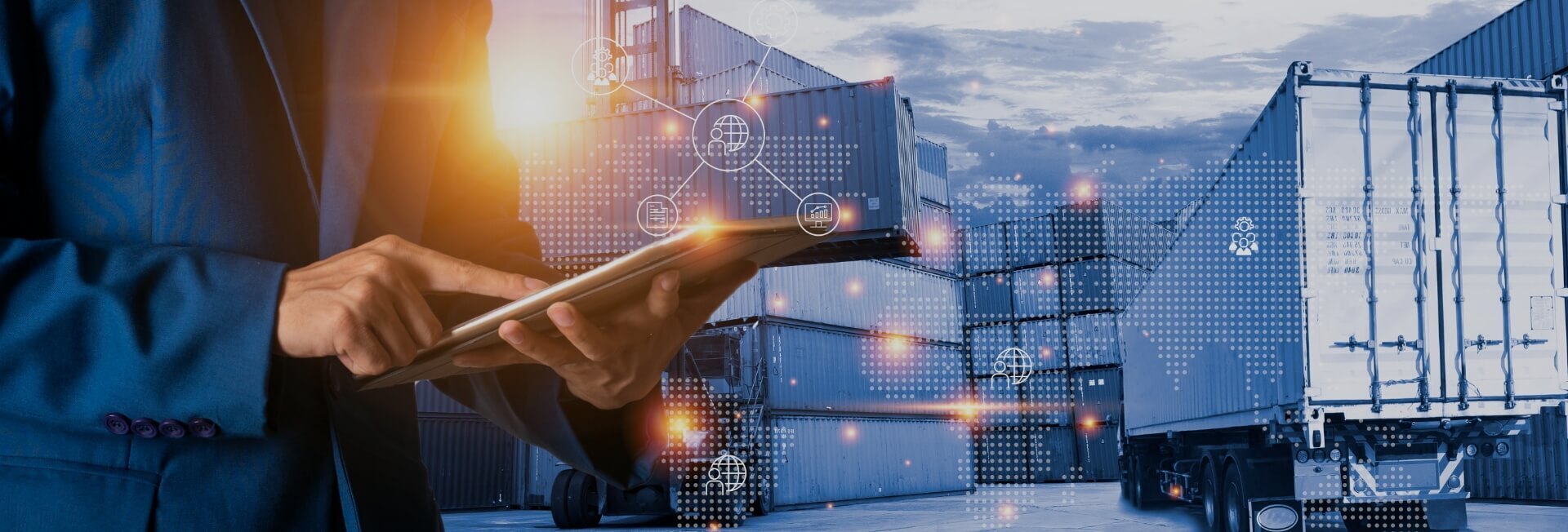
The impact of 3D printing on logistics automation
- Home
- Resources
- Fleet Operations and Optimization
- The impact of 3D printing on logistics automation
Introduction
Logistics automation has become a critical component of modern supply chain management. With the advent of new technologies, such as 3D printing, the logistics industry is undergoing a transformation like never before. 3D printing, also known as additive manufacturing, is revolutionizing the way products are designed, manufactured, and distributed. In this article, we will explore the impact of 3D printing on logistics automation and how it is reshaping the supply chain.
The Rise of 3D Printing
3D printing has gained significant traction in recent years due to its ability to create complex and customized objects on-demand. This technology uses computer-aided design (CAD) software to create a digital model, which is then converted into a physical object layer by layer. Unlike traditional manufacturing methods, 3D printing eliminates the need for molds, tooling, and assembly lines, making it more cost-effective and efficient.
Benefits of 3D Printing in Logistics Automation
Integrating 3D printing technology into logistics automation offers several benefits for fleet maintenance and supply chain management:
1. Streamlined Logistics
3D printing enables companies to produce spare parts and components on-demand, eliminating the need for large inventories and reducing lead times. This streamlines logistics by reducing the number of suppliers, transportation costs, and warehouse space required. With 3D printing, companies can produce parts locally, reducing the dependency on global supply chains and making the logistics process more efficient.
2. Enhanced Supply Chain Visibility
By integrating 3D printing technology into fleet maintenance and supply chain management, companies can gain real-time visibility into their inventory levels and demand patterns. This allows for better inventory management and more accurate demand forecasting, improving overall supply chain efficiency. With 3D printing, companies can quickly respond to changes in demand and reduce the risk of stockouts or overstocking.
3. Improved Maintenance Scheduling
3D printing technology enables companies to produce replacement parts on-demand, reducing the downtime associated with traditional maintenance processes. This allows for more efficient maintenance scheduling and faster repairs, minimizing the impact on fleet operations. With real-time fleet data and 3D printing capabilities, companies can proactively schedule maintenance based on actual usage patterns, optimizing fleet maintenance efficiency.
4. Cost Savings
Integrating 3D printing technology into logistics automation can lead to significant cost savings. By producing spare parts and components on-demand, companies can reduce inventory holding costs, eliminate the need for expedited shipping, and minimize the risk of obsolescence. Additionally, 3D printing allows for the optimization of part designs, reducing material waste and production costs. These cost savings contribute to overall fleet optimization and improved logistics efficiency.
Challenges of Implementing 3D Printing in Logistics Automation
While the benefits of integrating 3D printing technology into logistics automation are clear, there are also several challenges that need to be addressed:
1. Quality Control
Ensuring the quality and consistency of 3D printed parts can be a challenge. Companies need to establish robust quality control processes and invest in advanced inspection technologies to validate the integrity of printed parts. Implementing quality control measures is essential to maintain the reliability and safety of fleet operations.
2. Intellectual Property Protection
With the widespread use of 3D printing, there is an increased risk of intellectual property infringement. Companies need to implement effective strategies to protect their proprietary designs and prevent unauthorized replication of their products. This includes implementing encryption technologies, digital rights management systems, and legal frameworks to safeguard intellectual property rights.
3. Skill Gap
3D printing technology requires specialized skills and knowledge. Companies need to invest in training programs to equip their workforce with the necessary expertise to operate and maintain 3D printers. Bridging the skill gap is crucial to fully leverage the benefits of 3D printing in logistics automation.
4. Material Selection
Choosing the right materials for 3D printing can be challenging. Different applications require different material properties, such as strength, flexibility, and heat resistance. Companies need to carefully select materials that meet the specific requirements of their fleet maintenance and supply chain management processes. Conducting thorough material testing and evaluation is essential to ensure the suitability and performance of 3D printed parts.
Conclusion
3D printing is revolutionizing logistics automation and transforming the supply chain. By integrating 3D printing technology into fleet maintenance and supply chain management, companies can streamline logistics, enhance supply chain visibility, improve maintenance scheduling, and achieve significant cost savings. However, implementing 3D printing in logistics automation also comes with its own set of challenges, including quality control, intellectual property protection, skill gap, and material selection. Overcoming these challenges is essential to fully exploit the potential of 3D printing and drive efficient and data-driven fleet management. As the technology continues to evolve, 3D printing will undoubtedly play a crucial role in shaping the future of logistics automation.
Related Blogs
The benefits of implementing a preventive maintenance schedule for facility management
Read More