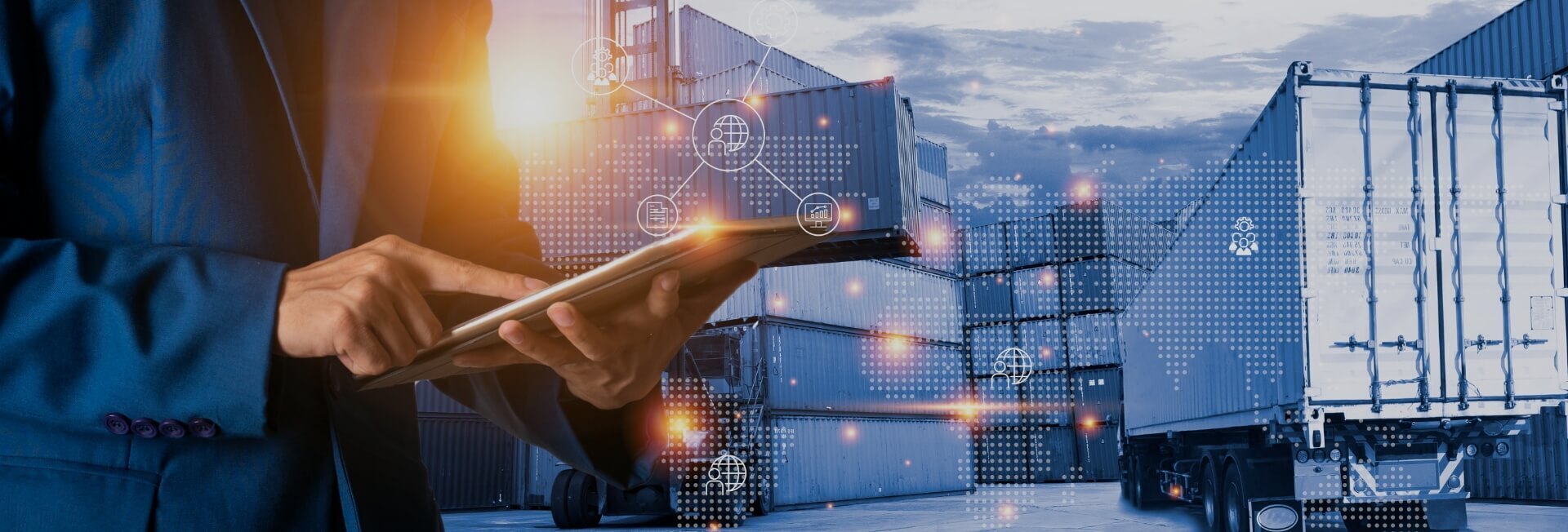
The challenges of optimizing maintenance scheduling in multi-site manufacturing operations
- Home
- Resources
- Fleet Operations and Optimization
- The challenges of optimizing maintenance scheduling in multi-site manufacturing operations
The Challenges of Optimizing Maintenance Scheduling in Multi-Site Manufacturing Operations
Preventive maintenance plays a crucial role in the efficient operation of manufacturing facilities. Regular maintenance and repairs help prevent unexpected breakdowns, reduce downtime, and ensure the longevity of equipment. However, optimizing maintenance scheduling in multi-site manufacturing operations can be a complex task. With multiple sites, diverse equipment, and varying production schedules, finding the right balance between maintenance and production can be a challenge. In this article, we will explore the challenges faced in optimizing maintenance scheduling in multi-site manufacturing operations and discuss potential solutions.
1. Fleet Maintenance and Tracking
In multi-site manufacturing operations, a fleet of vehicles is often used to transport goods and materials between sites. These vehicles are critical to the smooth functioning of the supply chain and need to be properly maintained to ensure efficient logistics. Fleet maintenance involves routine inspections, repairs, and preventive measures to keep the vehicles in optimal condition.
One of the challenges in fleet maintenance is tracking the maintenance history and scheduling future repairs. Without proper tracking, it can be difficult to identify when a vehicle needs maintenance and plan for it in advance. This can lead to unexpected breakdowns and disruptions in the supply chain.
Implementing a fleet tracking system can help address this challenge. Fleet tracking systems use GPS technology to monitor the location, speed, and performance of vehicles in real-time. By integrating maintenance data into the tracking system, maintenance schedules can be automatically generated based on mileage, engine hours, or other relevant factors. This enables proactive maintenance planning and ensures that vehicles are serviced at the right time.
2. Supply Chain Visibility and Optimization
Efficient maintenance scheduling is closely linked to supply chain visibility and optimization. In multi-site manufacturing operations, it is important to have a comprehensive understanding of the entire supply chain, from raw materials to finished products. This visibility allows for better planning and coordination of maintenance activities.
However, achieving supply chain visibility can be challenging due to the complexity of multi-site operations. Each site may have its own set of processes, systems, and data sources, making it difficult to consolidate and analyze information. Without a clear view of the supply chain, it is difficult to identify bottlenecks, optimize workflows, and schedule maintenance activities effectively.
Implementing a supply chain visibility solution can help overcome this challenge. These solutions integrate data from different sources and provide real-time insights into the entire supply chain. By analyzing data on production, inventory, and transportation, maintenance scheduling can be optimized to minimize disruptions and maximize efficiency.
3. Actionable Insights and Streamlined Logistics
Optimizing maintenance scheduling requires actionable insights and streamlined logistics. Traditional approaches to maintenance scheduling often rely on manual processes, spreadsheets, and guesswork. This can result in inefficient use of resources, missed maintenance opportunities, and increased costs.
To overcome these challenges, organizations can leverage data-driven insights and automation. By collecting and analyzing real-time fleet data, organizations can gain actionable insights into the condition of their assets and make informed decisions about maintenance scheduling. For example, predictive analytics can be used to identify patterns and trends in equipment failures, allowing for proactive maintenance before a breakdown occurs.
Furthermore, implementing a comprehensive fleet management system can streamline logistics and improve maintenance scheduling. These systems provide a centralized platform for managing maintenance activities, tracking work orders, and scheduling repairs. By automating routine tasks and providing real-time visibility into the status of maintenance activities, organizations can optimize their maintenance scheduling and improve fleet efficiency.
4. Efficient Logistics and Real-Time Decision-Making
In multi-site manufacturing operations, efficient logistics is essential for maintaining optimal production and minimizing downtime. However, coordinating logistics across multiple sites can be challenging, especially when it comes to maintenance scheduling. Delays or disruptions in transportation can have a cascading effect on production schedules and overall operational efficiency.
To address this challenge, organizations can leverage real-time data and decision-making tools. By integrating maintenance data with logistics systems, organizations can make informed decisions about scheduling maintenance activities. For example, if a vehicle requires maintenance, the system can automatically reschedule deliveries or allocate alternative transportation to minimize disruptions.
Furthermore, real-time decision-making tools can help organizations respond quickly to unexpected events or changes in production schedules. By having access to up-to-date information on maintenance activities, organizations can make informed decisions about resource allocation, prioritize maintenance tasks, and ensure the smooth functioning of the supply chain.
Conclusion
Optimizing maintenance scheduling in multi-site manufacturing operations is a complex task that requires careful planning, coordination, and the right tools. By leveraging fleet maintenance solutions, supply chain visibility, actionable insights, and efficient logistics, organizations can overcome the challenges and achieve comprehensive fleet management. With real-time data and automation, maintenance scheduling can be optimized to minimize disruptions, reduce costs, and improve overall operational efficiency.
Related Blogs
The benefits of implementing a preventive maintenance schedule for facility management
Read More