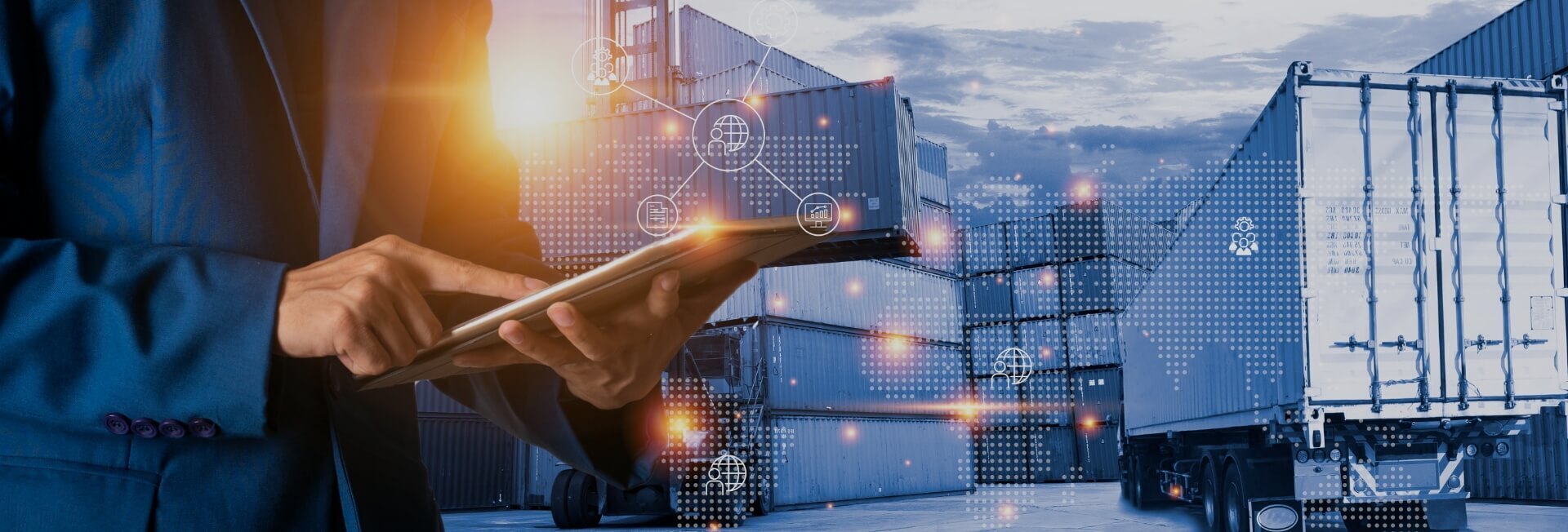
The challenges of integrating maintenance scheduling with enterprise resource planning (ERP) systems
- Home
- Resources
- Fleet Operations and Optimization
- The challenges of integrating maintenance scheduling with enterprise resource planning (ERP) systems
The Integration Challenge: Maintenance Scheduling and ERP Systems
In today's fast-paced business environment, organizations are constantly striving to optimize their operations and improve efficiency. This includes streamlining logistics, maximizing fleet performance, and ensuring timely maintenance of assets. To achieve these goals, many companies rely on enterprise resource planning (ERP) systems to manage their day-to-day operations. However, integrating maintenance scheduling with ERP systems can present significant challenges. In this article, we will explore the complexities involved in this integration and discuss potential solutions to overcome them.
The Importance of Maintenance Scheduling
Preventive maintenance is crucial for organizations that rely on fleets of vehicles or machinery to deliver their products or services. By proactively addressing maintenance needs, companies can minimize downtime, reduce repair costs, and extend the lifespan of their assets. Effective maintenance scheduling ensures that the right maintenance tasks are performed at the right time, based on factors such as usage, mileage, or time elapsed.
Traditionally, maintenance scheduling has been a manual and time-consuming process. Fleet managers or maintenance supervisors would rely on spreadsheets, paper-based records, or even memory to track maintenance needs and schedule repairs. This approach is prone to errors, delays, and oversight, leading to inefficiencies and increased costs.
With the advent of advanced technologies, maintenance scheduling has become more automated and data-driven. Fleet management software, equipped with real-time fleet data and comprehensive analytics capabilities, can now provide actionable insights to optimize maintenance schedules and improve fleet maintenance efficiency. However, integrating these systems with ERP platforms is not always seamless.
The Challenges of Integration
Integrating maintenance scheduling with ERP systems poses several challenges that organizations need to address in order to achieve efficient and streamlined operations. Let's explore some of these challenges:
1. Data Compatibility
ERP systems are designed to manage and integrate various business functions, such as finance, human resources, and supply chain management. However, they may not have the necessary features or modules to handle the complexities of maintenance scheduling. This can lead to data compatibility issues, making it difficult to sync maintenance data between the two systems. Without accurate and up-to-date data, organizations may struggle to make informed decisions and optimize their maintenance schedules.
2. Lack of Real-Time Updates
Effective maintenance scheduling requires real-time visibility into the condition and performance of assets. This allows organizations to identify maintenance needs, prioritize repairs, and allocate resources efficiently. However, many ERP systems lack the capability to provide real-time updates on asset status and maintenance requirements. This can result in delays, missed opportunities for preventive maintenance, and increased risk of breakdowns or failures.
3. Complex Workflows
Maintenance scheduling involves multiple stakeholders and complex workflows. From technicians and supervisors to procurement teams and finance departments, various individuals and departments need to collaborate and communicate to ensure smooth execution of maintenance tasks. Integrating these workflows with ERP systems can be challenging, especially when different systems or platforms are involved. The lack of integration can lead to communication gaps, delays, and errors in scheduling and executing maintenance tasks.
4. Limited Customization Options
ERP systems are often highly configurable and customizable to meet the specific needs of an organization. However, the level of customization available for maintenance scheduling may be limited. This can restrict the flexibility and adaptability of the system to accommodate unique maintenance requirements or industry-specific regulations. Organizations may find themselves limited by the capabilities of their ERP systems, leading to suboptimal maintenance scheduling and inefficient resource allocation.
Potential Solutions
While integrating maintenance scheduling with ERP systems presents challenges, there are potential solutions that can help organizations overcome these obstacles and achieve efficient and effective maintenance operations:
1. Dedicated Maintenance Management Software
Investing in dedicated maintenance management software can provide organizations with the specialized functionality they need to optimize maintenance scheduling. These software solutions are designed to integrate seamlessly with ERP systems, providing real-time updates, automated workflows, and comprehensive reporting. By leveraging such software, organizations can overcome the limitations of their ERP systems and achieve streamlined maintenance operations.
2. API Integration
Application Programming Interface (API) integration can enable seamless data exchange between maintenance scheduling software and ERP systems. APIs allow different software applications to communicate and share data in real-time, eliminating the need for manual data entry or data synchronization. By leveraging APIs, organizations can ensure that maintenance data is always up-to-date and accessible to both maintenance teams and other departments within the organization.
3. Customization and Configuration
While ERP systems may have limitations when it comes to maintenance scheduling, organizations can explore customization and configuration options to tailor the system to their specific needs. Working closely with ERP vendors or consultants, organizations can identify opportunities for customization and develop solutions that address their unique maintenance requirements. This can involve creating custom fields, workflows, or reports within the ERP system to enhance maintenance scheduling capabilities.
4. Training and Change Management
Integrating maintenance scheduling with ERP systems requires not just technical solutions, but also organizational change management. Providing comprehensive training to employees and stakeholders on the new processes, workflows, and systems is crucial to ensure successful integration. Change management strategies, such as clear communication, stakeholder engagement, and ongoing support, can help organizations overcome resistance and ensure smooth adoption of the integrated system.
Conclusion
Integrating maintenance scheduling with ERP systems is a complex endeavor that requires careful consideration of data compatibility, real-time updates, workflows, and customization options. By addressing these challenges and leveraging potential solutions, organizations can achieve efficient maintenance operations, reduce costs, and extend the lifespan of their assets. Whether through dedicated maintenance management software, API integration, customization, or change management strategies, organizations can overcome the integration challenge and reap the benefits of streamlined maintenance scheduling.
Related Blogs
The benefits of implementing a preventive maintenance schedule for facility management
Read More