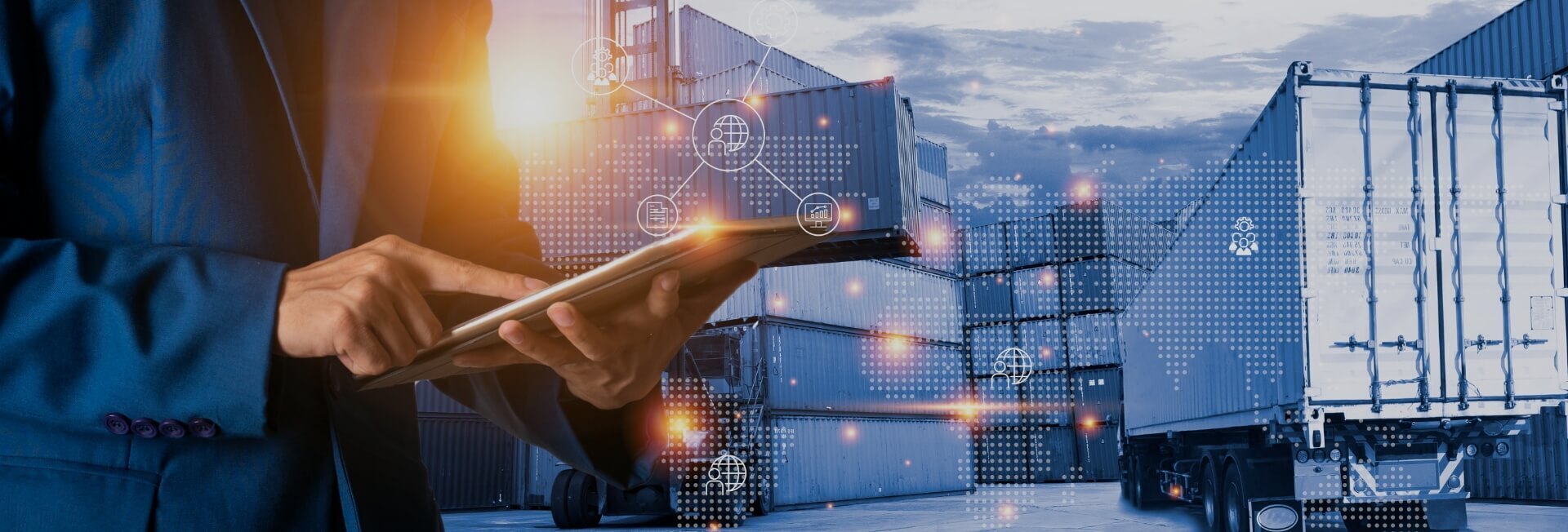
The challenges and limitations of implementing maintenance automation
- Home
- Resources
- Fleet Operations and Optimization
- The challenges and limitations of implementing maintenance automation
Introduction
As the world becomes increasingly reliant on technology and automation, industries across the board are looking for ways to streamline processes and improve efficiency. The logistics and transportation industry is no exception. With the advent of maintenance automation, fleet managers now have access to a wide range of tools and technologies that promise to optimize fleet maintenance and improve overall fleet efficiency. However, like any new technology, there are challenges and limitations that come with implementing maintenance automation. In this article, we will explore some of these challenges and limitations and discuss how fleet managers can navigate them to achieve optimal results.
The Challenge of Data Integration
One of the biggest challenges of implementing maintenance automation is the integration of data from various sources. Fleet managers rely on a plethora of data to make informed decisions about maintenance scheduling, vehicle repairs, and fleet optimization. However, this data is often scattered across different systems and platforms, making it difficult to consolidate and analyze. Without a streamlined approach to data integration, fleet managers may struggle to access real-time fleet data and make accurate, data-driven decisions.
To overcome this challenge, fleet managers need a comprehensive fleet management system that can gather data from various sources and provide actionable insights. This system should be capable of integrating with existing fleet tracking and supply chain visibility tools to ensure a seamless flow of information. By implementing a data-driven approach to fleet management, fleet managers can improve logistics efficiency and make informed decisions in real-time.
The Limitations of Predictive Maintenance
Predictive maintenance is a key component of maintenance automation and involves using data and analytics to predict when a vehicle is likely to experience a breakdown or require maintenance. By identifying potential issues before they occur, fleet managers can proactively schedule maintenance and reduce the risk of costly breakdowns and downtime.
However, predictive maintenance has its limitations. While it can provide valuable insights into the health of individual vehicles, it may not take into account external factors that can impact fleet maintenance. For example, unforeseen weather conditions or road hazards may increase the likelihood of vehicle damage and require additional maintenance. Additionally, predictive maintenance relies heavily on historical data, which may not always be indicative of future maintenance needs.
To address these limitations, fleet managers should combine predictive maintenance with preventive maintenance strategies. Preventive maintenance involves regularly scheduled maintenance tasks that are designed to prevent breakdowns and keep vehicles in optimal condition. By implementing a combination of predictive and preventive maintenance, fleet managers can maximize fleet uptime and minimize the risk of unexpected repairs.
The Complexity of Implementation
Implementing maintenance automation is not a simple task. It requires careful planning, coordination, and investment in technology and training. Fleet managers need to consider the specific needs and challenges of their fleet and identify the right tools and technologies to address them. They also need to ensure that the implementation process is seamless and does not disrupt normal fleet operations.
One of the key challenges of implementation is the need for employee training. Fleet managers and technicians need to be trained on how to use the new tools and technologies effectively. This can be a time-consuming process and may require additional resources to ensure that all employees are adequately trained.
Another challenge is the integration of new technologies with existing systems. Fleet managers need to ensure that the new tools and technologies can seamlessly integrate with their current fleet management systems, supply chain visibility tools, and other relevant platforms. This requires careful planning and coordination to avoid any disruptions or data loss during the implementation process.
The Importance of Real-Time Fleet Data
Real-time fleet data is crucial for effective maintenance automation. Fleet managers need access to up-to-date information about the health and status of their vehicles to make informed decisions about maintenance scheduling and repairs. Without real-time data, fleet managers may rely on outdated information, leading to inefficient maintenance practices and increased downtime.
To ensure real-time fleet data, fleet managers should invest in fleet tracking and telematics solutions. These solutions use GPS technology and onboard sensors to gather data about vehicle location, performance, and health in real-time. By integrating these solutions with their fleet management systems, fleet managers can access comprehensive, real-time data that enables them to make informed decisions and take proactive measures to optimize fleet maintenance.
The Need for Continuous Improvement
Maintenance automation is not a one-time solution. It requires continuous monitoring, analysis, and improvement to ensure optimal results. Fleet managers need to regularly evaluate the performance of their maintenance automation systems and identify areas for improvement.
One way to achieve continuous improvement is through the use of actionable insights. Fleet management systems should provide fleet managers with comprehensive analytics and reporting capabilities that allow them to identify trends, patterns, and areas of inefficiency. By analyzing this data, fleet managers can make informed decisions about maintenance scheduling, fleet optimization, and resource allocation.
Additionally, fleet managers should be open to feedback from technicians and other stakeholders. Technicians often have valuable insights and suggestions for improving maintenance practices and optimizing fleet efficiency. By fostering a culture of continuous improvement and encouraging collaboration, fleet managers can harness the collective knowledge and expertise of their team to drive positive change.
Conclusion
While maintenance automation offers numerous benefits for fleet managers, it is not without its challenges and limitations. From data integration and predictive maintenance to implementation complexity and the need for real-time fleet data, fleet managers need to navigate these challenges to achieve optimal results. By investing in comprehensive fleet management systems, combining predictive and preventive maintenance strategies, and continuously monitoring and improving their maintenance automation systems, fleet managers can streamline their logistics operations, improve fleet efficiency, and achieve long-term success.
Related Blogs
The benefits of implementing a preventive maintenance schedule for facility management
Read More