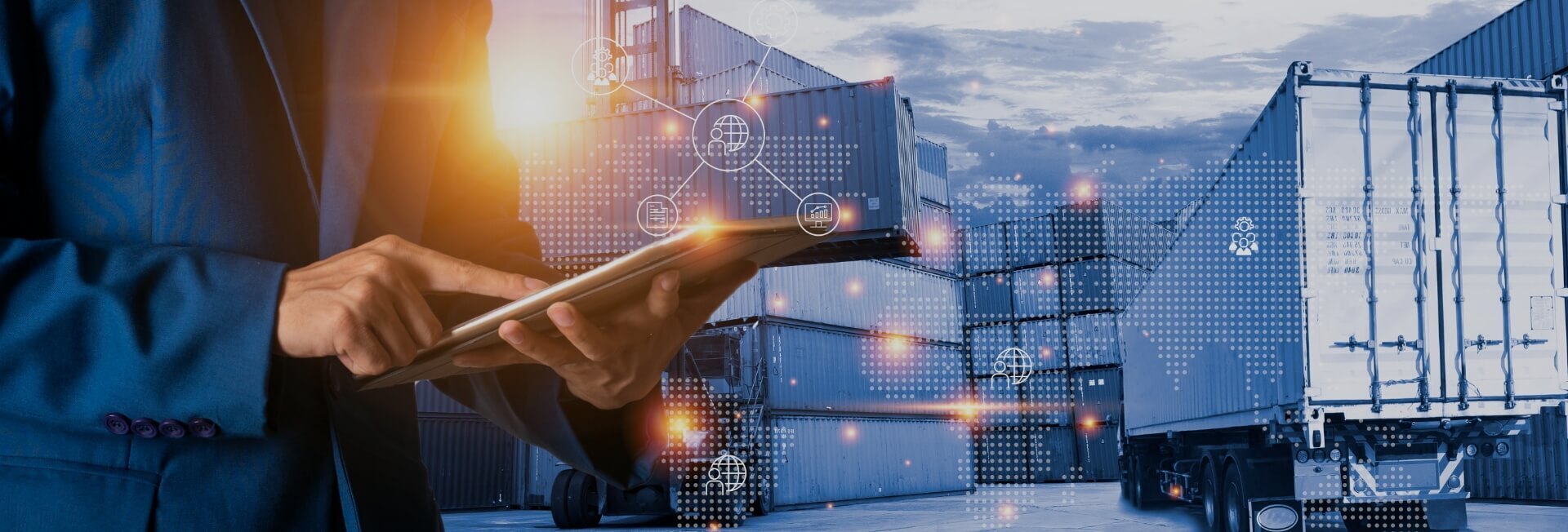
The benefits of using historical data to improve maintenance scheduling accuracy
- Home
- Resources
- Fleet Operations and Optimization
- The benefits of using historical data to improve maintenance scheduling accuracy
Effective maintenance scheduling is crucial for any organization that relies on a fleet of vehicles to keep their operations running smoothly. Without proper maintenance, vehicles can break down unexpectedly, leading to costly repairs, delays in deliveries, and unhappy customers. In order to optimize fleet maintenance and minimize downtime, many organizations are turning to historical data to improve the accuracy of their maintenance schedules. By analyzing past maintenance records and using data-driven insights, organizations can proactively identify maintenance needs, streamline their operations, and make better-informed decisions. In this article, we will explore the benefits of using historical data in improving maintenance scheduling accuracy.
Preventive Maintenance and Fleet Efficiency
Preventive maintenance is a proactive approach to vehicle maintenance that involves scheduling regular inspections, repairs, and replacements to prevent breakdowns and extend the lifespan of the vehicles. By implementing a preventive maintenance strategy based on historical data, organizations can ensure that their vehicles are always in optimal condition, reducing the likelihood of unexpected breakdowns and costly repairs.
Historical data provides valuable insights into the maintenance needs of each vehicle in the fleet. By analyzing past maintenance records, organizations can identify patterns and trends that can help them determine the optimal time for maintenance activities. For example, if a particular vehicle tends to experience frequent breakdowns after a certain mileage, the organization can schedule preventive maintenance before reaching that threshold to prevent any potential issues.
Implementing a preventive maintenance strategy based on historical data also improves fleet efficiency. By scheduling maintenance activities during periods of low demand or downtime, organizations can minimize the impact on their operations. This ensures that vehicles are available when needed and reduces the risk of delays in deliveries or disruptions to the supply chain.
Data-Driven Decision Making and Cost Savings
One of the key benefits of using historical data in maintenance scheduling is the ability to make data-driven decisions. By analyzing past maintenance records and performance data, organizations can identify areas for improvement and make informed decisions about maintenance activities.
For example, historical data can reveal which parts or components tend to fail more frequently, allowing organizations to stock up on spare parts to minimize downtime. It can also help identify vehicles that require more frequent maintenance or repairs, enabling organizations to allocate resources more efficiently.
By making data-driven decisions, organizations can also reduce maintenance costs. By identifying trends and patterns in maintenance needs, organizations can optimize their maintenance schedules, reduce the frequency of unnecessary repairs, and minimize the risk of major breakdowns. This can result in significant cost savings in terms of repair expenses, vehicle downtime, and replacement costs.
Improved Supply Chain Visibility and Optimization
Supply chain visibility is crucial for organizations that rely on efficient logistics to deliver their products or services. By using historical data to improve maintenance scheduling accuracy, organizations can gain better visibility into their supply chain and optimize their operations.
Historical data can provide insights into the performance of each vehicle in the fleet, allowing organizations to identify bottlenecks or inefficiencies in their supply chain. By analyzing past maintenance records, organizations can identify vehicles that frequently require repairs or maintenance, leading to delays in deliveries or disruptions in the supply chain. By addressing these issues proactively, organizations can optimize their logistics operations and ensure timely deliveries.
In addition, historical data can help organizations identify areas for improvement in their supply chain processes. By analyzing past maintenance records and performance data, organizations can identify trends or patterns that indicate potential areas of inefficiency. This allows organizations to take proactive measures to streamline their logistics operations, reduce costs, and improve overall supply chain performance.
Real-Time Fleet Data and Maintenance Automation
Real-time fleet data is crucial for organizations that want to optimize their maintenance scheduling and improve fleet efficiency. By integrating real-time data from telematics devices, organizations can collect and analyze data on vehicle performance, maintenance needs, and other relevant metrics.
By combining real-time fleet data with historical data, organizations can automate their maintenance scheduling processes. By setting up alerts and notifications based on predefined thresholds and patterns, organizations can proactively schedule maintenance activities, reducing the risk of breakdowns and minimizing downtime.
Maintenance automation not only improves the accuracy of maintenance scheduling but also saves time and resources. By automating routine maintenance tasks, organizations can free up their workforce to focus on more strategic activities, such as analyzing data and making data-driven decisions. This improves the overall efficiency of the maintenance process and enables organizations to optimize their fleet management operations.
Conclusion
Using historical data to improve maintenance scheduling accuracy offers numerous benefits for organizations that rely on a fleet of vehicles. By analyzing past maintenance records and using data-driven insights, organizations can implement a preventive maintenance strategy, make informed decisions, improve supply chain visibility and optimization, and automate their maintenance scheduling processes.
By leveraging historical data, organizations can optimize their fleet maintenance, reduce downtime, minimize repair costs, and ensure that their vehicles are always in optimal condition. This ultimately leads to improved operational efficiency, streamlined logistics, and enhanced customer satisfaction.
Related Blogs
The benefits of implementing a preventive maintenance schedule for facility management
Read More