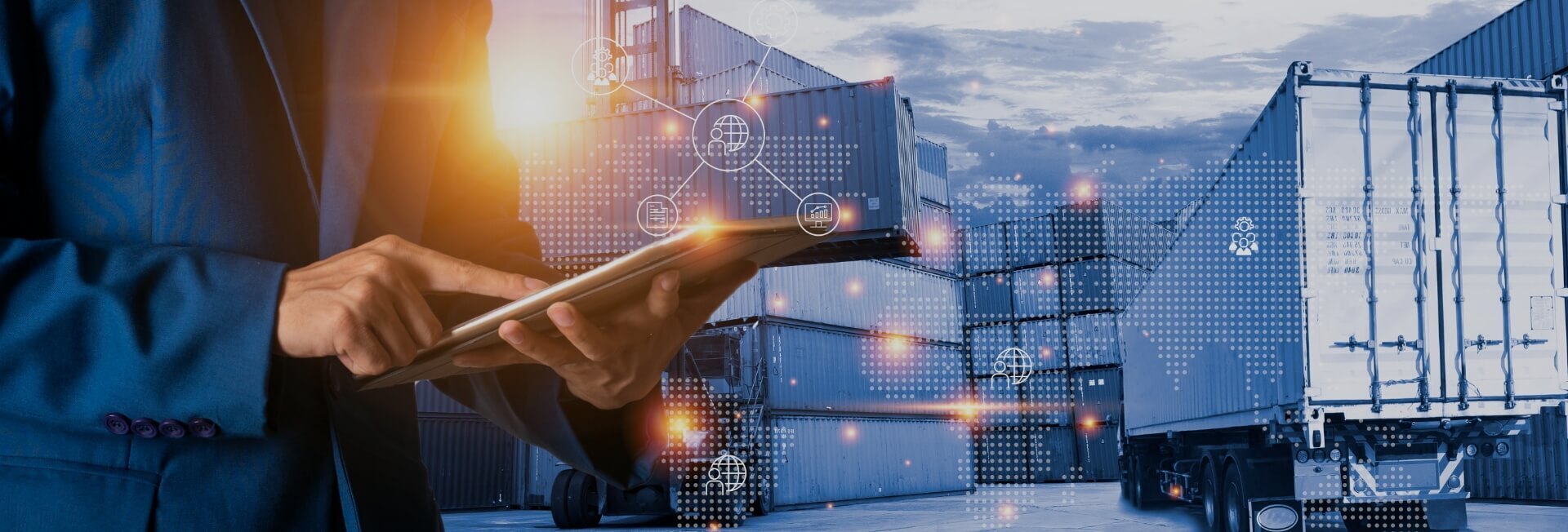
The benefits of scheduling maintenance based on equipment criticality ratings
- Home
- Resources
- Fleet Operations and Optimization
- The benefits of scheduling maintenance based on equipment criticality ratings
The Importance of Equipment Criticality Ratings in Maintenance Scheduling
Preventive maintenance is a crucial aspect of fleet management and logistics operations. By proactively addressing potential issues, companies can avoid costly breakdowns and disruptions in their supply chain. However, not all equipment requires the same level of attention and resources when it comes to maintenance. This is where equipment criticality ratings come into play.
What are Equipment Criticality Ratings?
Equipment criticality ratings are a system used to assess the importance and impact of a piece of equipment on overall operations. It helps prioritize maintenance tasks and allocate resources effectively. By assigning a criticality rating to each piece of equipment, companies can determine the level of maintenance required, frequency of inspections, and potential consequences of failure.
These ratings are often based on factors such as the equipment's role in the supply chain, its impact on production or service delivery, and the cost and time required for repairs or replacements. By considering these factors, companies can identify which equipment requires more frequent and intensive maintenance, and which can be maintained on a less frequent basis.
The Benefits of Scheduling Maintenance based on Equipment Criticality Ratings
Scheduling maintenance based on equipment criticality ratings offers several advantages for fleet management and logistics operations:
1. Improved Fleet Maintenance Efficiency
By focusing resources on the most critical equipment, companies can optimize their maintenance efforts and ensure that vital assets are in top condition. This leads to improved fleet maintenance efficiency and reduces the risk of unexpected breakdowns or failures.
Implementing a data-driven approach to maintenance scheduling allows companies to track and monitor the condition of critical equipment in real-time. This helps identify potential issues before they escalate and make informed decisions about when and how to perform maintenance tasks.
2. Enhanced Supply Chain Visibility and Optimization
Equipment criticality ratings also contribute to supply chain visibility and optimization. By understanding the criticality of each piece of equipment, companies can identify potential bottlenecks and vulnerabilities in their supply chain. This allows them to take proactive measures to mitigate risks and ensure a smooth flow of goods and services.
With the help of fleet tracking and comprehensive fleet management solutions, companies can gather real-time data on their equipment's performance and condition. This data, combined with equipment criticality ratings, provides actionable insights for optimizing the supply chain and streamlining logistics operations.
3. Cost Savings through Maintenance Automation
Maintenance automation plays a crucial role in optimizing fleet maintenance and reducing costs. By utilizing equipment criticality ratings, companies can automate maintenance scheduling and allocate resources efficiently.
Through the use of sensors, IoT devices, and real-time fleet data, companies can monitor the condition of critical equipment and automatically generate maintenance tasks when required. This eliminates the need for manual inspections and reduces the risk of human error. It also allows companies to prioritize maintenance based on equipment criticality ratings, ensuring that resources are allocated to the most important assets.
By automating maintenance scheduling, companies can also reduce downtime and improve operational efficiency. Unplanned breakdowns and repairs can be minimized, resulting in significant cost savings and increased productivity.
4. Real-Time Decision-Making and Actionable Insights
Equipment criticality ratings, combined with real-time fleet data, enable companies to make informed decisions and take timely actions. By continuously monitoring the condition of critical equipment, companies can identify potential issues, analyze trends, and make data-driven decisions on maintenance tasks.
Real-time fleet data provides valuable insights into equipment performance, allowing companies to optimize maintenance schedules and avoid unnecessary repairs or replacements. By leveraging this data, companies can improve their overall fleet efficiency and reduce costs associated with maintenance and vehicle repairs.
Conclusion
Scheduling maintenance based on equipment criticality ratings is a proactive approach that helps companies optimize their fleet management and logistics operations. By prioritizing maintenance tasks and allocating resources efficiently, companies can enhance fleet maintenance efficiency, improve supply chain visibility and optimization, reduce costs through maintenance automation, and make real-time data-driven decisions.
Implementing comprehensive fleet management solutions and leveraging real-time fleet data allows companies to gain a competitive edge in today's fast-paced business environment. By focusing on equipment criticality ratings, companies can ensure that their assets are well-maintained, minimize the risk of unexpected breakdowns, and achieve streamlined logistics operations and supply chain visibility.
Related Blogs
The benefits of implementing a preventive maintenance schedule for facility management
Read More