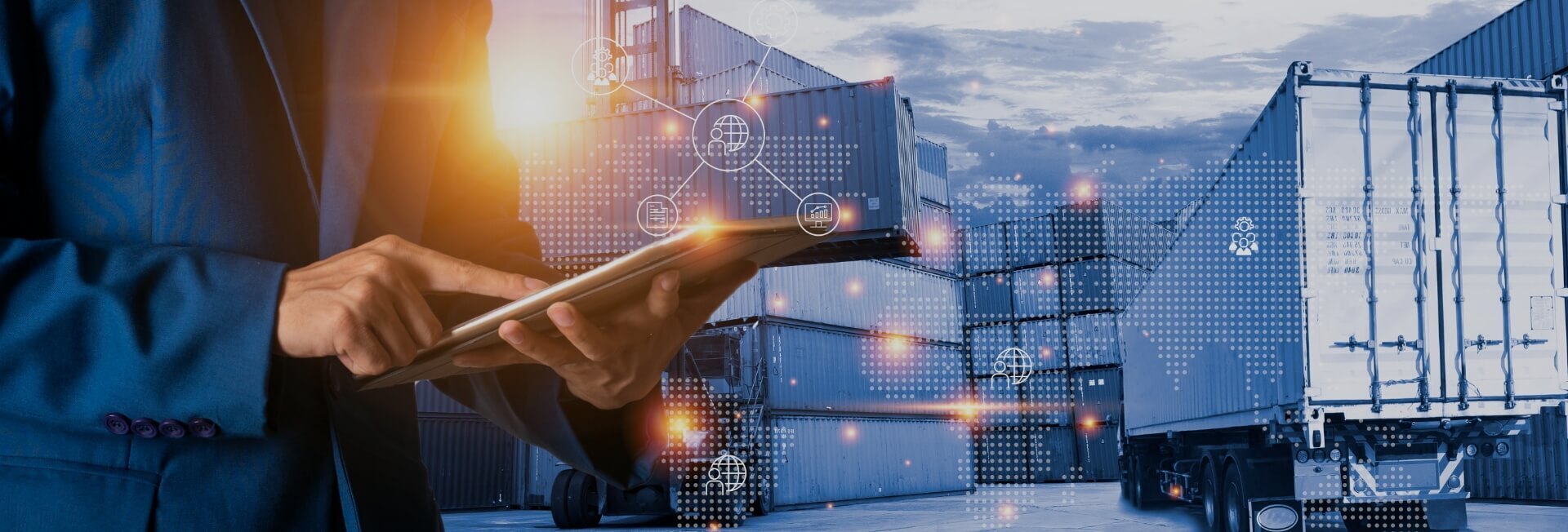
The benefits of implementing a predictive maintenance scheduling approach in the oil and gas industry
- Home
- Resources
- Fleet Operations and Optimization
- The benefits of implementing a predictive maintenance scheduling approach in the oil and gas industry
The Benefits of Implementing Predictive Maintenance Scheduling in the Oil and Gas Industry
In the oil and gas industry, fleet maintenance plays a crucial role in ensuring the smooth operation of vehicles and equipment. With a large number of vehicles and machinery involved, it is essential to have an effective maintenance strategy in place to minimize downtime, optimize resources, and reduce costs. One approach that has gained significant traction in recent years is predictive maintenance scheduling.
What is Predictive Maintenance Scheduling?
Predictive maintenance scheduling is a proactive approach to fleet maintenance that leverages data and analytics to predict and prevent equipment failures. By continuously monitoring the condition of vehicles and equipment, maintenance tasks can be scheduled based on their actual needs rather than relying on fixed time intervals or reactive repairs.
This data-driven approach allows fleet managers to identify potential issues before they escalate into costly breakdowns or safety hazards. By using advanced technologies such as IoT sensors, telematics, and predictive analytics, fleet managers can access real-time data on the health and performance of their assets. This enables them to make informed decisions and take proactive steps to prevent failures and optimize maintenance schedules.
The Benefits of Predictive Maintenance Scheduling
Implementing a predictive maintenance scheduling approach in the oil and gas industry offers several key benefits:
1. Improved Fleet Maintenance Efficiency
Predictive maintenance scheduling allows fleet managers to optimize maintenance tasks based on actual equipment conditions. By identifying potential issues in advance, maintenance can be scheduled during planned downtime, minimizing disruptions to operations.
For example, if a vehicle's sensor detects abnormal vibrations in the engine, it can trigger an alert for maintenance. The fleet manager can then schedule a maintenance check during the vehicle's next planned maintenance window, ensuring minimal impact on operations.
This proactive approach reduces the likelihood of unexpected breakdowns and allows for more efficient use of resources. Instead of allocating resources to reactive repairs, fleet managers can focus on preventive actions that address the root causes of failures.
2. Cost Savings through Reduced Vehicle Repairs
By implementing predictive maintenance scheduling, fleet managers can significantly reduce the occurrence of costly vehicle repairs. By addressing potential issues before they escalate, fleet managers can avoid major breakdowns that require extensive repairs or even vehicle replacements.
For example, if a vehicle's sensor detects a decrease in oil pressure, it can indicate a potential issue with the engine. By scheduling maintenance to address the issue promptly, fleet managers can prevent further damage and avoid the need for expensive repairs or engine replacements.
These proactive maintenance actions not only save on repair costs but also extend the lifespan of vehicles and equipment, maximizing their return on investment.
3. Enhanced Safety and Compliance
In the oil and gas industry, safety is of paramount importance. The implementation of predictive maintenance scheduling can help ensure that vehicles and equipment are in optimal condition, reducing the risk of accidents and injuries.
By continuously monitoring key performance indicators and detecting potential issues, fleet managers can take proactive measures to address safety concerns. For example, if a vehicle's sensor detects abnormal brake performance, maintenance can be scheduled to replace worn-out brake pads, reducing the risk of brake failure on the road.
Predictive maintenance scheduling also helps ensure compliance with safety and environmental regulations. By addressing maintenance issues promptly, fleet managers can avoid violations and penalties associated with non-compliance.
4. Increased Operational Efficiency
By implementing a predictive maintenance scheduling approach, fleet managers can streamline logistics and improve operational efficiency. With real-time data on the health and performance of vehicles and equipment, fleet managers can make data-driven decisions to optimize routes, schedules, and resource allocation.
For example, if a vehicle's sensor detects a potential issue that may require maintenance, the fleet manager can adjust the vehicle's schedule to avoid critical operations or high-demand periods. By avoiding unscheduled downtime, fleet managers can ensure that vehicles are available when needed, improving overall productivity.
Furthermore, predictive maintenance scheduling allows for better planning of maintenance activities, reducing the need for last-minute repairs and minimizing disruptions to operations. This streamlined approach leads to improved customer satisfaction and increased profitability.
Conclusion
Implementing a predictive maintenance scheduling approach in the oil and gas industry offers numerous benefits, including improved fleet maintenance efficiency, cost savings through reduced vehicle repairs, enhanced safety and compliance, and increased operational efficiency.
By leveraging real-time fleet data and actionable insights, fleet managers can make data-driven decisions to optimize maintenance schedules, prevent equipment failures, and streamline logistics. This results in improved fleet management, increased operational efficiency, and ultimately, a competitive advantage in the oil and gas industry.
Related Blogs
The benefits of implementing a preventive maintenance schedule for facility management
Read More